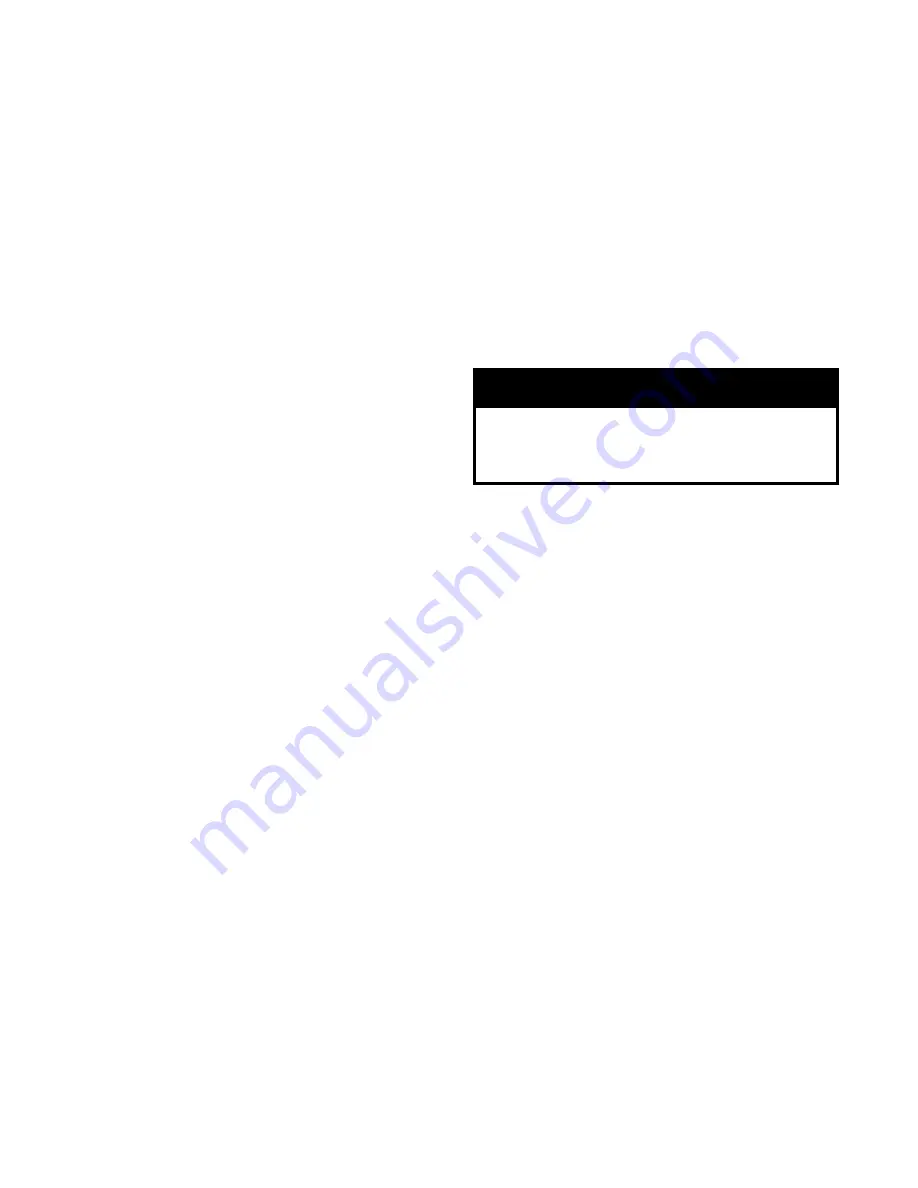
30
i.
If minimum return water temperature can
be maintained at 135°F and temperature
differential across the system is at 40°F
or less, refer to Figure 26 or 27 for
recommended minimum boiler piping
details.
ii.
If minimum return water temperature cannot
be maintained at 135°F or the temperature
differential across the system varies, a blend
pump is recommended as a minimum to help
protect the boiler from flue gas condensation
and/or thermal shock. See piping details in
Figure 28. Primary secondary piping with
a by-pass is an alternate to the blend pump
method and is shown in Figure 29.
d. If conditions exist where the boiler is subjected
to prolonged periods of operating conditions
below 135°F, other mixing methods such as three
or four way valves or variable speed injection
should be used. Burnham Commercial offers an
RTC Return Temperature Control kit to protect
the boiler. See separate RTC manual.
e. Multiple Boilers - Recommended minimum
multiple boiler piping is shown in Figure 30 as
primary secondary with a by-pass. The boiler
circulator will maintain a constant flow through
the boiler during every heat demand while the
by-pass diverts a portion of hot water back to
the return. Alternate minimum multiple boiler
piping is shown in Figure 31. The blend pump
will maintain constant flow through the boiler
during every heat demand and provide a hot
water blend back to the return.
f. Glycol Antifreeze Solutions - Many systems
today use ethylene or propylene glycol antifreeze
solutions as a measure for freeze protection, as
well as a pump lubricator and corrosion inhibitor.
The properties of the glycol mixture have an
impact on valve and pump sizing. All glycol
solutions have a lower specific heat than water.
This means that the glycol solution cannot
transfer heat as well as pure water, resulting in
the need for higher flow rates. In addition, the
viscosity of the glycol solution is usually higher
than water, requiring a higher pump head for the
same given flow. Consult factory for specific
applications, pump selection and flow rate.
WARNING
A properly constructed Hartford Loop must be
installed on all gravity return steam systems.
Hartford Loop is not required on pumped return
systems.
2. STEAM HEATING - For piping details, see Figure
32. Figure 33 shows a typical pumped return/boiler
feed unit arrangement. Figure 34 illustrates the
required elevations for McDonnell and Miller 150
and 63 float low water cut-offs.
Summary of Contents for operating and
Page 2: ...2 ...
Page 8: ...8 Section I General Information Figure 1 Dimensional Information ...
Page 21: ...21 Figure 16 Bare Boiler Assembly ...
Page 25: ...25 Figure 22 V9A Series Jacket Assembly Boiler Models V903A thru V912A ...
Page 31: ...31 Figure 26 V9A Series Minimum Piping Parallel Water Boiler ...
Page 32: ...32 Figure 27 V9A Series Minimum Piping Primary Secondary Water Boiler ...
Page 33: ...33 Figure 28 V9A Series Minimum Piping Details Bypass with Blend Pump Water Boiler ...
Page 34: ...34 Figure 29 V9A Series Minimum Piping Primary Secondary with Bypass Water Boiler ...
Page 37: ...37 Figure 32 Minimum Piping Requirements For Gravity Return V9A Series Steam Boilers ...
Page 42: ...42 Figure 37b DHW Generation with Tankless Coils Storage Tank and Destratification Pump ...
Page 43: ...43 Figure 37c DHW Generation with Indirect Water Heater ...
Page 58: ...58 Figure 40 Bare Boiler Assembly ...
Page 62: ...62 SERVICE RECORD DATE SERVICE PERFORMED ...
Page 63: ...63 SERVICE RECORD DATE SERVICE PERFORMED ...
Page 64: ...64 ...