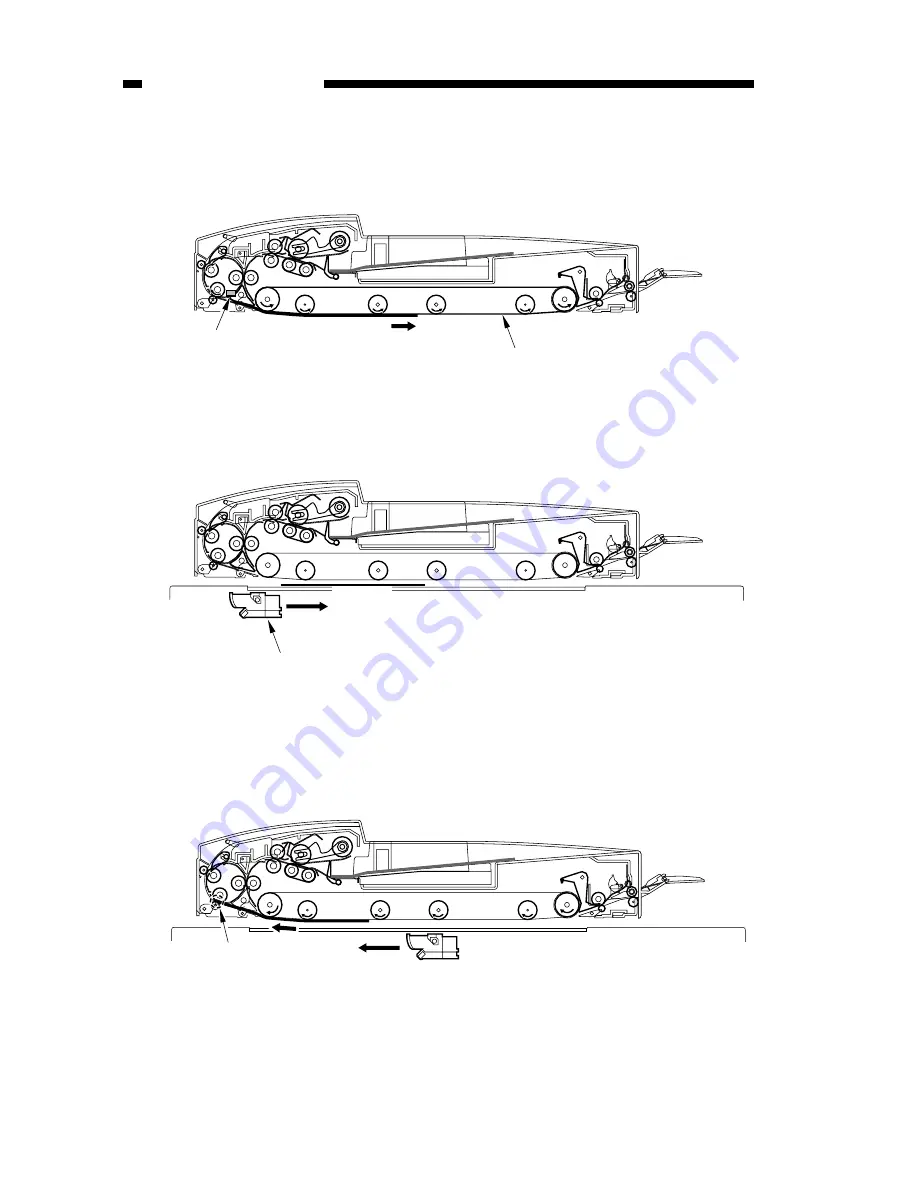
2-56
COPYRIGHT © 1999 CANON INC.
CANON ADF FOR iR600 REV.0 JAN. 1999 PRINTED IN JAPAN (IMPRIME AU JAPON)
CHAPTER 2 OPERATIONS
3] The reversing roller and the feeding belt are rotated to move the original.
The feeding belt is rotated after the trailing edge of the first original has moved past the reversal
sensor (S1), and the original is stopped.
Figure 2-258
4] The copier starts to make a copy by moving its scanner.
Figure 2-259
5] When the copier's scanner starts to move in reverse, the feeding belt is rotated to move the first
original to the reversing assembly. At this time, the leading edge of the original is butted against
the reversing roller to remove the skew.
Figure 2-260
Reversal sensor (S1)
Feeding belt
Copy
Scanning lamp
Butted.