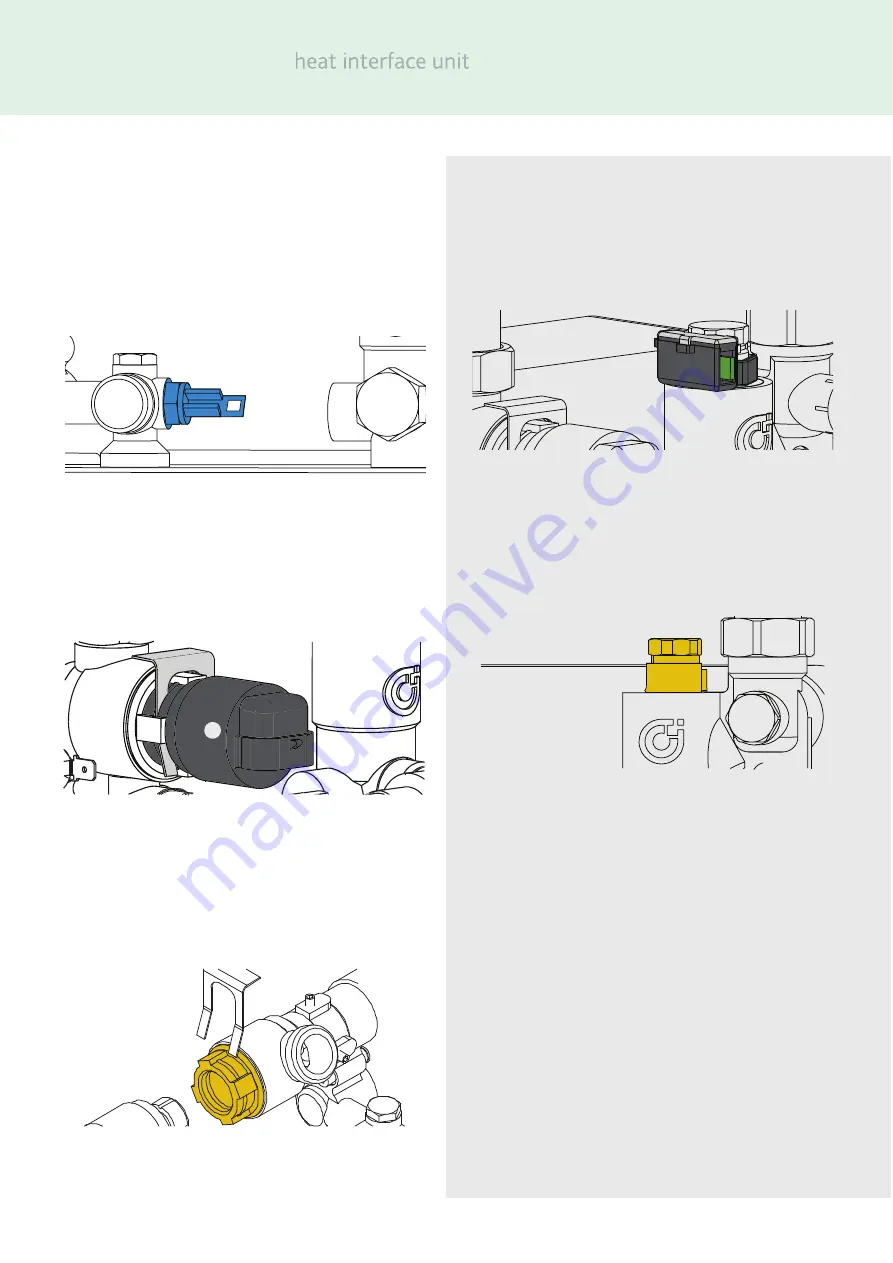
SATK20 & SATK30
16
Replacing the valve obturator
•
Disconnect the valve actuator (see previous paragraph).
•
Extract the obturator, unscrewing the locking nut (F).
•
Replace the obturator and screw on the locking nut (F),
then insert the actuator.
•
Insert the fixing clip, respecting the correct direction
•
Reconnect the connector.
Replacing the valve actuator
•
Disconnect the actuator cable, lightly pressing the tab on
the connector and extracting it (see page 17).
•
Extract the fixing clip (D) and then the actuator.
•
Position the new actuator (E).
•
Insert the fixing clip, respecting the correct direction.
•
Reconnect the connector.
Maintenance
Temperature probe replacement
•
Disconnect the probe cable, lightly folding the tab (C) and
extracting the connector (see page 17)
•
Unscrew the probe
•
Fit the new probe
•
Reconnect the connector respecting the only possible way
it can be inserted.
When carrying out maintenance on the electrical system, for
the connections follow the diagram on page 16.
After concluding maintenance, refill the system and check the
operations described in the chapter “Commissioning” and
re-fit the cover.
For information regarding spare parts or other technical
information, please contact Altecnic.
Only genuine Altecnic re-placement components should be
used.
Replacing or cleaning the DHW priority flow meter turbine
Extract the flow sensor
•
Unscrew and remove the cartridge (H)
•
Remove any impurities present or change the cartridge if
necessary
•
Screw in the cartridge
•
Reposition the flow sensor.
Replacing the DHW priority flow meter
•
Disconnect the flow meter cable by means of the
connector (see page 17).
•
Extract the flow sensor (G).
•
Position the new sensor.
•
Reconnect the connector respecting the only possible way
it can be inserted.
C
G
F
D
E
H