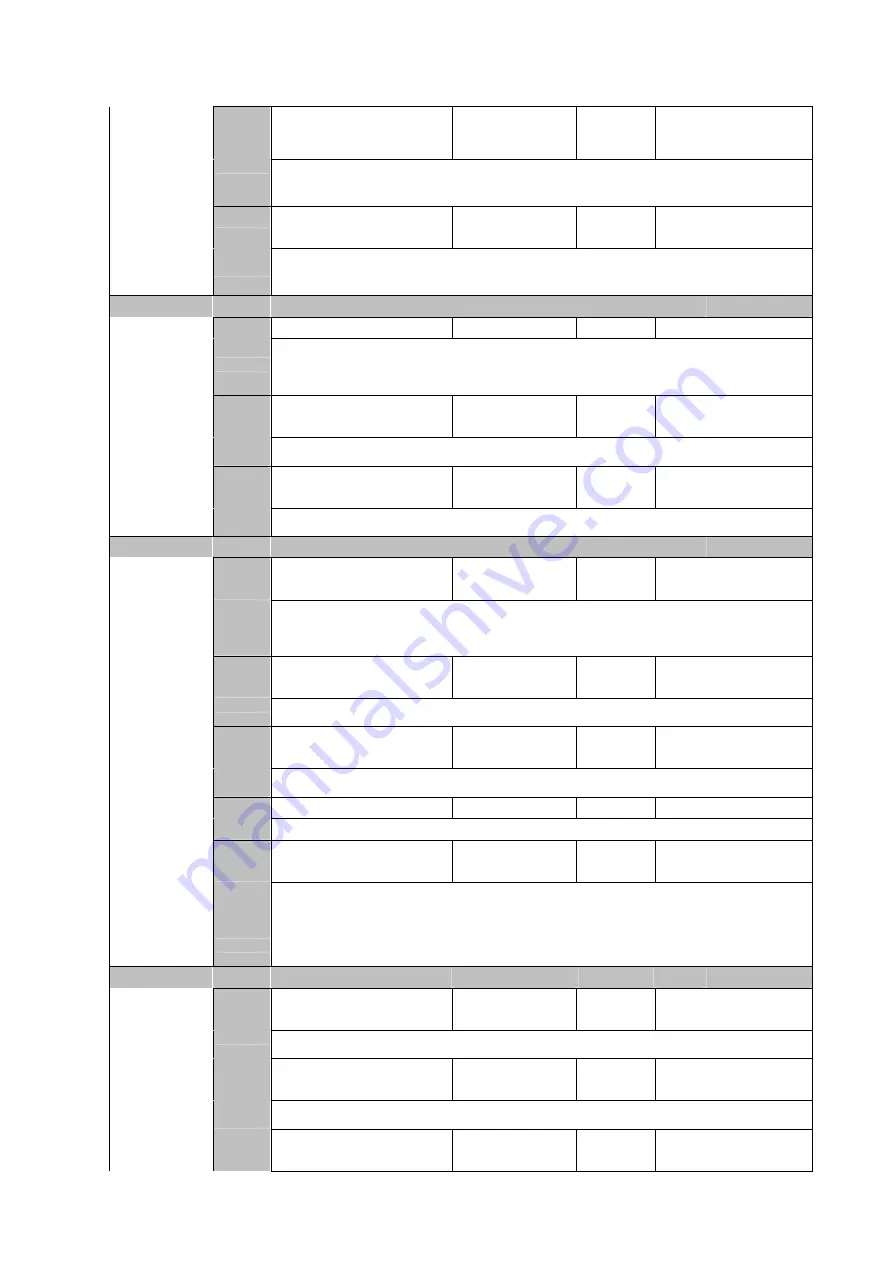
Page 69 of 82
Date: 27.01.06
6
Input B function:
Inhibit evaluation,
freeze current evaluation result
U8
rw
1
Valid values:
Function not
supported
0
Function supported
1
7
Input B function:
Reset mean value
U8
rw
1
Valid values:
Function not
supported
0
Function supported
1
7
Evaluation results
1
evaluation result
U8
ro
1
Valid values:
OK
0
NOK: too high
1
NOK: too low
2
2
Contents of minimum
value buffer
REAL32
ro
4
Valid values:
Contents of min value
buffer
3
Contents of maximum
value buffer
REAL32
ro
4
Valid values:
Contents of max value
buffer
8
Sensor test
1
Measure sensor test
reference value
U8
wo
1
EVENT!
Valid values:
Adopt current
measured value as
new sensor test
reference value
write any byte
2
Sensor test
reference value
REAL32
rw
4
Valid values:
New sensor test
reference value
3
Sensor test
tolerance value
REAL32
rw
4
Valid values:
New sensor test
tolerance value
4
Perform sensor test
U8
wo
1
EVENT!
Valid values:
write any byte
5
Read result from last
sensor test
U8
ro
1
Valid values:
OK
0
NOK: too high
1
NOK: too low
2
Test not performed
yet
3
9
Reset functions
1
Reset evaluation
result
U8
wo
1
EVENT!
Valid values:
Clear current
evaluation result
write any byte
2
Reset minimum value
buffer
U8
wo
1
EVENT!
Valid values:
Delete contents of min
value buffer
write any byte
3
Reset maximum
value buffer
U8
wo
1
EVENT!