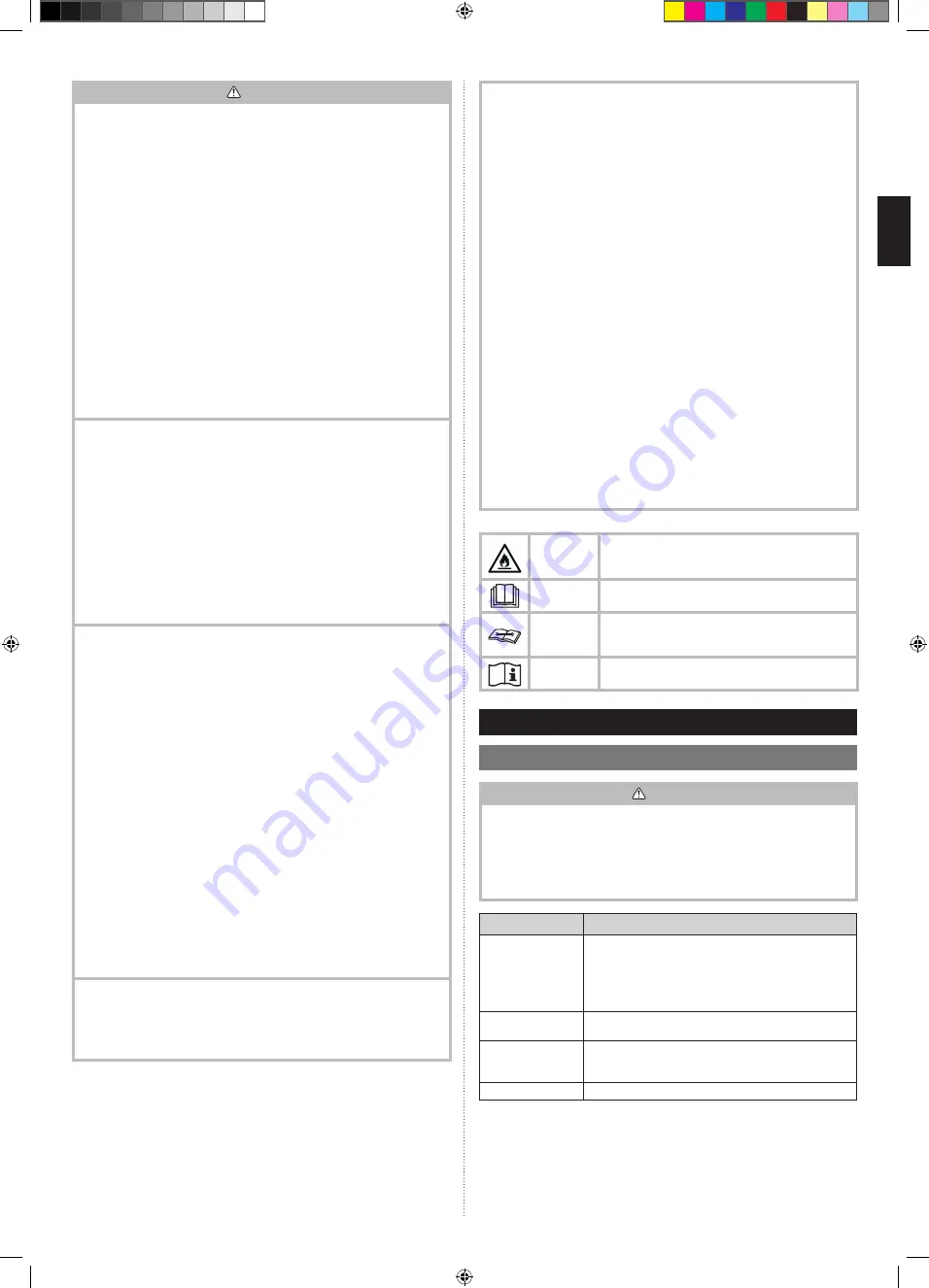
En-3
CAUTION
8. Removal and evacuation
• When breaking into the refrigerant circuit to make repairs – or for any other
purpose –conventional procedures shall be used.
