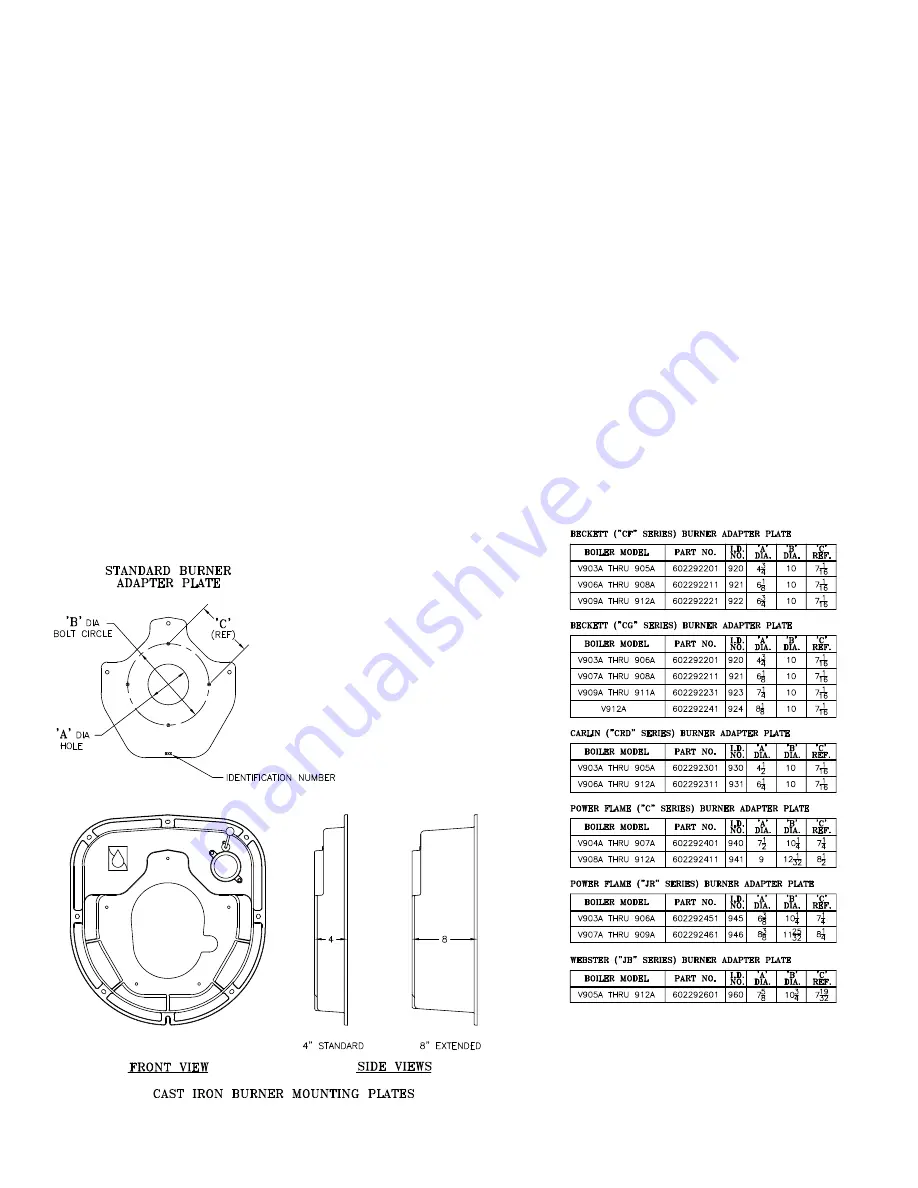
26
8. Combination Label and Burnham Logo Plate were
attached to jacket front panel at time of manufacture.
If loose or peeling, apply pressure to reset adhesive.
9. On steam boilers, attach lowest permissible water
level plate (from steam trim carton) to the front
panel using sheet metal screws.
10. Tighten all sheet metal screws to complete jacket
assembly.
F.
BURNER MOUNTING PLATE
- Refer to Figures 16
and 23.
1. Using silastic sealant, secure the 3/16” diameter
rope gasket to the groove along the mounting plate
opening in the front section.
2. Install 5/16” x 1” lg. cap screw in lower tapping on
front section to carry weight of burner mounting
plate.
3. Engage bottom slot on burner mounting plate with
matching bolt in bottom tapping of front section.
Align mounting holes and fasten the mounting plate
to the boiler sections with seven (7) remaining 5/16”
cap screws and washers. Fully tighten all bolts.
G.
MOUNT BURNER ADAPTER PLATE TO
BURNER MOUNTING PLATE.
Refer to Figures 16 and 23. ALSO, REFER TO
BURNER INSTALLATION MANUAL FOR
INSTRUCTIONS SPECIFIC TO EACH BURNER.
1. In all cases, the burner adapter plate carton for the
specified burner will be provided by Burnham.
2. Open Adapter Plate carton and remove contents.
Apply four (4) small dabs of silastic on rear surface
of adapter plate to temporarily hold gasket in
place. Hold adapter plate in position against burner
mounting plate, align holes and secure with five (5)
3/8” lock washers and 3/8” x 7/8” lg. cap screws.
3. USE A HOLE SAW OR KNIFE TO CUT
BURNER MOUNTING PLATE INSULATION
TO MATCH HOLE SIZE ON BURNER
ADAPTER PLATE. After cutting, remove any and
all loose pieces of insulation which may become
lodged or interfere with the head of a burner air tube
after insertion.
4. Confirm that hole in insulation fits snugly around
burner blast tube. If hole is oversized, remove
burner mounting plate (with burner attached) from
boiler. Use additional fiberglass rope gasket
provided with burner to fill in any space between
Figure 23: Burner Mounting Plate/Burner Adapter Plate Options
Summary of Contents for operating and
Page 2: ...2 ...
Page 8: ...8 Section I General Information Figure 1 Dimensional Information ...
Page 21: ...21 Figure 16 Bare Boiler Assembly ...
Page 25: ...25 Figure 22 V9A Series Jacket Assembly Boiler Models V903A thru V912A ...
Page 31: ...31 Figure 26 V9A Series Minimum Piping Parallel Water Boiler ...
Page 32: ...32 Figure 27 V9A Series Minimum Piping Primary Secondary Water Boiler ...
Page 33: ...33 Figure 28 V9A Series Minimum Piping Details Bypass with Blend Pump Water Boiler ...
Page 34: ...34 Figure 29 V9A Series Minimum Piping Primary Secondary with Bypass Water Boiler ...
Page 37: ...37 Figure 32 Minimum Piping Requirements For Gravity Return V9A Series Steam Boilers ...
Page 42: ...42 Figure 37b DHW Generation with Tankless Coils Storage Tank and Destratification Pump ...
Page 43: ...43 Figure 37c DHW Generation with Indirect Water Heater ...
Page 58: ...58 Figure 40 Bare Boiler Assembly ...
Page 62: ...62 SERVICE RECORD DATE SERVICE PERFORMED ...
Page 63: ...63 SERVICE RECORD DATE SERVICE PERFORMED ...
Page 64: ...64 ...