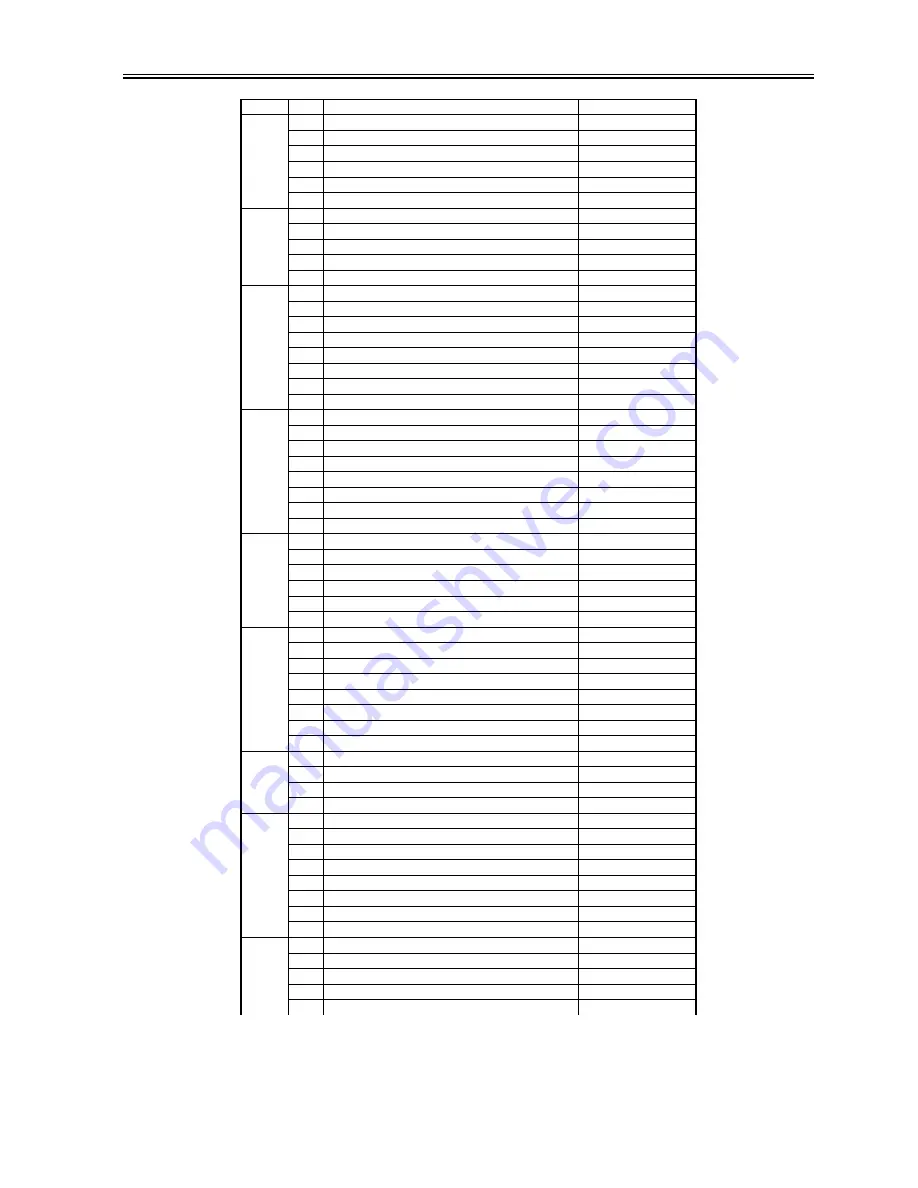
Chapter 16
16-19
P034
0
saddle inlet solenoid
1: ON
1
saddle No. 1 flapper solenoid
1: ON
2
saddle No. 2 flapper solenoid
1: ON
3
saddle pickup solenoid
1: ON
4-6
not used
7
saddle inlet sensor
1: detected
P035
0
saddle rear stapler CW (CW)
0: ON
1
saddle rear stapler CCW (CCW)
0: ON
2
saddle front stapler CW (CW)
0: ON
3
chip select (CS1*)
4-7
not used
P036
0
DIPSW_1
0: ON
1
DIPSW_2
0: ON
2
DIPSW_3
0: ON
3
DIPSW_4
0: ON
4
DIPSW_5
0: ON
5
DIPSW_6
0: ON
6
DIPSW_7
0: ON
7
DIPSW_8
0: ON
P037
0
not used
1
PUSHSW1
0: ON
2
5V detection signal
0: detected
3
24V detection signal
0: detected
4
for revision control
5
for revision control
6
for revision control
7
for revision control
P038
0
download ON signal
1: ON
1
not used
4
LED3
0: ON
5
LED2
0: ON
6
LED1
0: ON
7
power-on signal
0: ON
P039
0
DIPSW1
0: ON
1
DIPSW2
0: ON
2
DIPSW3
0: ON
3
not used
4
PCH-OUT
5
trailing edge sensor
1: ON
6
punch encoder lock
7
punch HP sensor
0: detected
P040
0
PCH-IN
1
RxD
2
TxD
3-7
not used
P041
0
EEPROM-IN
1
EEPROM-OUT
2
EEPROM-CLK
3
EEPROM-CS
4
horizontal registration HP sensor
1: ON
5
horizontal registration motor STB
0: ON
6
punch motor CCW
0: ON
7
punch motor CW
0: ON
P042
0-3
not used
4
DIPSW4
0: ON
5
horizontal registration motor CUR
0: ON
6
PWM
7
not used
Address
bit
Description
Remarks
Summary of Contents for iR6570 series
Page 1: ...Mar 29 2005 Service Manual iR6570 5570 Series...
Page 2: ......
Page 6: ......
Page 26: ...Contents...
Page 27: ...Chapter 1 Introduction...
Page 28: ......
Page 30: ......
Page 55: ...Chapter 2 Installation...
Page 56: ......
