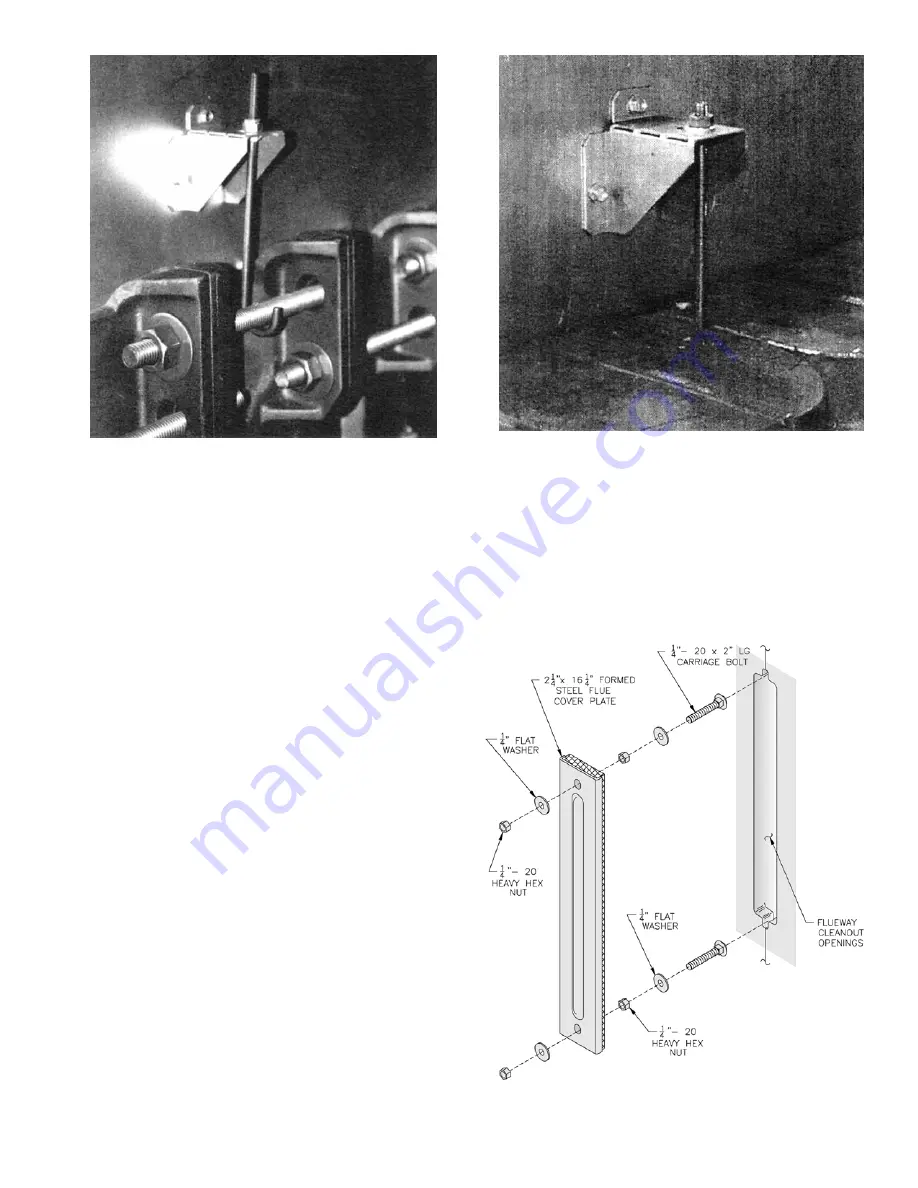
23
Figure 17: Left Side Canopy Intermediate Bracket
Figure 18: Right Side Canopy
Intermediate Bracket
on center section draw-up rod (hooks should
face outward). Secure canopy with 5/16” flat
washers, lock washers and brass nuts. See
Figure 17.
d. Secure canopy right side bracket(s) with ¼ - 20
x 5” lg. carriage bolts. Insert head of carriage
bolt between canopy body and casting. Slide
carriage bolt into slot provided between castings.
Lower carriage bolt until threaded end will pass
through hole in bracket. Secure canopy with ¼”
flat washers, lock washers and brass nuts. See
Figure 18.
13. Attach the 1/8” x 1” wide self-adhesive fiber gasket
to the surfaces of either the top flue outlet damper
assembly or top outlet canopy cover that mounts
against the canopy. Gasket must be centered over
all attachment holes. Do not overlap corners, cut
butt joints.
14. Secure either the top flue outlet damper assembly
or top outlet canopy cover with #10 x 1/2” sheet
metal screws.
B.
INSTALL FLUE COVER PLATES
over cleanout
openings on left side of boiler as shown in Figure 19.
See Important Product Safety Information on Page
21 of this manual, regarding refractory ceramic
fiber product warning.
1. Locate the cover plates, carriage bolts, nuts and
washers in the boiler assembly carton(s).
2. Remove insulation from two (2) 3/8” diameter holes
in flue cover plates using a 3/8” drill bit. Rotate bit
through insulation by hand.
3. Attach the carriage bolts to the top and bottom of the
flue openings with washers and hex nuts to provide
a fixed stud.
4. Install flue cover plates over studs with insulation
against boiler and secure with washers and nuts.
Tighten until insulation on cover plate provides a
tight seal to casting. If after tightening, a gap is still
evident where the sections join, apply silastic along
top and bottom edge of insulation board.
5. Repeat steps 3 through 6 for mounting remaining
flue cover plates.
Figure 19: Flue Cover Plate Attachment
Summary of Contents for operating and
Page 2: ...2 ...
Page 8: ...8 Section I General Information Figure 1 Dimensional Information ...
Page 21: ...21 Figure 16 Bare Boiler Assembly ...
Page 25: ...25 Figure 22 V9A Series Jacket Assembly Boiler Models V903A thru V912A ...
Page 31: ...31 Figure 26 V9A Series Minimum Piping Parallel Water Boiler ...
Page 32: ...32 Figure 27 V9A Series Minimum Piping Primary Secondary Water Boiler ...
Page 33: ...33 Figure 28 V9A Series Minimum Piping Details Bypass with Blend Pump Water Boiler ...
Page 34: ...34 Figure 29 V9A Series Minimum Piping Primary Secondary with Bypass Water Boiler ...
Page 37: ...37 Figure 32 Minimum Piping Requirements For Gravity Return V9A Series Steam Boilers ...
Page 42: ...42 Figure 37b DHW Generation with Tankless Coils Storage Tank and Destratification Pump ...
Page 43: ...43 Figure 37c DHW Generation with Indirect Water Heater ...
Page 58: ...58 Figure 40 Bare Boiler Assembly ...
Page 62: ...62 SERVICE RECORD DATE SERVICE PERFORMED ...
Page 63: ...63 SERVICE RECORD DATE SERVICE PERFORMED ...
Page 64: ...64 ...