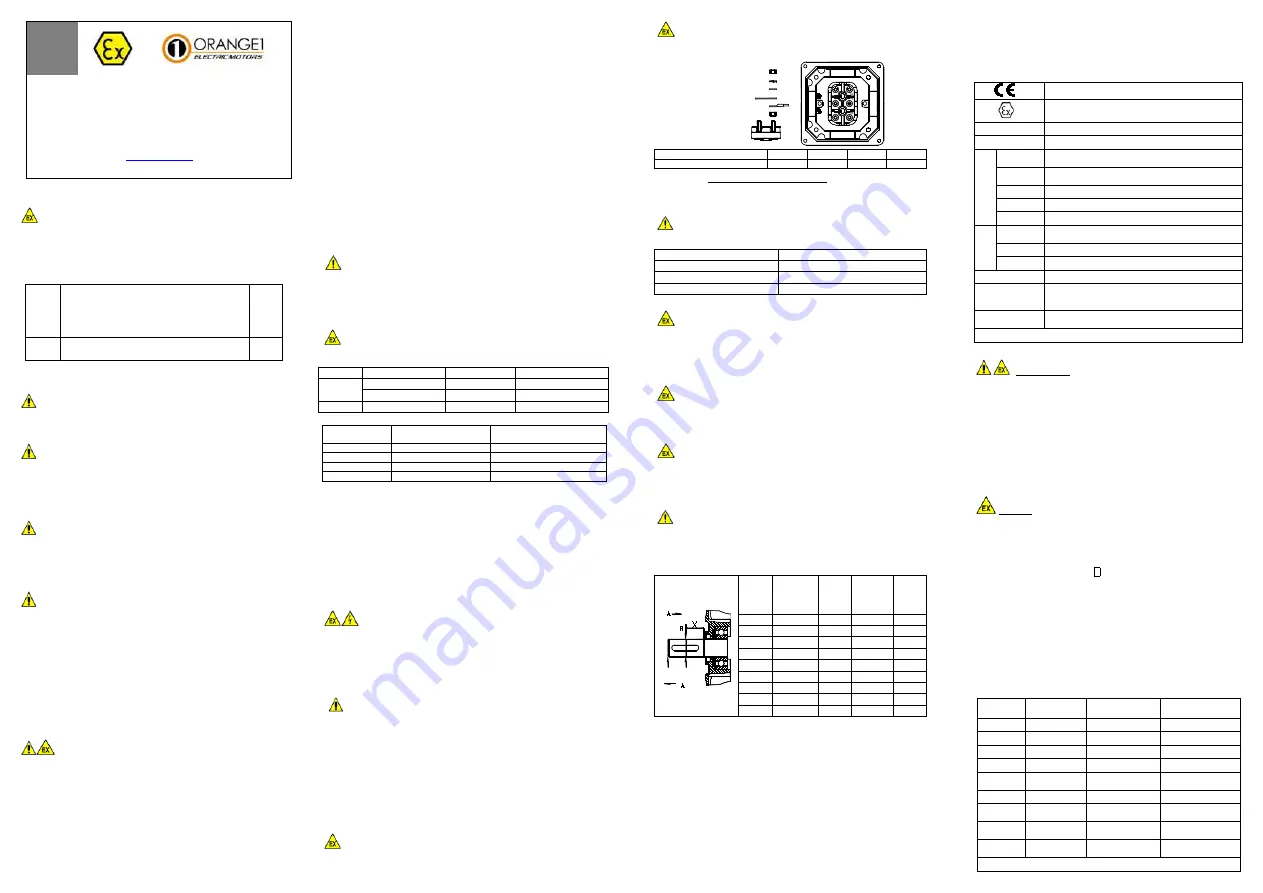
GB
Motors series O-M
Safety, installing
maintenance instructions
www.orange1.eu
(Rev.00 – 28-01-2019)
1.
GENERAL SAFETY INFORMATION
These security instructions refer to the installation, utilization and
maintenance of motors O-M series to be used in potentially explosive areas
with presence of combustible GAS and/or DUST. The information of these
instructions are only for qualified personnel. Except for the opening of terminal
cover, any other opening cancels the warranty conditions of the motors.
