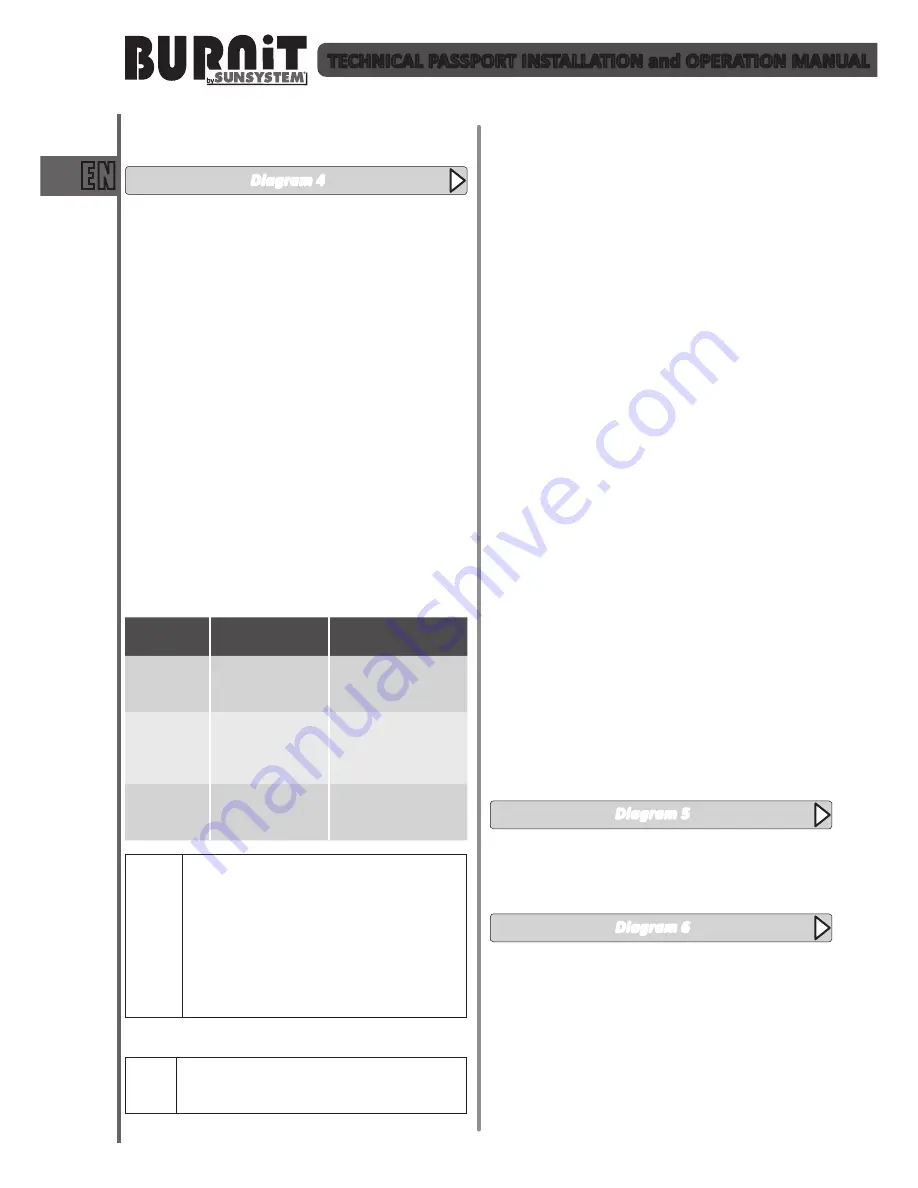
6
EN
TECHNICAL PASSPORT INSTALLATION and OPERATION MANUAL
7. INSTALLATION OF THE HEATING BOILER
7.1. Connecting the boiler to a chimney
Diagram 4
Boiler-to-chimney connection must always comply
with the existing standards and rules. The chimney
must provide sufficient draught for evacuation of the
smoke under any conditions.
The proper functioning of the chimney requires
adequate sizing of the chimney itself since the
draught it produces affects combustion, boiler’s
output and life span.
The draught created by the chimney is in functional
relation to its cross-section, height and the roughness
of its interior walls. No other appliance may be
connected to the chimney serving the boiler. Chimney
diameter must not be smaller than the flue outlet
of the boiler. Flue outlet must be connected to the
chimney opening. In terms of mechanical properties,
the flue outlet must be sturdy and properly sealed (to
avoid gas leak) and allow for easy access for cleaning
on the inside. The inner section of the flue outlet
must not be greater than the effective section of the
chimney and must not narrow. Avoid using elbow
joints.
Table 3
Recommended minimum chimney heights
Boiler
output
Chimney
diameter
Recommended
height
18 kW
Ø 160 mm
Ø 180 mm
Ø 200 mm
At least 8 m
At least 8 m
At least 7 m
25 kW
Ø 160 mm
Ø 180 mm
Ø 200 mm
Ø 220mm
At least 9 m
At least 9 m
At least 8 m
At least 8 m
40 kW
Ø 180 mm
Ø 200 mm
Ø 220mm
At least 11 m
At least 10 m
At least 10 m
i
Data in the tables are for indicative
purposes.
Draught depends on the diameter, height,
uneven sections along the chimney
surface and differences in temperature of
combustion products and outside air. We
recommend that you use chimney fitted
with flue terminal. Heating specialist must
calculate the precise sizing of the chimney.
7.2. Connecting the safety heat exchanger
*
Such connection must be performed by a
technician / service shop authorized for
such operations.
The heating boiler is equipped with safety heat
exchanger (cooling circuit). It connects to the water
system through a thermostatic valve. In case of
overheating, the thermostatic valve feeds in cold
water from the water mains which passes through
the heat exchanger and absorbs the heat in the boiler.
The water is then discharged into the sewage system.
This arrangement ensures safe evacuation of the
excess heat without the need for additional energy.
This guarantees that the water in the boiler will not
exceed the maximum safe level of
95°C
.
The minimum operating pressure of the cooling
water in the safety heat exchanger must be within
the range 2 - 10 bar.
A flow rate of at least 12 l/min is required. Connect
the safety heat exchanger according to the hydraulic
diagram using thermostatic valve. Install a filter on
the inlet before the thermostatic valve.
8. BOILER OPERATION
8.1. Loading and ignition of boiler
When lighting the boiler for the first time, a
condensate is formed which is later drained (this is
not a fault in the boiler).
When burning moist wood, the boiler stops
working effectively and fuel consumption increases
significantly, desired output is not achieved and the
operational life of the boiler body and the chimney
is shortened.
Fuel is loaded in the upper combustion chamber and
it is recommended is to load logs of length equal to
the combustion chamber length and stack them tight
inside with least possible air gaps.
Recommendations for fuel loading:
1.
Keep air openings (upper chamber) clean from ash.
Clogging of air openings may affect boiler operation.
Diagram 5
2. Stacking firewood in boiler chamber.
Wood in the chamber must be neatly arranged and
not thrown, as is illustrated. This is a top plan view of
the boiler chamber.
Diagram 6
An important condition for the smooth running of the
pyrolysis combustion is the upper chamber to be well
tight with fuel, i.e. with minimal air gaps between the
wood pieces.
When stacking the wood in the firebox keep clear
the opening between upper and lower chambers.
The entry of a large log in this opening can affect the
pyrolytic combustion