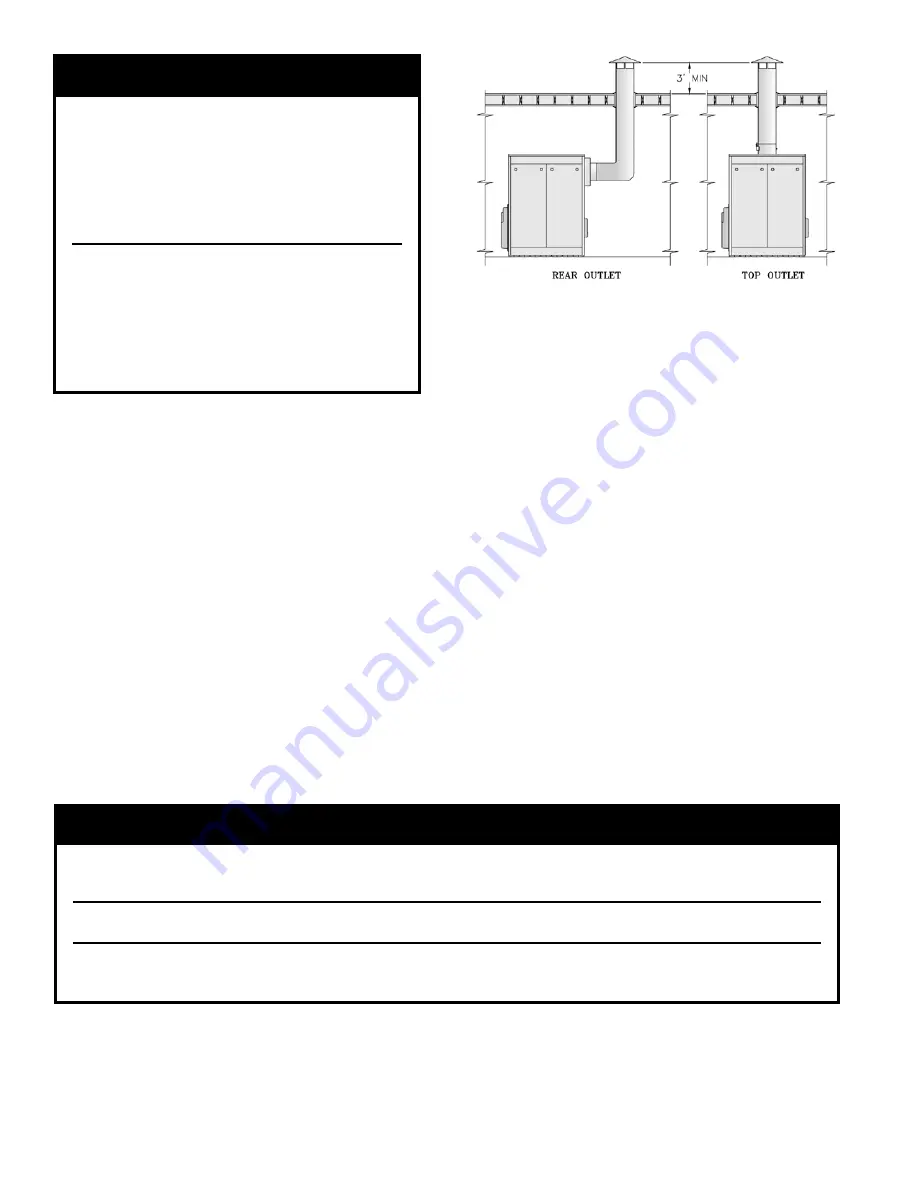
12
WARNING
When a V9A gas fired boiler is connected
to a venting system that is designed so that
it will operate under a positive pressure,
manufactured vent systems, designed and
approved for positive pressure application per
UL1738, must be used (for example, Van-Packer
model CS, Protech Model FasNSeal / FasNSeal
W2, Heatfab Saf-T-Vent or equivalent).
