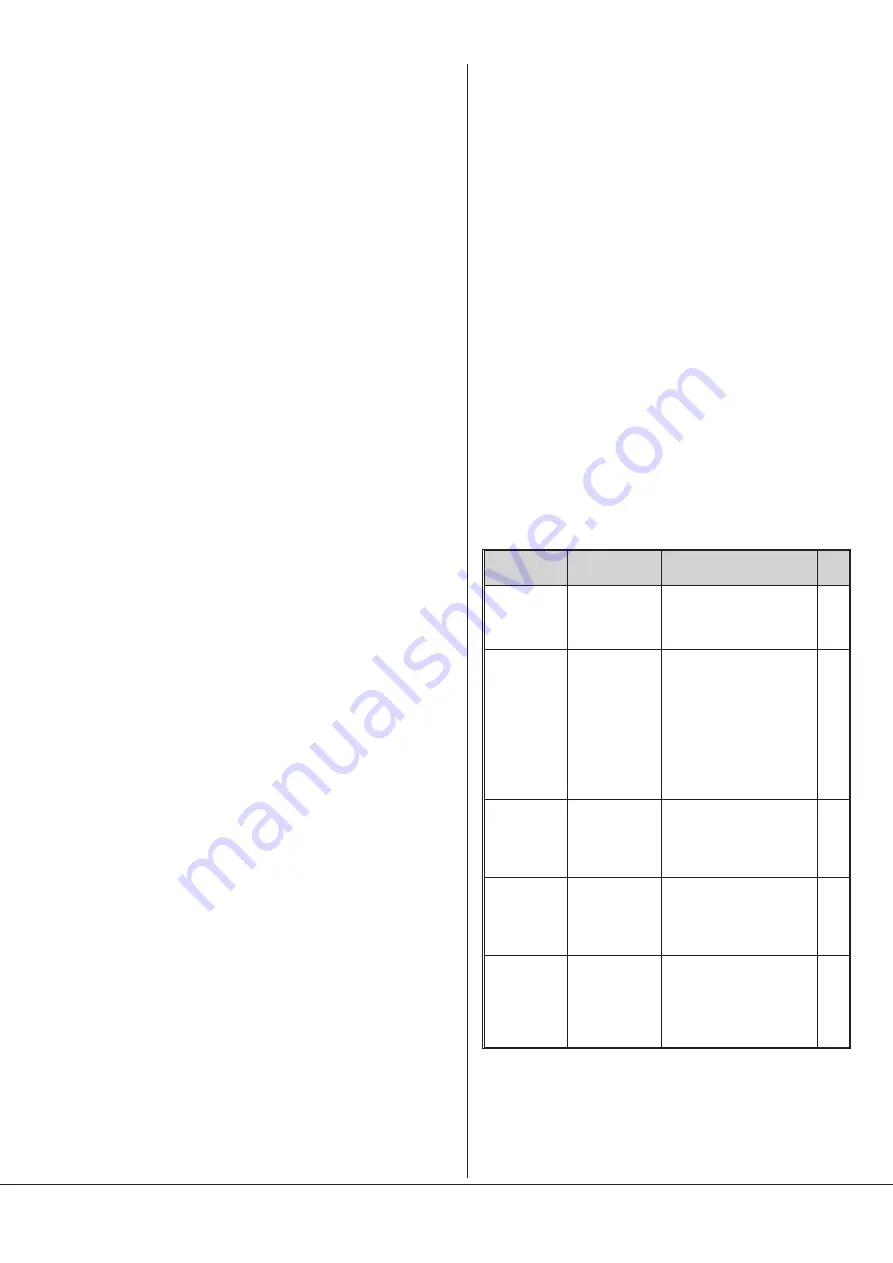
sures are no greater than 30 volts rms, 42.4 volts peak, 60 volts dc or
240 volt-amp in dry locations.
Type 4
Equipment is energized. Energized circuits are exposed and inadvertent
contact with uninsulated energized parts is possible. Potential expo-
sures are greater than 30 volts rms, 42.4 volts peak, 60 volts dc,
or 240 volt-amp in dry locations. Potential exposures to radio-
frequency currents, whether induced or via contact, exceed the limits in
Table A5-1 of Appendix 5 (SEMI S2 guideline).
