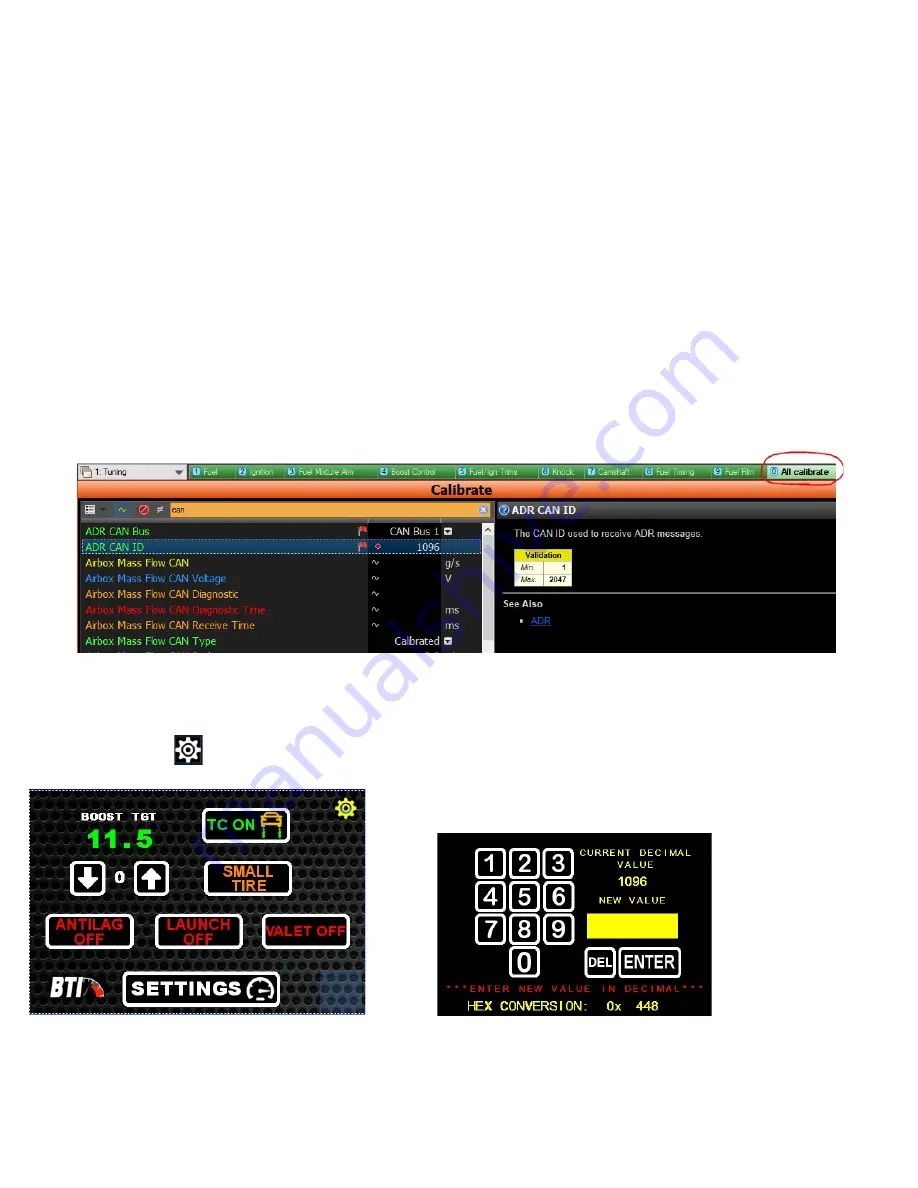
51
Upon powering up a properly terminated gauge, the Gauge will display the interface and version number.
M1 CAN bus options:
This gauge is designed to read the O2 sensor data from an LTC wideband controller.
The gauge will look for sensor #1 data on 0x460 and sensor #2 data on 0x461 which should be default
values. In the event that you do not have an LTC, some of the more popular packages will output the
analog O2 sensor data on the first byte of 0x651.
The gauge will look for O2 sensor #1 data there if no LTC modules are detected.
Torque and Horsepower are not standard parameters in the M1 CAN protocol. The John Reed package
outputs this data on CAN address 0x647 and this display is designed to read those parameters.
Horsepower is a 16 bit word starting at byte 0 where one bit = .1 Watt. Torque is a 16 bit word starting at
byte 16 where one bit = 1 Nm.
Example CAN transmit configuration in M1 Tune
In order to transmit CAN commands over the CAN bus to the M1 ECU, the ADR CAN bus must be
configured The ADR CAN ID is entered in the M1 Tune software as a decimal value.
The same value must be entered into the BTI touch screen as a decimal value as well:
**Note that CAN XMIT must be enabled in the setup screen.
Press the white cog wheel in order to enter the CAN control screen:
Press the yellow cog wheel in order to configure the ADR CAN
ID
Once the ADR CAN ID is configured, the inputs for the control buttons must be configured in the M1 Tune
software
Summary of Contents for 4.3 TFT
Page 9: ...9 Example Boost Setup ...
Page 12: ...12 ...
Page 13: ...13 EMS 4 CAN Bus wiring ...
Page 30: ...30 ...
Page 32: ...32 ...
Page 38: ...38 ...
Page 48: ...48 MoTeC M1 Integration MoTeC M130 Connector Pin out MoTeC M142 and M150 Pin out ...
Page 49: ...49 MoTeC M170 Pin out A MoTeC M182 M190 Pin out ...