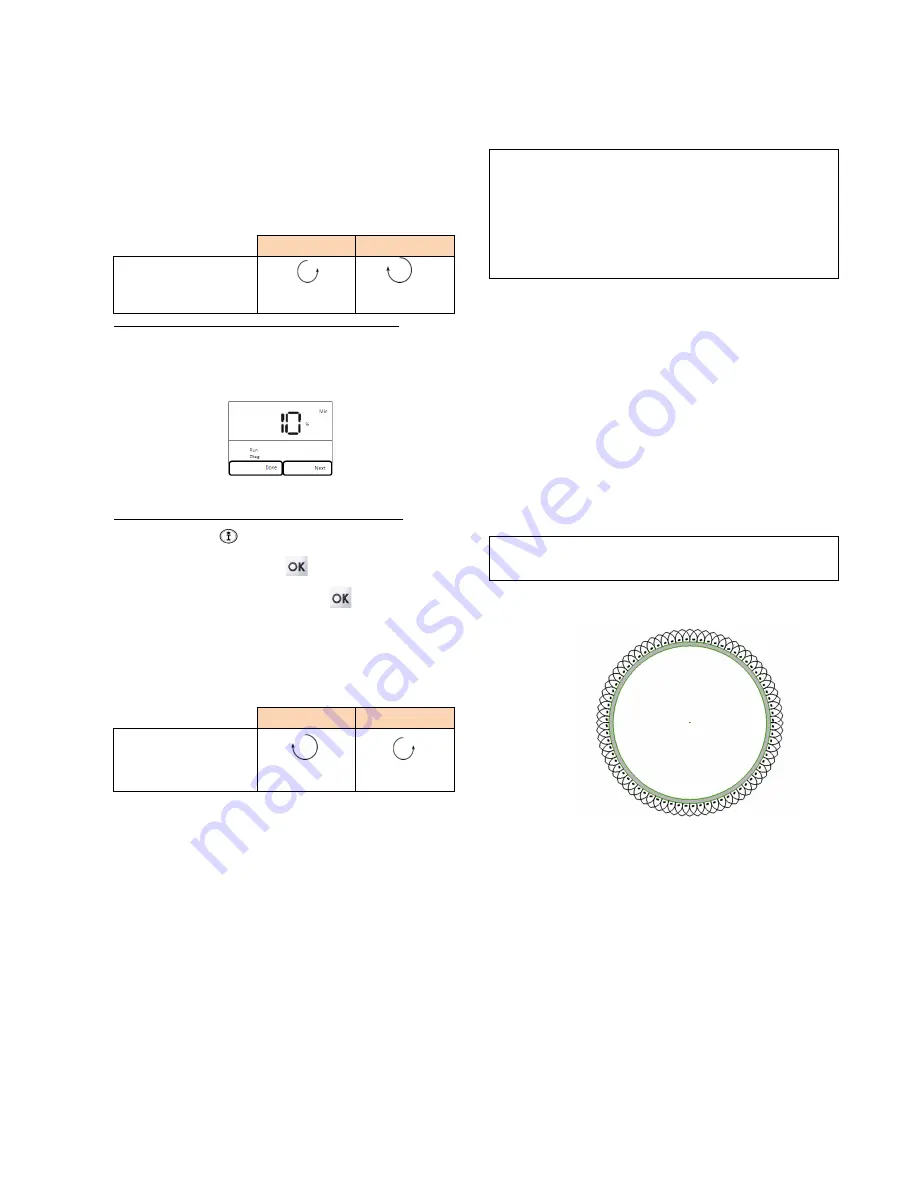
40
4) Select Set High Fire
Locate the input adjustment screw on the top side of the gas
valve. Turn the screw 1/8 turn in either way for each
adjustment to keep track of the adjustments. After adjusting
the screw wait a moment for the combustion levels to
stabilize before attempting to make any further adjustments.
Continue this procedure until combustion levels are satisfied.
Increase CO2
Decrease CO2
High Fire Adjustment
Counter-Clock
Wise
Clockwise
To adjust the low fire setting on the standard display
Press and hold the ‘Next’ button for 3 seconds to enter the
diagnostic menu on the TH Control Panel. Press ‘Next’ until
the following screen appears:
Figure 33: Low Fire Adjustment Screen
To return to normal operation press ‘Done’.
To adjust the low fire setting on the upgraded display
5) Press the
button
6) Select Test and press
7) Select Forced Rate and press
8) Select Set Low Fire
The TH should respond immediately and fire at 1500 RPM.
When this is achieved locate the low fire adjustment screw.
When the correct combustion values are achieved replace
the screw cap back on to the gas valve.
Increase CO2
Decrease CO2
Low Fire Adjustment
Clockwise
Counter-Clock
Wise
PART 10 MAINTENANCE
CAUTION
It is important that all gas appliances be serviced by a
qualified technician trained by Camus Hydronics. It is in your
own interest and that of safety to ensure that all local codes,
and all the “NOTES” and “WARNINGS” in this manual are
complied with. To service or adjust this appliance, it is
imperative that the serviceman utilize a combustion analyzer
to read CO
2
and CO according to Camus Hydronics
recommendations.
Listed below are items that must be checked to ensure safe
reliable operations. Verify proper operation after servicing.
10.1
EXAMINE THE VENTING SYSTEM
Examine the venting system at least once a year. Check
more often in the first year to determine inspection interval.
Check all joints and pipe connections for tightness, corrosion
or deterioration. Flush the condensate drain hose with water
to clean. Clean screens in the venting air inlet system as
required. Have the entire system, including the venting
system, periodically inspected by a qualified service agency.
10.2
VISUALLY CHECK MAIN BURNER FLAMES
At each start up after long shutdown periods or at least every
six months. A burner view port is located on the combustion
chamber front door.
CAUTION
The area around the burner view port is hot and direct
contact could result in burns
Figure 34: Normal Burner Flame Profile (short dense and
blue)
•
Normal Flame: A normal flame at 100% of burner input
is blue, with a well defined flame and no flame lifting.
•
Yellow Tip: Yellow tipping can be caused by blockage
or partial obstruction of air flow to the burner.
•
Yellow Flames: Yellow flames can be caused by
blockage of primary air flow to the burner or excessive
gas input. This condition MUST be corrected
immediately.
If improper flame is observed, examine the venting system;
ensure proper gas supply and adequate supply of
combustion and ventilation air.