Lock Out/ Tag Out procedure (Type 1 of
electrical work)
l
Stop the pump with the remote control (press on STOP button
during 10s)
l
Press on emergency stop button
l
Switch off the main disconnect switch
l
Switch off the customer’s power supply
l
Switch off the water (inlet first, then outlet) and nitrogen quick
connections
l
Put the label or warning board “Maintenance processing” on or
next to the pump
Safety Lockout procedure
l
Take off the label or warning board “Maintenance processing”
l
Check the cooling liquid and oil levels according to the chapters
“Checking the oil level” and “Checking the cooling liquid level”
l
Open the power box cover and check that the FDP1 thermal relay
is on manual reset position
l
Close the cover
l
Switch on the main disconnect switch
l
Release the emergency stop button
l
Switch on the water (outlet first, then inlet) and nitrogen quick
connections
Start the pump with the remote control (press on START button)
Emergency off circuit description
l
The Emergency off circuit may be opened by pressing on emer-
gency stop button, by opening the overload relay (s) FDP1, FDP2,
FDP3, FDP4 or the temperature switch TS 6. If one of the elements
fails, then the vacuum system will immediately stop. The PLC will
remain energized to save the pump status.
l
If the emergency stop button was pressed, check the start up of
the pump then release this button to restart the pump. Press on
Silence button for Reset, then Start button on the remote control,
the pump will restart.
l
If the FDP1or FDP2, FDP3, FDP4 thermal protection is on, press on
emergency stop button, switch off and padlock the main discon-
nect switch, switch off the customer’s power supply (type 1 of
electrical work). Open the power box cover and check the value on
the FDP1 or FDP2, FDP3, FDP4 thermal relay(s) according to the
settings indicated in the electrical schematics.
l
If ok, check the wiring system from the terminal box motor to the
KDP1 contactor. If ok, call the BUSCH Semicon service team in
charge of the maintenance of the pumps.
l
Before restarting the vacuum system, reactivate the FDP1 thermal
relay by pressing on Reset. If this does not work, wait 60 seconds
and start the operation again. Close the cover again. Switch on the
main disconnect switch, then release the emergency stop button.
Restart the vacuum system by pressing on Start button on the re-
mote control. If the vacuum system does not start, press on emer-
gency stop button, switch off and padlock the main disconnect
switch, switch off the customer’s power supply and put the label
“maintenance processing”. Call the BUSCH Semicon service team
in charge of the maintenance of the pumps.
l
If the external thermal protection B11 is engaged, check that the
water flow shows 29 l/min on the flowmeter. If not, set the water
flow at 29 l/min according to the instruction (see chapter
“Checking the cooling liquid flow”). Check the wiring system of
the thermal protection by opening the side face (Type 3 of electri-
cal work). Wait a few minutes for the cooling of the protection,
then press on Start button to restart the vacuum system.
Safety interlock description
See “Interlock table”.
Lock out/ Tag out for hydraulics and pneumatics
u
Hydraulics: cooling water
u
Pneumatics: nitrogen
Lock Out/ Tag Out procedure (Type 1 of
electrical work)
l
Stop the pump with the remote control (press on STOP button
during 10s)
l
Press on emergency stop button
l
Switch off the main disconnect switch
l
Switch off the customer’s power supply
l
Switch off the water (inlet first, then outlet) and nitrogen quick
connections
l
Put the label or warning board “Maintenance processing” on or
next to the pump
The end user is responsible for providing energy isolation capabilities
on the water and nitrogen
Interlock table
Interlock event Sensor
Response
Cooling liquid
overtempera-
ture
Themperature
switch TS 2
Contactors open and remove
power to motors
S
DP, MB
motors
overcurrent
Thermal over-
load relays
EOCR (MB)
Thermal over-
load relays
EOCR
(DP 1, 2 & 3)
Contactors open and remove
power to motors.
For DP, the security circuit is
shut down then reload the
thermal relay.
For MB, the MB circuit is
shut down then reload the
thermal relay.
S
DP Motor
overtempera-
ture (t° >
150°C)
Themperature
switch TS 6
Contactors open and remove
power to motors.
EMO: security circuit
S
MB Motor
overtempera-
ture (t° >
150°C)
Themperature
switch TS 7
MB vacuum pump stops
S
Exhaust
overpressure
(option)
Overpressure
sensor TS 5
Depends on alarm function
set in the PLC for
overpressure Set at factory:
None ie. the pump continues
running with alarm
S
COBRA DS 8163 A
Safety
0870772605
Page 13
Summary of Contents for COBRA DS 8163 A
Page 34: ......