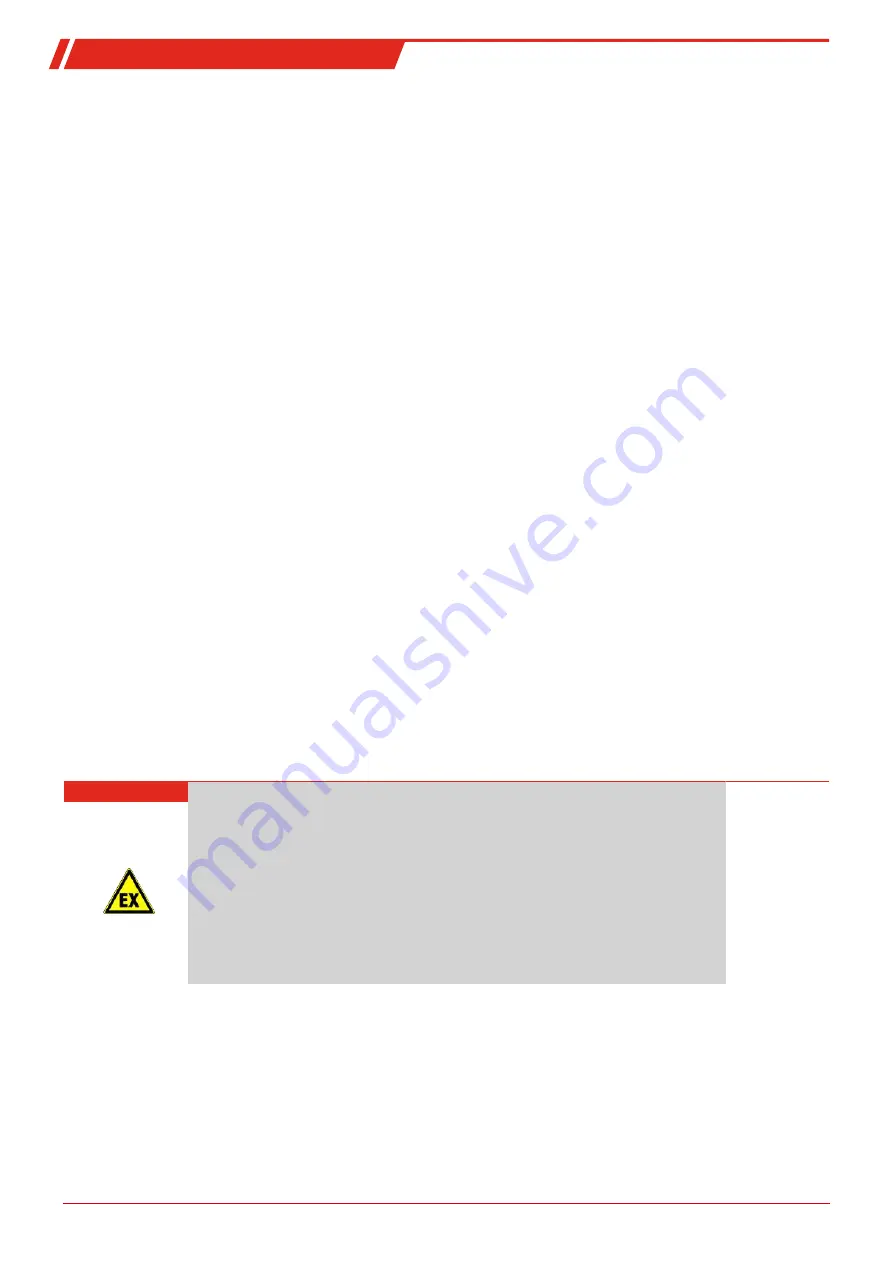
P2.x ATEX
6.4 Replacement of the O-ring of the bypass valve (optional)
Please refer to assembly drawing 42/025-Z02-01-2 in the appendix for this maintenance.
– Loosen the two bolts (24) and carefully pull the entire unit, consisting of valve plate (23), spindle (22) and O-ring (21) on the
knob (26) out of the pump body (13). On VA pump bodies, unscrew the spindle holder (25) with a SW13 open-end spanner,
turning clockwise, and remove the entire unit.
– Remove the old O-ring from the spindle.
– Moisten a new O-ring with suitable O-ring grease (e.g. Fluoronox S90/2) and carefully attach it to the spindle.
– Carefully reinsert the entire unit into the pump body, turning, and tighten the bolts or spindle holder.
– Check the sample gas pump for leaks.
6.5 Replacing the inlet and outlet valves
Please refer to assembly drawing 42/025-Z02-01-2 in the appendix for this maintenance
– Remove the screw-in connections (18) from the pump body (13).
– Unscrew the valves (17) with a wide slot screwdriver. Stainless steel pump bodies have so-called displacers (20) under the
valves. These reduce the dead volume and must remain installed on these pump bodies.
– Screw the new valves into the pump body and tighten to max. 1 Nm. Be sure the valve is installed the correct direction. Valves
for a permitted gas inlet temperature of max. 100 °C are black/red, and grey/orange for max. 160 °C. Here the red or orange
end corresponds to the gas inlet and the black or grey end the gas outlet. The valves at the gas inlet are marked “EIN" and "IN"
and "AUS" and "OUT” at the gas outlet. The marking you see looking into the pump body from above determines the valve
function.
– Lastly, reinstall the screw-in connections in the pump body. In the case of stainless steel screw-in connections, replace any
damaged seals (19).
– Check the sample gas pump for leaks.
– Perform a test run. At a minimum, the following values must be reached:
Overpressure: P2.2/P2.4 Atex = 1.7 bar; P2.72/P2.74 Atex = 1.8 bar
Negative pressure: P2.2/P2.4 Atex = -0.65 bar; P2.72/P2.74 Atex = -0.6 bar
Flow rate: P2.2/P2.4 Atex = 400 L/h; P2.72/P2.74 Atex = 700 L/h
Record the maintenance including test values in the „operating log (template)“ of the sample gas pump.
6.6 Cleaning
6.6.1 Cleaning the pump console
DANGER
Electrostatic charge (Spark formation)
Clean plastic parts and labels with damp cloth only.
Inflame of dust
If the device is used in dust ambiance, remove the layer from the components regularly.
Also remove the dust layer in areas difficult to access.
Conserve the protective effect of the coating
To avoid potential ignition hazard, the protective effect of the coating must not be
derogated by abrasion or corrosive media and must be conserved in any case.
Refinishing or repainting is
not
allowed!
Do not use sharp or pointed tools.
– To clean the inside of the pump console, unscrew the three cross-tip screws (9) of the console cover (8) and remove the cover.
– You can now clean dust and other dirt inside the pump console. Wipe off stubborn dirt with a damp, clean cloth. Do not use
cleaning products containing solvents.
– Now reattach the console cover and tighten the three bolts.
For the item numbers, please refer to the assembly drawing 42/025-Z02-01-2 in the appendix.
23
Bühler Technologies GmbH
BE420002 ◦ 07/2022