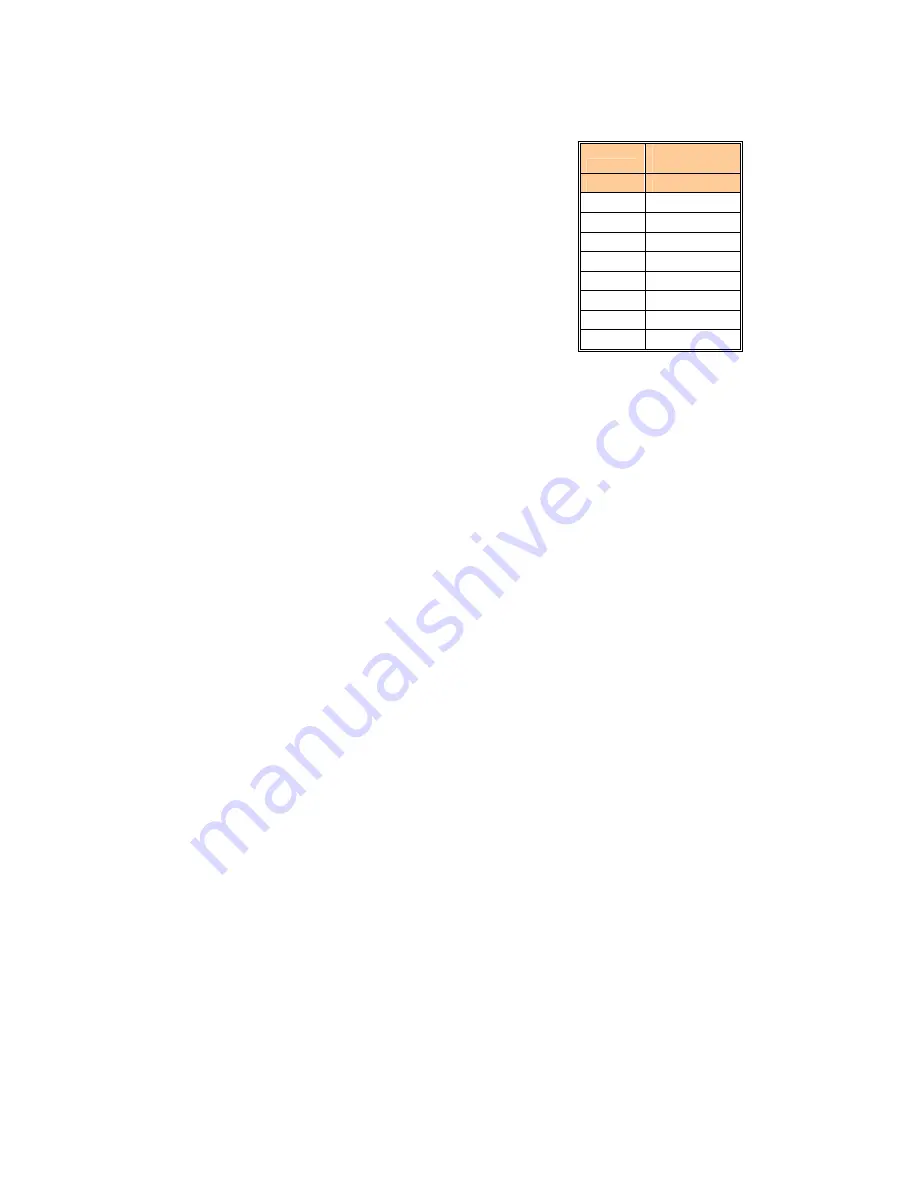
15
PART 4
WATER CONNECTION
•
Check all applicable local heating, plumbing and
building safety codes before proceeding.
•
If the appliance is installed above radiation level it must
be provided with a low water cut-off device at the time
of appliance installation (available from Camus). Some
local codes require the installation of a low water cut-
off on all systems.
•
A temperature and pressure relief valve is supplied
with each TH. The relief valve must be mounted in a
vertical position and piped to the floor in a manner
acceptable to the enforcing authority.
•
Be sure to provide unions and gate valves at inlet and
outlet to the appliance so that it can be easily isolated
for service.
•
This appliance is a low mass stainless steel tube
design which provides for instant heat transfer. All
appliances are supplied with an internal suitable
specific pump mounted in place. When replacing the
pump, replace with one of equal or better-performance.
•
An air vent is supplied on the heat exchanger header
to eliminate trapped air. Install venting devices at high
points in the system as well to eliminate trapped air in
the piping.
•
Use suitable pipe hangers or floor stands to support
the weight of all water and gas piping.
•
The TH must be installed so that the gas ignition
system components are protected from water
(dripping, spraying, rain, etc.) during appliance
operation and service (circulator replacement, control
replacement, etc.)
•
Pipe cold water supply below hot water connection to
prevent heat migration during times of low heat
demand
4.1
INLET AND OUTLET CONNECTIONS
•
All water connections must meet
American National
Standard Pipe Threads (NPT).
•
For ease of service, install unions on inlet and outlet of
the appliance. The connection to the appliance marked
“Inlet” on the header should be used for return from the
system. The connection on the header marked “Outlet”
is to be connected to the supply side of the system.
4.2
MINIMUM PIPE SIZE REQUIREMENTS
Minimum water pipe connections are as follows for TH
single unit installations. The equivalent number of straight
feet of pipe for each valve and fitting in the connecting
piping must be considered to properly arrive at the total
equivalent feet of straight pipe in the field installed piping to
the appliance. Consult factory if longer piping distances are
required for a specific application. It is recommended to use
copper piping for all system piping to reduce the possibility
of the formation of deposits, which may result in heat
exchanger starvation.
System pipe size must be in accordance with Table 9
(depending on model). Connection sizes at the heater are
given in Table 4.
Table 9: Minimal System Pipe Size
Input,
Water Size,
NPT
Btu/Hr
[in.]
80,000
1
100,000
1
150,000
1
199,000
1
250,000
1 1/4
299,000
1 1/4
399,000
1 1/2
500,000
1 1/2
4.3
HEAT EXCHANGER
This appliance uses precision formed stainless steel tubing to
maximize the heat transfer process and achieve 97% steady-
state efficiency. This heat exchanger is designed to withstand
160 PSIG working pressure.
A factory installed circulating pump ensures proper water flow
during burner operation and creates enough velocity inside
the stainless steel tubes and headers that prevents scaling.
4.4
LOW WATER TEMPERATURE SYSTEMS
In combination applications where the heating system
requires supply water temperatures below 110°F, connections
may be made directly to the TH (Refer to Figure 35). At
incoming temperatures of 80
o
F or lower the TH achieves
maximum efficiency. Inlet temperatures must not drop below
40
o
F to prevent freezing.
4.5
PIPING ARRANGEMENTS
4.5.1
Field Supplied Components
1) Heater system piping
Boiler system piping MUST be sized according to
Table 9. Reducing the pipe size can restrict the flow
rate through the tank and cause an excessive
pressure drop.
2) Isolation Valves
Use only full port ball valves. Failure to supply full
port ball valves may result in reduced flow rate
through the tank.
3) Anti-Scald Mixing Valve
An anti-scaled mixing valve is recommended when
DHW storage is above 120
o
F.
4) Unions
Recommended for ease of serviceability.
5) System Temperature Sensor
A system temperature sensor is to be installed in the
main header at a point to detect controlled
temperature and where it will not lead to short-
cycling of the boiler.