Here below you can see the different markings of the motors and the different
zones where they can be used:
GAS
II 2G Ex db IIC T3 Gb T.amb –40°C , +60°C
II 2G Ex db IIC T4 Gb
T.amb –40°C , +60°C
II 2G Ex db IIC T5 Gb
T.amb –40°C , +40°C
II 2G Ex dbeb IIC T3 Gb
T.amb –40°C , +60°C
II 2G Ex dbeb IIC T4 Gb
T.amb –40°C , +60°C
II 2G Ex dbeb IIC T5 Gb T.amb –40°C , +40°C
Zones
1, 2
DUST
II 2D Ex tb IIIC T125°C T.amb –40°C , +60°C
(maximum thicknes of dust layer 5mm)
Zones
21, 22
The motors comply with the Essential Health and Safety Requirements for
potentially explosive atmospheres provided by European Standards:
IEC/EN 60079-0, IEC/EN 60079-1, IEC/EN 60079-7, IEC/EN60079-31
Electric rotating machines present dangers from live and rotating parts,
and probably very hot surfaces. All work on them including transportation ,
connection , commissioning and maintenance must be by qualified and
responsible specialists ( IEC 364 must be observed). Inadequate work can
lead to severe damage to persons and property.
It is imperative to observe the data printed on the nameplate before
operating the motor. Low voltage motors are components to be installed into
machines in accordance with Directive 2006/42/EC.
Commissioning is not allowed until the conformity of the end product with this
directive has been established.
These asynchronous motors comply the EMC (2014/30/UE) Directive and no
particular shielding is necessary when connected to a pure sinewave voltage
supply.
Before working on the motor, ensure it has stopped and is disconnected
from the power supply (including auxiliary equipment).If there is any form of
automatic starting, automatic resetting, relays or remote starting, avoid any
possibility
of
unexpected
re-starting,
paying
attention
to
specific
recommendations on equipment application.
2. TRANSPORT, STORAGE
On receipt verify that the motor has not been damaged during transport
and in this case avoid any installation and communicate immediately to the
transport service.
Eyebolts, when provided with the motor, must be tightened properly as they
are suitable only for lifting the motor, no additional loads are allowed to be
attached. If necessary use sufficiently dimensioned devices as a means of
transport.
Do not use any projection of the motor body to hang the motor for transport
purposes.
If two eyebolts are present on the motor use both for lifting.
Store low voltage motors in a dry, dust free and low vibration (v eff <0,2 mm/s)
area to prevent bearing damage. Before commissioning, the insulation
resistance must be measured. In case of values < 1,5 M< the winding must be
dried. Contact our technical department directly for information on the drying
procedure.
3. INSTALLATION
Installation must comply with the rules of the standard IEC/EN
60079-14 or with the national standards (edition into effect).
Before the installation in an explosive atmosphere, the installer must ensure
that the motor is suitable for the classified area in consideration of the different
inflammable substances present in the installation area (
please verify the
marking on the motor plate before installation
).
The motor must be installed only by qualified people with knowledge about
electrical apparatus for explosive gas atmospheres and electrical installations
in hazardous areas and has to be done with the motor and driven machine at
standstill, electrically dead and locked against restart.
The rating on the nameplate corresponds to voltage and frequency of the
power supply and all other electrical and mechanical data, as well as the
safety data regarding the motor (protection type, temperature class, ambient
temperature etc.).
. The coupling components must also be balanced with a half key on a smooth
mandrel. Coupling belts and pulleys must be assembled by suitable tools to
protect the bearings.
After assembly check that the coupling components are well fixed on the shaft end;
they must be properly pushed against the shaft shoulder. Where the hub of the
coupling gear is shorter than the shaft end, compensate the difference by use of a
bush spacer.
Too large or too small pulleys can impair the shaft bearing life; similarly excessive
belt tension can cause low bearing life or shaft breakage.
The motors must be installed in a proper position so that cooling air can go in and
out easily. The ventilation must not be hindered and the outgoing air - also from
adjacent units - must not be directly sucked in again. To keep a good cooling of the
motor, there must be a minimum distance of 40mm between the fan cover and
another element capable to reduce the air aspiration of the ventilation. Avoid heat
sources near the motor that might affect the temperatures both of cooling air and of
the motor.
In case of outdoor installation protect the motor from solar radiation and extremes
of weather. In case of vertical mounting with shaft down use fan cover with rain
roof.
It is advisable to protect the motor with such as overcurrent devices and torque
limiters where it is not protected by winding temperature transducers connected to
appropriate switchgear.
In case of environments with wide thermal excursions and when can be preview
the presence of moisture, Orange1 EM will equip the motor with heaters.
Instead of use anti-condensation heaters, is possible to supply the motor on pins
U1-V1 with a voltage 4-10% of the rated motor phase-voltage; 20-30% of the rated
current is enough to heat the motor.
Check the direction of rotation with the motor not coupled fastening the shaft
key to avoid its violent ejection during rotation.