Page 58: ...Contents 2 9 3 Mounting the Cassette Heater 2 34...
Page 98: ......
Page 99: ...Chapter 3 Basic Operation...
Page 100: ......
Page 102: ......
Page 110: ......
Page 111: ...Chapter 4 Main Controller...
Page 112: ......
Page 114: ......
Page 135: ...Chapter 5 Original Exposure System...
Page 136: ......
Page 181: ...Chapter 6 Laser Exposure...
Page 182: ......
Page 184: ......
Page 192: ......
Page 193: ...Chapter 7 Image Formation...
Page 194: ......
Page 198: ......
Page 259: ...Chapter 8 Pickup Feeding System...
Page 260: ......
Page 350: ......
Page 351: ...Chapter 9 Fixing System...
Page 352: ......
Page 401: ...Chapter 10 External and Controls...
Page 402: ......
Page 406: ......
Page 448: ......
Page 449: ...Chapter 11 MEAP...
Page 450: ......
Page 452: ......
Page 455: ...Chapter 12 Maintenance and Inspection...
Page 456: ......
Page 458: ......
Page 468: ......
Page 469: ...Chapter 13 Standards and Adjustments...
Page 470: ......
Page 505: ...Chapter 14 Correcting Faulty Images...
Page 506: ......
Page 508: ......
Page 537: ...Chapter 15 Self Diagnosis...
Page 538: ......
Page 540: ......
Page 565: ...Chapter 16 Service Mode...
Page 566: ......
Page 568: ......
Page 633: ...Chapter 17 Upgrading...
Page 634: ......
Page 636: ......
Page 641: ...Chapter 17 17 5 F 17 4 HDD Boot ROM Flash ROM System Software...
Page 646: ...Chapter 17 17 10 F 17 11 8 Click START F 17 12...
Page 675: ...Chapter 17 17 39 F 17 59 2 Select the data to download F 17 60 3 Click Start...
Page 677: ...Chapter 18 Service Tools...
Page 678: ......
Page 680: ......
Page 683: ...Mar 29 2005...
Page 684: ......