However, it is important that best practice is followed since
fl
ammability is a
consideration.
The following procedure shall be adhered to:
• remove refrigerant
• purge the circuit with inert gas
• evacuate
• purge again with inert gas
• open the circuit by cutting or brazing
• The refrigerant charge shall be recovered into the correct recovery cylinders.
• The system shall be “
fl
ushed” with OFN to render the unit safe.
• This process may need to be repeated several times.
• Compressed air or oxygen shall not be used for this task.
• Flushing shall be achieved by breaking the vacuum in the system with OFN and
continuing to
fi
ll until the working pressure is achieved, then venting to atmosphere,
and
fi
nally pulling down to a vacuum.
• This process shall be repeated until no refrigerant is within the system.
• When the
fi
nal OFN charge is used, the system shall be vented down to atmo-
spheric pressure to enable work to take place.
• This operation is absolutely vital if brazing operations on the pipe work are to take
place.
• Ensure that the outlet for the vacuum pump is not close to any ignition sources and
there is ventilation available.
9. Charging procedures
• In addition to conventional charging procedures, the following requirements shall
be followed.
- Ensure that contamination of different refrigerants does not occur when using
charging equipment.
- Hoses or lines shall be as short as possible to minimize the amount of refriger-
ant contained in them.
- Cylinders shall be kept upright.
- Ensure that the refrigeration system is earthed prior to charging the system with
refrigerant.
- Label the system when charging is complete (if not already).
- Extreme care shall be taken not to over
fi
ll the refrigeration system.
• Prior to recharging the system it shall be pressure tested with OFN.
• The system shall be leak tested on completion of charging but prior to commis-
sioning.
• A follow up leak test shall be carried out prior to leaving the site.
10. Decommissioning
• Before carrying out this procedure, it is essential that the technician is completely
familiar with the equipment and all its details.
• It is recommended good practice that all refrigerants are recovered safely.
• Prior to the task being carried out, an oil and refrigerant sample shall be taken in
case analysis is required prior to re-use of reclaimed refrigerant.
• It is essential that electrical power is available before the task is commenced.
a) Become familiar with the equipment and its operation.
b) Isolate system electrically.
c) Before attempting the procedure ensure that:
• mechanical handling equipment is available, if required, for handling refrig-
erant cylinders;
• all personal protective equipment is available and being used correctly;
• the recovery process is supervised at all times by a competent person;
• recovery equipment and cylinders conform to the appropriate standards.
d) Pump down refrigerant system, if possible.
e) If a vacuum is not possible, make a manifold so that refrigerant can be re-
moved from various parts of the system.
f) Make sure that cylinder is situated on the scales before recovery takes place.
g) Start the recovery machine and operate in accordance with manufacturer’s
instructions.
h) Do not over
fi
ll cylinders. (No more than 80 % volume liquid charge).
i) Do not exceed the maximum working pressure of the cylinder, even temporarily.
j) When the cylinders have been
fi
lled correctly and the process completed, make
sure that the cylinders and the equipment are removed from site promptly and
all isolation valves on the equipment are closed off.
k) Recovered refrigerant shall not be charged into another refrigeration system
unless it has been cleaned and checked.
11. Labelling
• Equipment shall be labelled stating that it has been de-commissioned and emptied
of refrigerant.
• The label shall be dated and signed.
• Ensure that there are labels on the equipment stating the equipment contains
fl
am-
mable refrigerant.
12. Recovery
• When removing refrigerant from a system, either for servicing or decommissioning,
it is recommended good practice that all refrigerants are removed safely.
• When transferring refrigerant into cylinders, ensure that only appropriate refrigerant
recovery cylinders are employed.