If the direction of rotation is not as desired, disconnect the motor and wait
until the motor is completely stopped:
in case of three phase motors interchange two phases at the terminals.
in case of single phase motors refer to the diagram supplied with the motor
Cable entries
Depending on the type of protection of the motor the cable entries shall
comply with the standards written in the table and having the range of
temperature of the motor itself:
Type of protection
T.amb
Standard
GAS
Ex eb
–40°C , +60°C
IEC/EN 60079-0, 7
Ex db
–40°C , +60°C
IEC/EN 60079-0, 1
DUST
Ex tb
–40°C , +60°C
IEC/EN 60079-0, 31
The cable diamaeter for each size of cable gland are like below:
Cable gland
thread
Motor
size
Range of cable diameter
(mm)
M16x1.5
(*) on request
6-12
M20X1.5
56-63-71-80-90-100-112
6-12 / (*)9-16
M25X1.5
132
12,5-20,5
M32X1.5
160-180
17-26
Cable glands and plugs if not supplied with the motor shall be like above.
The cable glands shall be completely screwed to the motor with a
tightening torque of 5Nm
As the feet can be mounted on the frame it is possible to fix them in 3 different
positions so to have the possibility to have the terminal box on the top or on the right
and left sides of the motor.
At the same time the terminal box can be mounted on the motor so to have the
cable entries where it is necessary. So the cable entries can be in the four different
positions. This operation has to be done before connection, removing the box cover,
unscrewing the 4 screws that fix the box to the motor and screwing them completely
in respect of the tightening torque of 5Nm.
4. CONNECTION TO THE POWER SUPPLY
Only qualified people are allowed to connect the motor to the power
supply.
The connection to the electric supply must be done by through the cable entry
supplied with the motor or through another type of cable entry certified in
accordance with the European Standards showed above in compliance with
Directive 2014/34/EU and IECEx approved.
In case of motor complete with cable, the free end of the cable should be
connected in a safe zone or inside an Ex enclosure with a type of protection
suitable for the explosive atmosphere.
Always refer to the data printed on the nameplate for voltage and frequency
to ensure the motor is appropriate for the mains supply.
If not specified it is possible to assume tolerances of ±5% on voltage and ±1% on
frequency indicated on the nameplate (X on the certificate number.
For motor with temperature class T3 and T4 is possible to have ±10% on voltage.
The connection diagrams are normally supplied together with the motor or are
printed in the terminal box. If they are missing please refer to this manual or
contact directly to our technical office.
Check and make sure that, in the case of star /delta start, the switching from star
to delta can only be executed after the starting current of the star step has fallen;
this is important because of the risk of not allowed operational loads.
The cable size choice must be suitable to the motor ratings and the plant type.
The motors shall be protected by a tripping device, which in case of breakdown
could cut off the power supply before the surface temperature exceeds the ignition
temperature of the explosive atmosphere.
The motors with increased safety terminal box (“eb”) are built with a special
terminal board with improved insulation and distances.
The Ex d motors have a normal terminal board.
The power connection shall be made as in the picture. The nuts shall have to
be tightened enough so to avoid any loosening.
TERMINAL BOARD
NUT
TERMINAL
CONNECTING PLATE
WASHER
SPRING WASHER
W1
V1
U1
V2
U2
W2
NUT
Thread
M4
M5
M6
M8
Tightening Torque (Nm)
1,5
2
3
6
IMPORTANT: Motors with Ex eb terminal box REPLACE THE GASKET
(SEAL) IN THE RIGHT POSITION BEFORE CLOSING THE TERMINAL
BOX AND SCREW COMPLETELY ALL THE SCREWS.
Earth connection
In addition to the earth screw terminal fitted inside the terminal box,
another external one must be on the motor frame. If the line conductors have a
section S the earth connections have to be:
Earth conductor
Line conductors
= S
S
16 mm
2
16
16 mm
2
< S
35 mm
2
0,5 S
S > 35 mm
2
Connection of auxiliary cables (“e” terminal box)
If the motor is provided with terminal board with auxiliary pins the
connection of thermal protection and/or heaters can be made in such pins.
If the motor is provided with just a terminal board having just the 6 mains pins
the connection of thermal protection and heaters have to be made by welding
the wires of auxiliary devices with the wires of the cable and insulate using a
heat-shrink sheath.
Protection
The motor must be protected by a tripping device that in case of
breakdown, cut off the supply of the motor so that the surface temperature of
the parts in contact with the explosive atmosphere doesn’t reach the ignition
temperature.
Motors for inverter duty
In case the motors are supplied by inverter, they shall be provided with
protectors inside the windings (normally PTC thermistors), capable of assuring
the respect of temperature class limits..
Such devices shall be connected to a control device able to cut off power to the
motor in case of reaching of the limit temperature.
Heaters
The heaters shall be supplied only when the motor is not under power.
