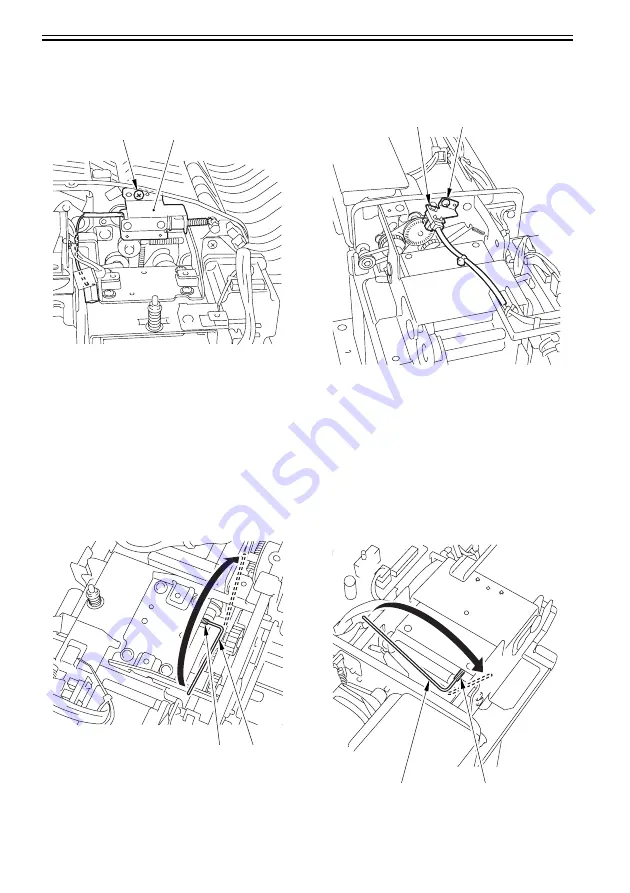
Chapter 5
5-36
B. How to Adjust the Pressure of Hinge Spring
1. Hinge (left)
1) Unscrew a screw [1] and detach and pre-reversal
solenoid mount [2].
F-5-113
2) Rotate the spring pressure adjusting screw [A] of
the hinge to the direction of the arrow [B] (in a
clockwise direction) using a hex wrench 18 times
by 60 degrees (Max. angle to be rotated per time)
per time (Shorten the spring pressure adjusting
screw [A] by 2 mm).
F-5-114
2. Hinge (right)
1) Unscrew a screw [1] and detach the delivery
motor clock sensor mount [2].
F-5-115
2) Rotate the spring pressure adjusting screw [A] of
the hinge to the direction of the arrow [B] (in a
clockwise direction) using a hex wrench 18 times
by 60 degrees (Max. angle to be rotated per time)
per time (Shorten the spring pressure adjusting
screw [A] by 2 mm).
F-5-116
[1]
[2]
[1]
[2]
[1]
[2]
[1]
[2]
Summary of Contents for DADF-R1
Page 2: ......
Page 4: ......
Page 12: ...Contents 6 3 Alam Code 6 6 6 3 1 List of Alarm Code 6 6 ...
Page 13: ...Chapter 1 SPECIFICATIONS ...
Page 14: ......
Page 16: ......
Page 22: ......
Page 23: ...Chapter 2 INSTALLATION ...
Page 24: ......
Page 26: ......
Page 55: ...FUNCTIONS Chapter 3 ...
Page 56: ......
Page 67: ...Chapter 3 3 9 F 3 11 Reversing Copying the 2nd side Delivering From previous page ...
Page 121: ...PARTS REPLACEMENT PROCEDURE Chapter 4 ...
Page 122: ......
Page 124: ......
Page 145: ...MAINTENANCE Chapter 5 ...
Page 146: ......
Page 200: ......
Page 201: ...ERROR CODE Chapter 6 ...
Page 202: ......
Page 204: ......
Page 211: ...APPENDIX ...
Page 212: ......
Page 221: ......
Page 222: ......