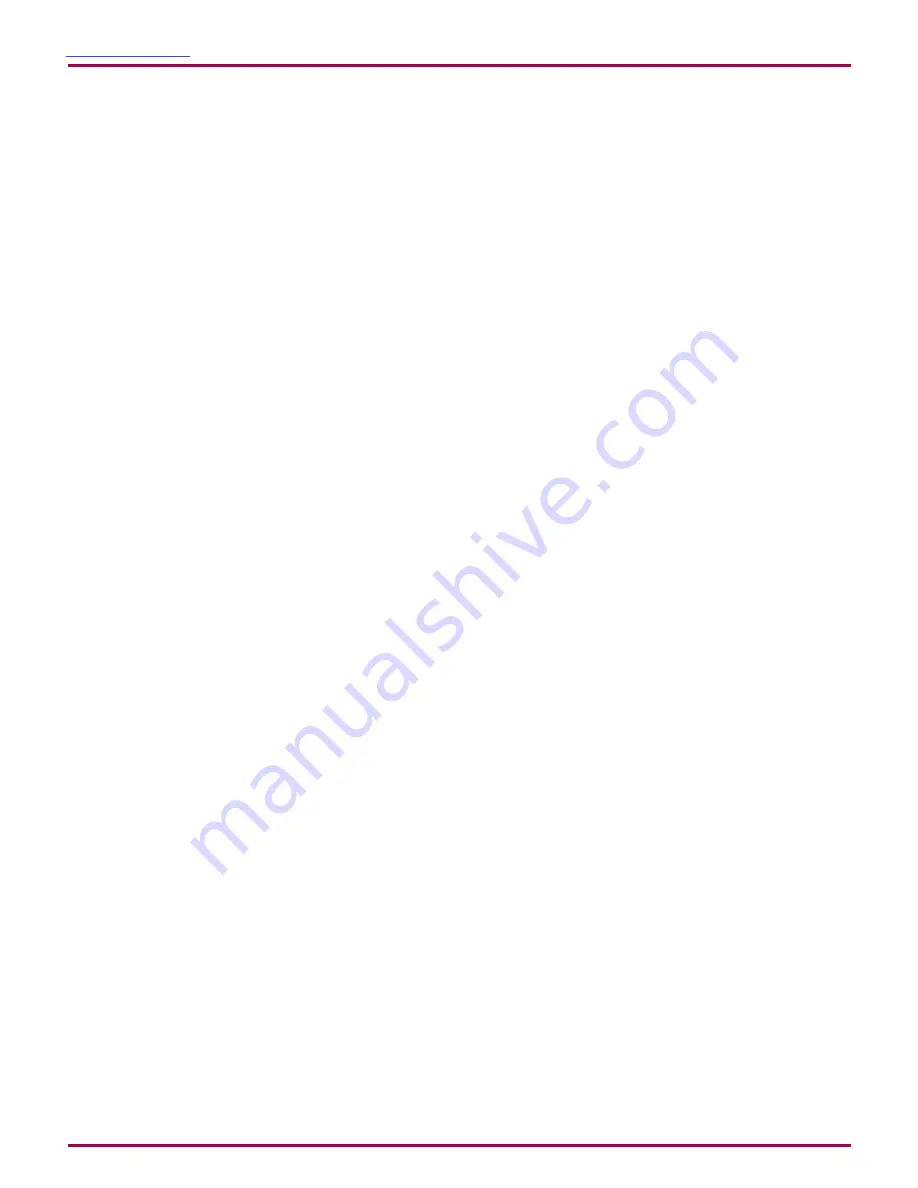
Deadband would be between 95 and 105 cc/min. The
PID controller would therefore be suspended whenever
the actual flow rate is within this range. This parameter
should normally be set to 1 cc/min.
Proportional Gain (Kp) (Master and Slave)
The proportional PID controller gain mainly affects the
response of the DynaFlow system to disturbances. The
DynaFlow system may operate with Kp at zero, however
response to material supply and delivery pressure distur-
bances will be poor. The value of Kp is divided internally
by a factor of 1,000 and is used as a multiplier for the flow
rate error term. The flow rate error term is the difference
between the set point and actual flow rate for the CHANNEL.
Integral Gain (Ki) (Master and Slave)
The integral PID controller gain mainly affects the steady-
state (non-transitional) response of the DynaFlow system.
The DynaFlow system must have a non-zero value for Ki
to operate properly.
The valve of Ki is divided internally by a factor of 100,000
and is used as a multiplier, along with a factor of 3, for the
sum of the error term over the time the trigger has been
turned on.
Derivative Gain (Kd) (Master and Slave)
The differential PID controller gain mainly affects the re-
sponse of the DynaFlow system to disturbances caused
by disturbances that are slow in nature. Normally, the
DynaFlow system may operate with a Kd value of zero.
The value of Kd is divided internally by a factor of 1,000
and is used as a multiplier, along with a factor of 1/3, for
the rate of change in the error term.
flow meters should be periodically checked. The rheology
of some fluids may effect the calibration values, therefore
a different value for pulses per liter may be used for each
material and is entered into the JOB data tables.
Deadband (Master and Slave)
This represents a flow rate range divided equally above
and below the set point flow rate in which the PID controll
is suspended. This keeps the control output from contin-
ually changing and produces stability when close to the
requested value. For example, if the Deadband is set for
5 cc/min and flow rate set point is set for 100 cc/min, the
DIAGNOSTIC PARAMETERS (F5)
The following parameters are available in the Local Operator
Interface program as diagnostic parameters.
Force CHANNEL Digital Inputs
Forcing inputs permits debugging and trouble-shooting
to determine proper operation of the hardware. Each
CHANNEL input can be forced ON therefore not requiring
a hardware signal for that input to become active. If an
external hardware input is present, a forced OFF command
will have no effect unless the hardware input is removed.
Force CHANNEL Digital Outputs
Forcing outputs permits debugging and trouble-shooting
to determine proper operation of the hardware.
Force CHANNEL Analog Outputs
Forcing analog outputs permits debugging and trouble-
shooting to determine proper operation of the hardware.
PLOT DATA (F6)
This feature allows the operator to generate a real-time
graph of many of the process variables to monitor the
response of the system as it relates to time. Up to four
variables from any of the configured guns can be graphed
at any one time. All four variable do not have to be from the
same gun. (e.g. The triggers from 4 guns can be monitored
at the same time.)
The following variables can be graphed:
- Trigger
- Requested Ratio
- Actual Ratio
- Requested Flow (both channels)
- Actual Flow (both channels)
- Requested Flow (Chan. A & B)
- Actual Flow (Chan. A & B)
- Control Pressure (Chan. A & B)
To select the data to be graphed, simply touch the Plot Data
button (F6) then touch the items you wish to plot one at a
time followed by touching the Select Variable button (F1).
(Up to four items can
LN-9400-00-R11 (08/2018)
36 / 96
www.carlisleft.com
OPERATION