Tha cables have to be adequate for a power of 25W with supply that can be
from 110V up to 240V (±10%).
Permissible load
Assuming a life-span of 20.000h for 2P motors and 40.000h for 4,6,8P motors:
ù
Pull
Thrust
F
F
L
L/2
F
Motor
size
Bearings
Max
radial
load
in L/2
Max
axial
load
(Thrust)
Max
axial
load
(Pull)
63
6202
365
230
120
71
6202
450
280
160
80
6204
590
370
220
90
6205
645
400
230
100
6206
920
560
350
112
6306
1280
700
480
132
6308
1345
770
590
160
6309
2465
1401
714
180
6310
3000
1498
615
Allowed duty services
S1
: Continosus duty the motor works at a constant load until thermal
equilibrium is reached.
S2
: Intermittent duty: Once started, the motor works at a constant load for a
limited period and thermal equilibrium is not reached. Motor will be started a
second time then when its temperature has decreased to room temperature.
S3
: Intermittent duty: A sequence of identical duty cycles, made up with a time
of operation at constant load and a time at rest. When at rest, the motor is not
fed. Starting current does not significantly influence temperature rise.
S9
: Load and speed vary periodically within the permissible operating range.
Frequent overloading may occur. Tipical of motors supplied by inverter (see
above).
Motors with forced ventilation (IC416)
In case of motors with forced ventilation, the main motor can be supplied only
when the auxiliary ventilation is already working.
5. MARKING
(*)
Marking of conformity to the European Directives
(*)
Specific marking of explosion protection
II (*)
Motor for surface plants (different from mines)
2 (*)
Category 2: high level of protection
G
AS
G (*)
explosive atmosphere due to presence of combustible
gas vapour or mist
Ex db
Flameproof motor and terminal box
Ex dbeb
Flameproof motor, increased safety terminal box
IIC
Gas group, suitable for IIB and IIA
T3, T4, T5
Temperature class
D
U
ST
D (*)
explosive atmosphere due to presence of combustible
dust
Ex tb IIIC
tb enclosures suitable for zone 21 (cat. 2D)
T125°C
Max surface temperature
T.amb
Ambient temperature
AB xx yyy
AB : laboratory which issues the CE type certificate
xx : year of issue of certificate
yyy : number of CE type certificate
ZZZZ (*)
Notified Body that gives the Product Quality Assurance
Notification
(*) Only for ATEX marking
6. MAINTENANCE AND REPAIR
MAINTENANCE shall be performed only by qualified people in
accordance with the standard IEC/EN 60079-17 or national standards (last
edition).
Qualified people must have knowledge about electrical apparatus for
explosive atmospheres and electrical installations in hazardous areas.
- Every 3000 hours of service verify and restore, if necessary, the grease on
the radial seals (for example V-rings).
Periodically (depending on the environment and duty) verify:
- motor cleanliness (oil, DUST, dirt and machining residuals absence) and free
passage of cooling air
- correct tightening of electrical connections, of fastening screws
- free motor running with low vibration (v eff<3,5mm/s for Pn<15KW v eff<4,5
mm/s for Pn>15KW) and absence of anomalous noises; where there is high
vibration and/or noise verify the motor fastenings, machine balancing and that
the bearings are in good condition.
REPAIRS shall be made in accordance with the rules as defined in EN
60079-19 standard.
These repairs can only be done under the control and authorization of
Orange1 EM or by certified repair workshop.
When the repair is made by a certified repair workshop, they must respect all
the original characteristic of the motor and use only original spare parts.
Furthermore they have to place an additional nameplate on the motor with
written a symbol to identify the
R
epair, company name and certification,
repair operation number and date.
Nothing regarding the type of protection can be modified.
In case all these rules are not respected, the motor loses all its characteristic of
certification.
FLAMEPROOF JOINTS CANNOT BE REPAIRED
7. MODULAR COMPONENTS
The motors are completely modular.
Feet and flanges can be mounted without affecting the ATEX certificate, as they
are external and are not part of the type of protection.
In the table here below we show you the screws to be used to mount the
different modular components.
Taglia
Motore
Flange
Piedi
Coperchio
scatola morsetti
63
M5x16
M6x16
M5x14
71
M5x16
M6x16
M5x14
80
M6x20
M6x20
M5x14
90
M6x20
M8x20
M5x14
100
M8x20
M8x30
DADO M8
M5x14
112
M8x20
M8x35 DADO M8
M5x14
132
M10x20
M10X50 DADO
M10
M6x16
160
n.3 M10x95
n.1 M10x70
DADO
M10
M6X20
180
n.3 M10x95
n.1 M10x70
DADO
M10
M6X20
Viti classe 8.8