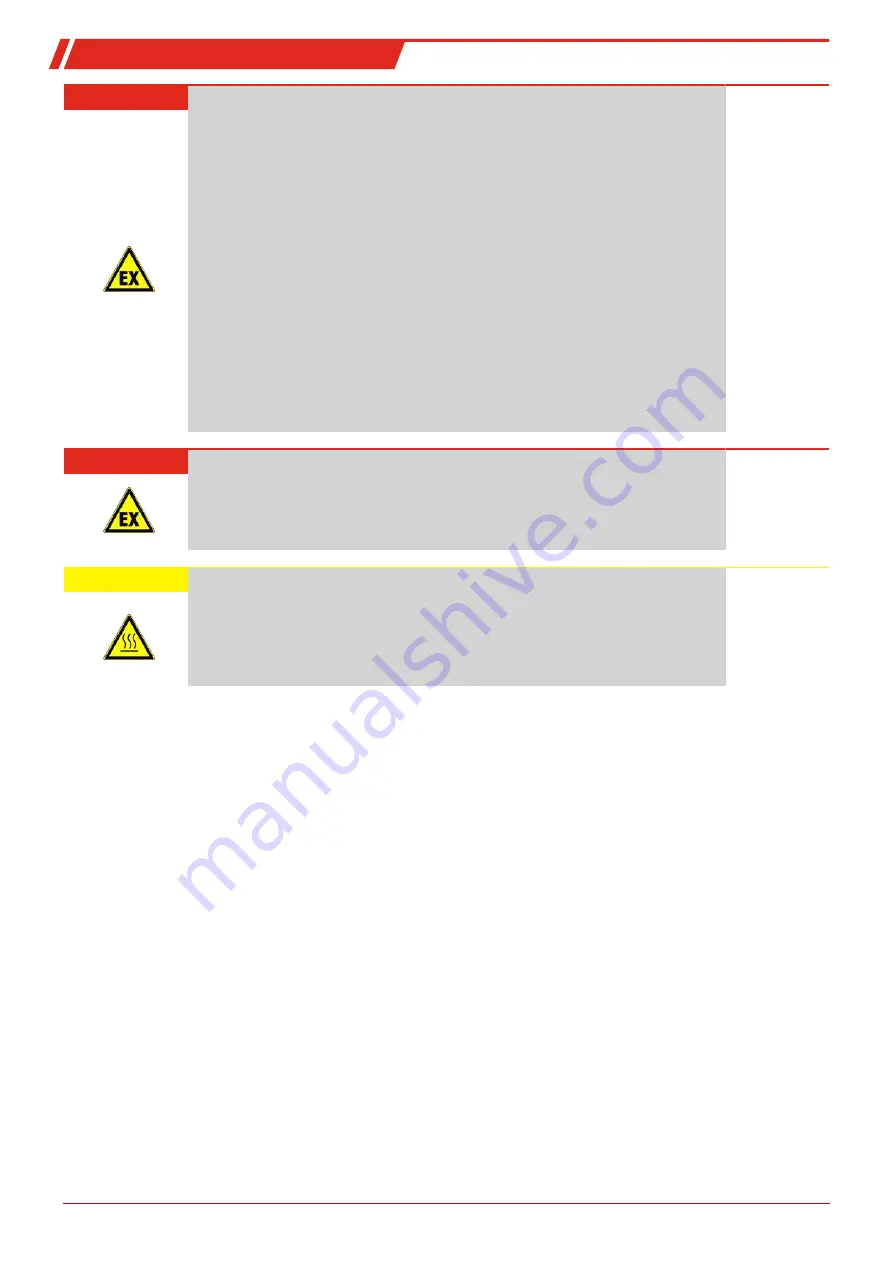
P2.x ATEX
DANGER
Use appropriate tools
According to DIN EN 1127-1, the operator is responsible to select and use appropriate
tools.
Application in explosive atmosphere
Combustible gases and dust may inflame or explode. Avoid the following hazardous
situations:
Electrostatic charge (spark formation)
Clean plastic parts and labels with damp cloth only.
Spark formation
Protect the equipment against external impact.
Install a flame arrester in case of a flashback hazard.
Inflame of dust
If the device is used in dust ambiance, remove the layer from the components regularly.
Also remove the dust layer in areas difficult to access (see chapter "Cleaning").
Conserve the protective effect of the coating
To avoid potential ignition hazard, the protective effect of the coating must not be
derogated by abrasion or corrosive media and must be conserved in any case.
Refinishing or repainting is not allowed!
Do not use sharp or pointed tools.
DANGER
Explosion hazard due to incorrect replacement of components
The replacement of the components requires carefulness. Inexpert operation could lead
to explosion.
If you feel uncertain about any details of the operation, please bear in mind that the re-
placement should be done by the manufacturer only.
CAUTION
Hot surface
Burning hazard
According to the product type and operation conditions, the temperature of the housing
may exceed 50 °C during operation.
Depending on the conditions at the installation site it may be necessary to provide these
areas with appropriate warning signs.
Depending on the quality of the sample gas to be pumped, the valves in the inlet and the outlet may have to be changed from
time to time. A description of the replacement of parts can be found in the “Replacing inlet and outlet valves” section.
If the valves are heavily contaminated, in particular after just a short period of operation, then you should provide for particle
filtration before the pump. This will increase the service life considerably.
Depending on the operating conditions, the following must be performed at suitable intervals (see “Maintenance plan”)
– Inspect the terminal compartments and terminals for cleanliness and clean them if necessary.
– Inspect whether the electrical connections are firmly in place.
– The cooling air channels of the motor are cleaned.
– Carry out an inspection of the radial clearance and a visual check of the elastomer sprocket.
The exhaust ports and the cooling surfaces of the motor must be protected from blocking and impurities.
19
Bühler Technologies GmbH
BE420002 ◦ 07/2022