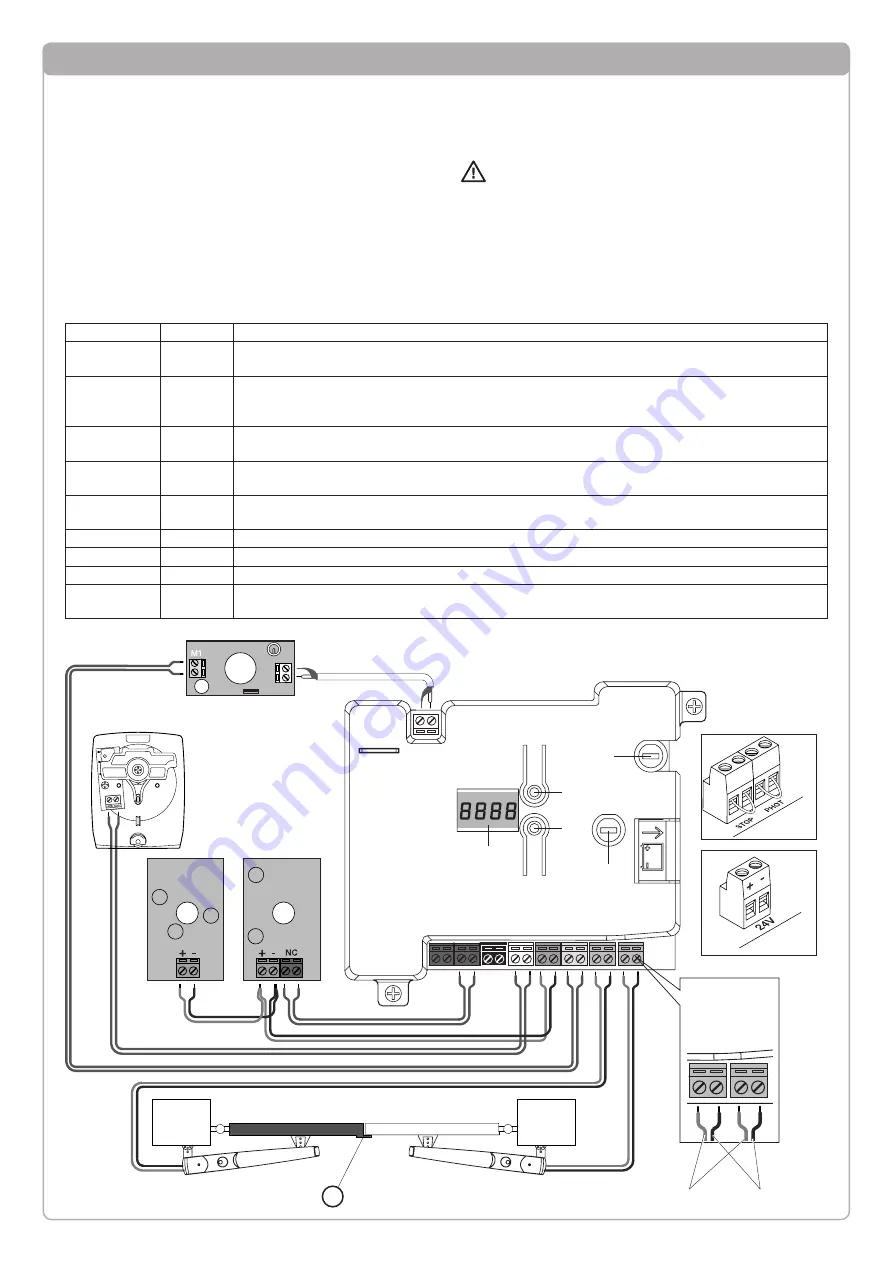
16
Control unit CP.BTY connections
Fig.24
3
5
2
SHHIELD
ANT
P.BY
K.BY
RX
PHOT
PHOT C
STOP
PP
24V
-
+
4
1
BLINK
MOT1
MOT2
ANT
SHIELD
F.BY
TX
DESCRIPTION OF THE TERMINAL BOARDS
CLAMP
COLOUR DESCRIPTION
PHOT
GREEN
NC contact input from the RX photocell installed on the pillar. The two clamps are connected to
each other by a wire (ref. “A”). Remove this wire only if the photocell is connected.
PHOT C
GREEN
NC contact input from the RX photocell installed inside the small column (optional).
The two clamps are connected to each other by a wire (ref. “A”). Remove this wire only if the
photocell is connected.
STOP
BLACK
STOP input NC contact for auxiliary “STOP” command (optional). The two clamps are connected
to each other by a wire (ref. “A”). Remove this wire only if a device is connected to this input.
PP
WHITE
Step-by Step’ command input from the key selector. At every impulse sent from the selector a
sequence of commands, which can be configured using the PP function, is performed cyclically.
24V
YELLOW
24V output for photocells power supply. Respect the pola and - in the connections (ref
“B”).
BLINK
RED
24 Vdc flashing light connection output
MOT1
ORANGE
Motor 1 connection output respect red and blue (ref. “C”)
MOT2
ORANGE
Motor 2 connection output respect red and blue (ref. “C”)
SHIELD/ANT
BLUE
Connection of the aerial built-in the flashing light.
When connecting the RG58 cable, the external shield must be connected to the SHIELD clamp.
3
5
2
SHHIELD
ANT
P.BY
K.BY
RX
PHOT
PHOT C
STOP
PP
24V
-
+
4
1
BLINK
MOT1
MOT2
ANT
SHIELD
F.BY
TX
BLUE
RED
P
A
B
M1
M2
C
Except for the mains connection cable, all electric connections
have a voltage of 24V and can also be performed by unquali-
fied staff.
KEY:
1 Line protection fuse
2 Accessories protection fuse
3 “PGM” programming button
4 Programming button “
5
”
5 LCD
Connect all accessories making reference to the layout in figure
24 and to the “Electric connections” paragraph, for that con-
cerning the types of cable.
To make connection easier, the accessory clamps have colours
that correspond to those of the control unit.
If the leaves have a profile similar to that highlighted in
detail P in figure 24, consider that the opening movement
always starts with motor 1, while the closure movement
always starts with motor 2. The time that passes in
between can be regulated using the parameter TDMC
(see “Regulation of the phase shift time between the
leaves”).
Summary of Contents for BEAUTY
Page 27: ......