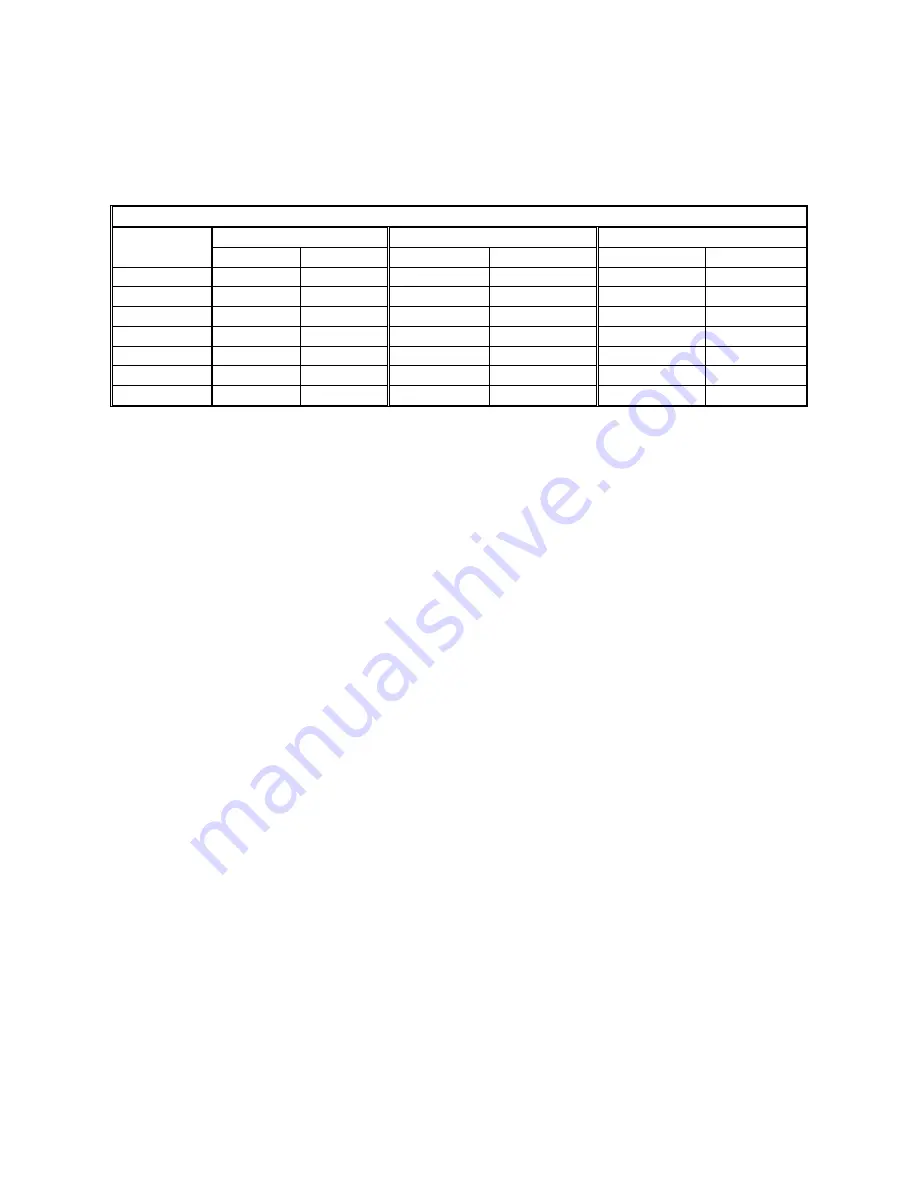
6
Before operating the boiler, the complete gas train and all connections must be tested using
soap solution.
DISTANCE FROM NATURAL GAS METER OR PROPANE SECOND STAGE REGULATOR
0-100 FT
100-200 FT.
200-300 FT.
Input
Btu/Hr
NAT.
L.P.
NAT. L.P. NAT. L.P.
800,000
2”
1 ½“
2 ½“
2“
2 ½“
2“
1,000,000
2”
1 ½“
2 ½“
2“
2 ½“
2“
1,200,000
2 ½“
2“
2 ½“
2“
3”
2 ½“
1,400,000
2 ½“
2“
2 ½“
2“
3”
2 ½“
1,600,000
2 ½“
2“
3”
2 ½“
3”
2 ½“
1,800,000
2 ½“
2“
3”
2 ½“
3”
2 ½“
2,000,000
2 ½“
2”
3”
2 ½“
3”
2 ½“
Table 2
7. VENTING
Boilers for outdoor installation are intended to vent using a listed vent cap.
For indoor installations venting must be in accordance with Part 7, Venting of Equipment, of the
National Fuel Gas Code, ANSI Z223.1, or Section 7, Venting of Equipment and Air Supply for
Appliances, of the CAN/CGA B149, Installation Codes, and applicable provisions of the local
building codes.
Vent connectors serving appliances vented by natural draft shall not be connected into any
portion of mechanical draft systems operating under positive pressure.
Horizontal runs of vent pipe shall be securely supported (approximately every 4 feet) to prevent
sagging and maintain a minimum upward slope of
¼
” per foot from the boiler to the vent
terminal.
When an existing boiler is removed from a common venting system, the common venting
system is likely to be too large for proper venting of the appliances remaining connected to it .At
the time of removal of an existing boiler, the following steps must be followed with each
appliance remaining connected to the common venting system placed in operation, while the
other appliances remaining connected to the common venting system are not in operation.
a) Seal any unused openings in the common venting system.
b) Visually inspect the venting system for proper size and horizontal pitch and determine
that there is no blockage, restriction, leakage, corrosion or other deficiency, which could
cause an unsafe condition.
c) Insofar as is practical, close all building doors and windows and all doors between the
space in which the appliances remaining connected to the common venting system are
located and other spaces of the building. Turn on the clothes dryers and any appliances
not connected to the common venting system. Turn on any exhaust fans, such as range
Summary of Contents for MICOFLAME 2 Series
Page 24: ...22...
Page 25: ...23...
Page 26: ...24 22 EXPLODED VIEW...