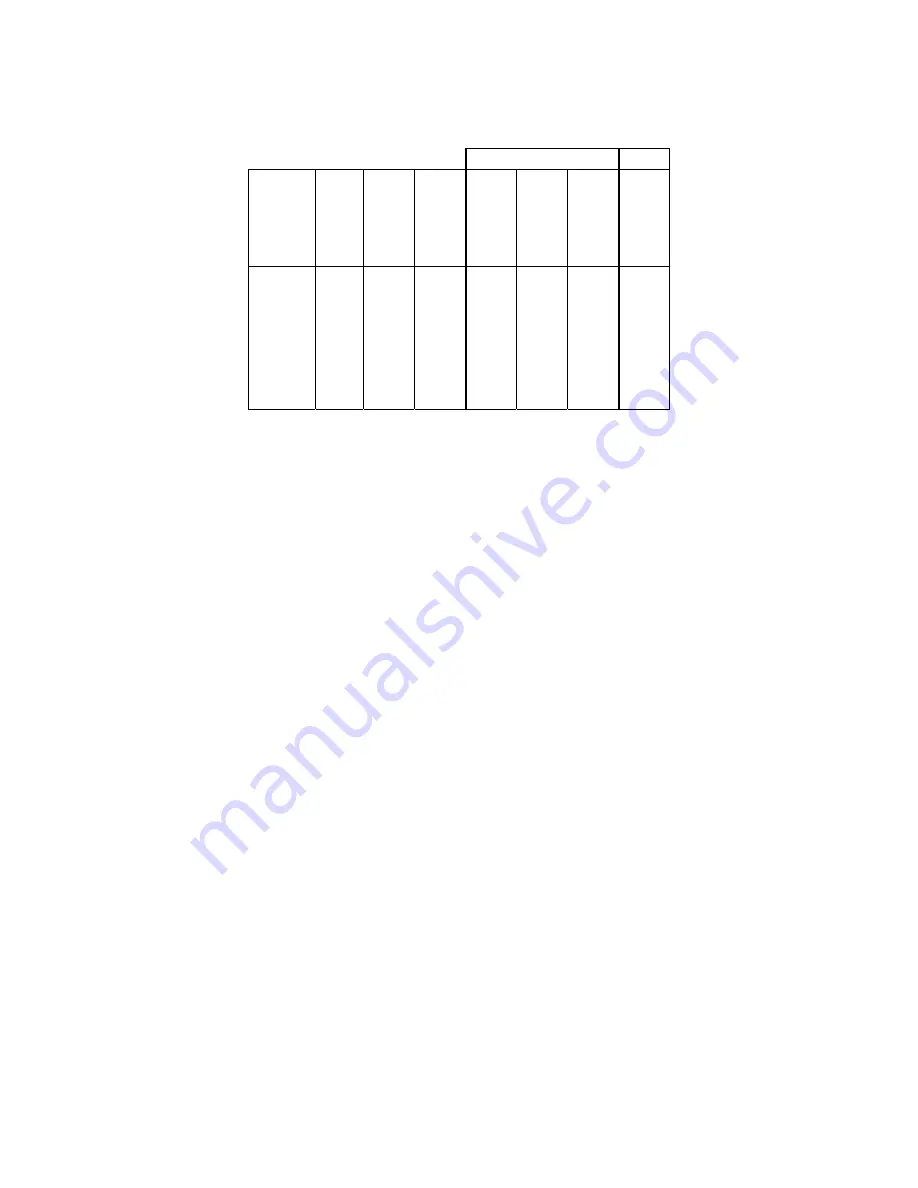
3
B' Dia. Venting
E' Dia.
Model W'
Wa
ter
Conn
ection
Gas
Conn
ection
Outdo
o
r
Cond
ensing
or Sidewall
Standa
rd
Air Inlet
MF800 45 3/4 2 1/2
1
8
8
10
8
MF1000 52 3/4 2 1/2 1 1/4
8
8
10
8
MF1200
62
2 1/2 1 1/4
10
10
12
10
MF1400 71 1/4 2 1/2 1 1/4
10
10
12
10
MF1600 80 3/4 2 1/2 1 1/2
12
12
14
12
MF1800 89 3/4 2 1/2 1 1/2
12
12
14
12
MF2000
99
2 1/2 1 1/2
12
12
14
12
Table 1
3. PROVIDE AIR FOR COMBUSTION AND VENTILATION
Provisions for combustion and ventilation air must be in accordance with:
•
Section 5.3. Air for combustion and Ventilation, of the National Fuel Gas Code, ANSI
Z223.1, or;
•
Sections 7.2, 7.3 or 7.4 of CAN/CGA B149 Installation Codes, and;
•
Applicable provisions of the local building codes.
The operation of exhaust fans, compressors, air handling units etc. can rob air from the room,
creating a negative pressure condition leading to reversal of the natural draft action of the
venting system. Under these circumstances an engineered air supply is necessary.
If the heater is to be installed near a corrosive or potentially corrosive air supply, the heater
must be isolated from it and outside air should be supplied as per code.
Potentially corrosive atmospheres will result from exposure to permanent wave solution,
chlorinated waxes and cleaners, chlorine, water softening chemicals, carbon tetrachloride,
halogen based refrigerants, Freon cleaning solvents, hydrochloric acid, cements and glues,
masonry washing materials, antistatic fabric softeners, dry cleaning solvents, degreasing liquids,
printing inks, paint removers, etc.
4. ELECTRICAL WIRING
All electrical wiring to the boiler must be electrically bonded to ground in accordance with the
requirements of the authority having jurisdiction or, in the absence of such requirements, with
the National Electrical Code, ANSI/NFPA 70 or the Canadian Electrical Code Part I, CSA C22.1,
Electrical Code.
Summary of Contents for MICOFLAME 2 Series
Page 24: ...22...
Page 25: ...23...
Page 26: ...24 22 EXPLODED VIEW...