• Ensure that the correct number of cylinders for holding the total system charge are
available.
• All cylinders to be used are designated for the recovered refrigerant and labelled
for that refrigerant (i.e. special cylinders for the recovery of refrigerant).
• Cylinders shall be complete with pressure relief valve and associated shut-off
valves in good working order.
• Empty recovery cylinders are evacuated and, if possible, cooled before recovery
occurs.
• The recovery equipment shall be in good working order with a set of instructions
concerning the equipment that is at hand and shall be suitable for the recovery of
fl
ammable refrigerants.
• In addition, a set of calibrated weighing scales shall be available and in good work-
ing order.
• Hoses shall be complete with leak-free disconnect couplings and in good condition.
• Before using the recovery machine, check that it is in satisfactory working order,
has been properly maintained and that any associated electrical components are
sealed to prevent ignition in the event of a refrigerant release.
Consult manufacturer if in doubt.
• The recovered refrigerant shall be returned to the refrigerant supplier in the correct
recovery cylinder, and the relevant Waste Transfer Note arranged.
• Do not mix refrigerants in recovery units and especially not in cylinders.
• If compressors or compressor oils are to be removed, ensure that they have been
evacuated to an acceptable level to make certain that
fl
ammable refrigerant does
not remain within the lubricant.
• The evacuation process shall be carried out prior to returning the compressor to
the suppliers.
• Only electric heating to the compressor body shall be employed to accelerate this
process.
• When oil is drained from a system, it shall be carried out safely.
Explanation of symbols displayed on the indoor unit or outdoor unit.
WARNING
This symbol shows that this equipment uses a
fl
ammable
refrigerant. If the refrigerant is leaked, together with an
external ignition source, there is a possibility of ignition.
CAUTION
This symbol shows that the Operation Manual should be
read carefully.
CAUTION
This symbol shows that a service personnel should be
handling this equipment with reference to the Installation
Manual.
CAUTION
This symbol shows that there is information included in the
Operation Manual and/or Installation Manual.
2. PRODUCT SPECIFICATION
2.1. Installation tools
WARNING
• To install a unit that uses R32 refrigerant, use dedicated tools and piping materials that
have been manufactured speci
fi
cally for R32(R410A) use. Because the pressure of
R32 refrigerant is approximately 1.6 times higher than R22, failure to use dedicated
piping material or improper installation can cause rupture or injury. Furthermore, it can
cause serious accidents such as water leakage, electric shock, or
fi
re.
• Do not use a vacuum pump or refrigerant recovery tools with a series motor, since it
may ignite.
Tool name
Contents of change
Gauge manifold
Pressure is high and cannot be measured with a conventional
(R22) gauge. To prevent erroneous mixing of other refriger-
ants, the diameter of each port has been changed.
It is recommended the gauge with seals -0.1 to 5.3 MPa
(-1 to 53 bar) for high pressure. -0.1 to 3.8 MPa (-1 to 38 bar)
for low pressure.
Charge hose
To increase pressure resistance, the hose material and base
size were changed. (R32/R410A)
Vacuum pump
A conventional vacuum pump can be used by installing a
vacuum pump adapter.
(Use of a vacuum pump with a series motor is prohibited.)
Gas leakage detector
Special gas leakage detector for HFC refrigerant R32/R410A.
Copper pipes
It is necessary to use seamless copper pipes and it is desirable that the amount of residual
oil is less than 40 mg/10 m. Do not use copper pipes having a collapsed, deformed or
discolored portion (especially on the interior surface). Otherwise, the expansion valve or
capillary tube may become blocked with contaminants.
As an air conditioner using R32(R410A) incurs pressure higher than when using conven-
tional refrigerant, it is necessary to choose adequate materials.
9379069953_IM.indb 3
9379069953_IM.indb 3
5/24/2019 9:59:18 AM
5/24/2019 9:59:18 AM