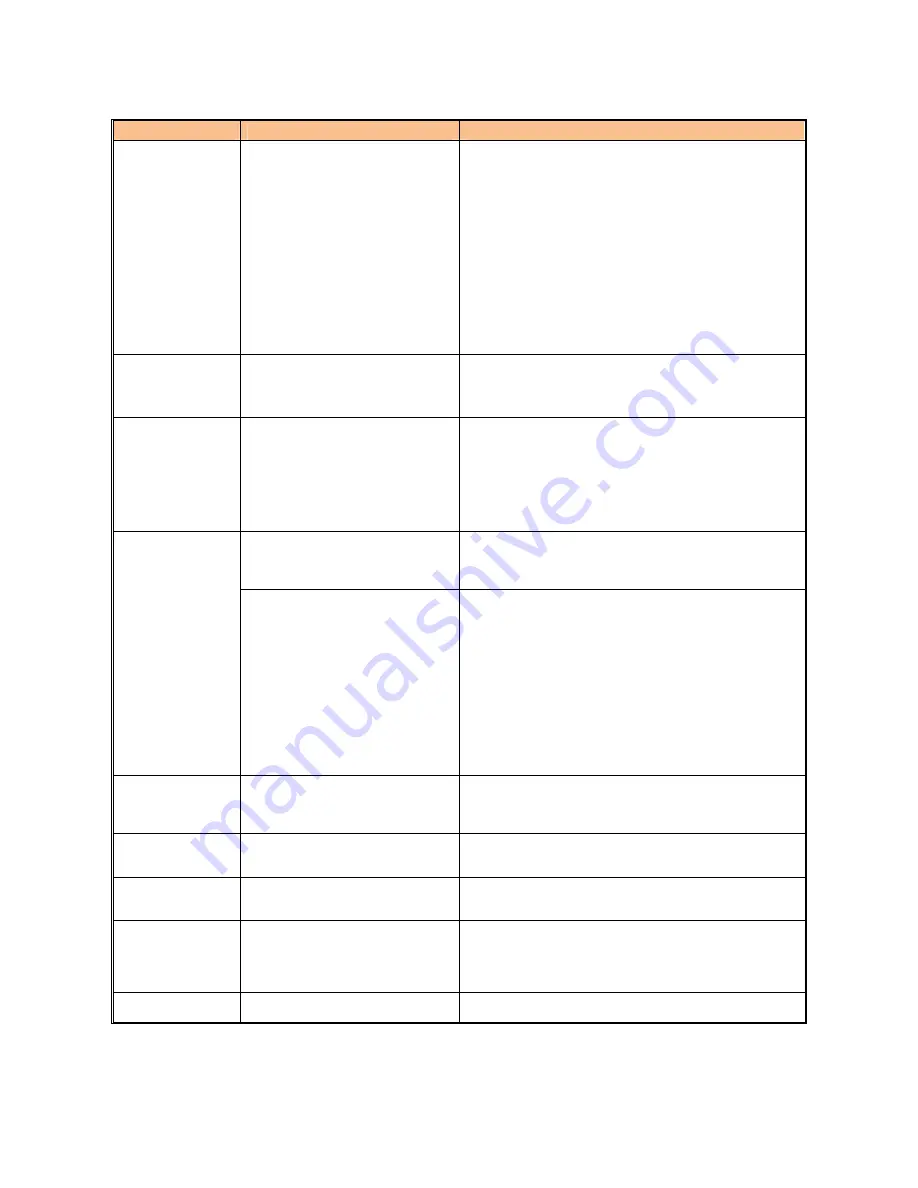
32
SYMPTOM
FAILURE MODE
ANALYSIS
Manual Reset High
Limit Trips
(Pressing the
manual RESET on
the TH Control
Panel will be
required to restart
the ignition
sequence)
• Manual Reset Safety High Limit
tripped, supply/outlet temperature
in excess of 210
o
F
• Alert: 303-310
• Verify that the capillary tube is broken. If this is the case,
replace Manual Reset High Limit
• Verify that the system is full of water and that all air has
been properly purged from the system.
• Verify that the boiler is piped properly. Refer to Piping
Diagrams in Section 12 of this manual.
• Verify that 120 VAC is being supplied to the boiler pump
on a call for heat. If voltage cannot be detected check
wiring.
• Verify that the pump is circulating when 120 VAC is
supplied. If so, pump impeller may be stuck. Use a flat
head screwdriver on face of pump to turn impeller
manually.
• If 120 VAC is present during a call for heat, but the pump
still does not circulate, replace pump.
Fan Speed Too
Low
• Actual fan RPM is 30% slower than
target fan speed.
• Alert: 60, 76
• Verify wiring connections at the fan and TH Controller.
• Replace the fan
• Replace the TH Controller.
Fan Speed Too
High
• Actual fan RPM is 30% faster than
what is required.
• Alert: 59, 75
• Vent/ Air Inlet Lengths exceed the maximum allowed
equivalent lengths. Refer to Air Inlet and Venting Section
in Part 2 of this manual.
• Verify that there are no obstructions in the vent/ air inlet
pipes or at terminations
• Verify wiring connections at the fan and TH Controller.
• Replace the fan
• Replace the TH Controller.
Temperature
Overshoot
• Stack temperature has exceeded
the limit set on the boiler.
• Lockout: 82
• The stack temperature has exceeded the maximum
temperature allowed.
• Measure the resistance of the flue sensor at room
temperature, it should be approximately 10k
Ω
.
• The supply/outlet temperature has
exceeded the setpoint
temperature specified.
• Alert: 79
• Verify that the system is full of water and that all air has
been properly purged from the system
• Verify that the boiler is piped properly. Refer to Piping
Diagrams in Section 12 of this manual
• Verify that 120 VAC is being supplied to the heater pump
on a call for heat. If voltage cannot be detected check
wiring
• Verify that the pump is circulating when 120 VAC is
supplied. If so, pump impeller may be stuck. Use a flat
head screwdriver on face of pump to turn impeller manually
• If 120 VAC is present during a call for heat, but the pump
still does not circulate, replace the pump.
• Replace the TH Controller, if necessary.
Sensor Not
Connected
•Supply/ Outlet sensor, Alert: 92
•Return/ Inlet sensor, Alert: 91
•Flue sensor, Alert: 95
•DHW sensor, Alert: 93
• Verify that the sensors are connected
• Verify that they are wired correctly.
• Measure the resistance of the sensors, 10k
Ω
sensors.
• Replace the sensor if necessary
Fan Not Turning
• Fan refuses to rotate
• Check fan power wires
• Fan signal wires are interchanged
• Minimum fan speed must be greater than 1500 RPM
Air Switch
• Blocked flue error
• Alert: 67
• Air Switch wire(s) is/are loose
• Air Switch is set too tight, reduce sensitivity by turning
screw ¼ turn clockwise.
Flame Detection is
out of Sync
• Flame detection is present when no
visible signs of a flame exist
• Lockout: 105, 158
• Verify supply voltage for proper polarity.
• Check external wiring for voltage feedback
• Check internal wiring for proper connections
• Check the flame sensor and verify that it is clean
• Replace TH Controller
Blank Display
Screen
• Blank display screen
• Check wire connections from TH Controller to DyanMax
display