When a V9A oil fired or combination gas/oil
fired boiler is connected to a venting system
that is designed so that it will operate un-
der a positive pressure, manufactured vent
systems, designed and approved for posi-
tive pressure application, must be used (for
example, Selkirk Metalbestos Model PS / IPS,
Van-Packer Model ES or equivalent).
The V9A Series boiler is designed for forced draft
firing and may be used with a conventional natural draft
stack (15’ minimum height) or a stub vent, sometimes
called a diesel stack (see Figure 3a). See Table I for
the proper vent outlet size. For low silhouette vent
terminations, see Figure 3b. Draft controls are not
normally required, although they may be used on
installations where a natural draft stack is used or on
multiple boiler installations with a common stack. The
boiler is provided with a breeching damper, which
should be adjusted to maintain a positive pressure of
0.1” W.C. in the vent connector box during burner high
fire operation (see breeching pressure sensing port in
Figure 1).
If the venting system is designed for positive or forced
draft venting, the boiler, vent connector and stack will
operate under positive pressure. Gas tight vent systems
designed for pressure systems must be used to prevent
flue by-product leakage. The vent height is usually
limited to prevent negative draft, typically three (3)
feet above the roof line (see Figure 3a). The damper
shall be adjusted to maintain a positive pressure of
0.1” W.C. in the vent connector box during burner high
fire operation (see breeching pressure sensing port in
Figure 1).
If the venting system is designed for negative pressure
(natural draft), the boiler still operates with positive
pressure in the chamber and up to the fixed damper on
the flue collar. However, if the venting system is larger
than what is required, the stack will provide a surplus
draft (or negative pressure) that may require the use of
a barometric damper to maintain the positive 0.1” W.C.
pressure at the flue outlet. Multiple forced draft boiler
stacks should always be designed as negative to ensure
the products of combustion do not exit a boiler that is
not firing.
WARNING
Venting instructions are recommendations only. Consult a venting expert on the design of a specific
vent system for your application. The ASHRAE Venting Guide and The National Fuel Gas Code, NFPA
54 should be considered in all venting systems.
Conventional vent material may not be suitable for the application. Flue gases can leak carbon
monoxide from the joints on these materials and can result in severe personal injury or death.
Installations having long horizontal runs or an excessive amount of tees or elbows will restrict the flow
of combustion gases and can result in condensation, flue gas leakage of carbon monoxide, resulting in
severe personal injury or death.
Figure 3a: Typical Arrangement for Stub Vent
Summary of Contents for operating and
Page 2: ...2 ...
Page 8: ...8 Section I General Information Figure 1 Dimensional Information ...
Page 21: ...21 Figure 16 Bare Boiler Assembly ...
Page 25: ...25 Figure 22 V9A Series Jacket Assembly Boiler Models V903A thru V912A ...
Page 31: ...31 Figure 26 V9A Series Minimum Piping Parallel Water Boiler ...
Page 32: ...32 Figure 27 V9A Series Minimum Piping Primary Secondary Water Boiler ...
Page 33: ...33 Figure 28 V9A Series Minimum Piping Details Bypass with Blend Pump Water Boiler ...
Page 34: ...34 Figure 29 V9A Series Minimum Piping Primary Secondary with Bypass Water Boiler ...
Page 37: ...37 Figure 32 Minimum Piping Requirements For Gravity Return V9A Series Steam Boilers ...
Page 42: ...42 Figure 37b DHW Generation with Tankless Coils Storage Tank and Destratification Pump ...
Page 43: ...43 Figure 37c DHW Generation with Indirect Water Heater ...
Page 58: ...58 Figure 40 Bare Boiler Assembly ...
Page 62: ...62 SERVICE RECORD DATE SERVICE PERFORMED ...
Page 63: ...63 SERVICE RECORD DATE SERVICE PERFORMED ...
Page 64: ...64 ...