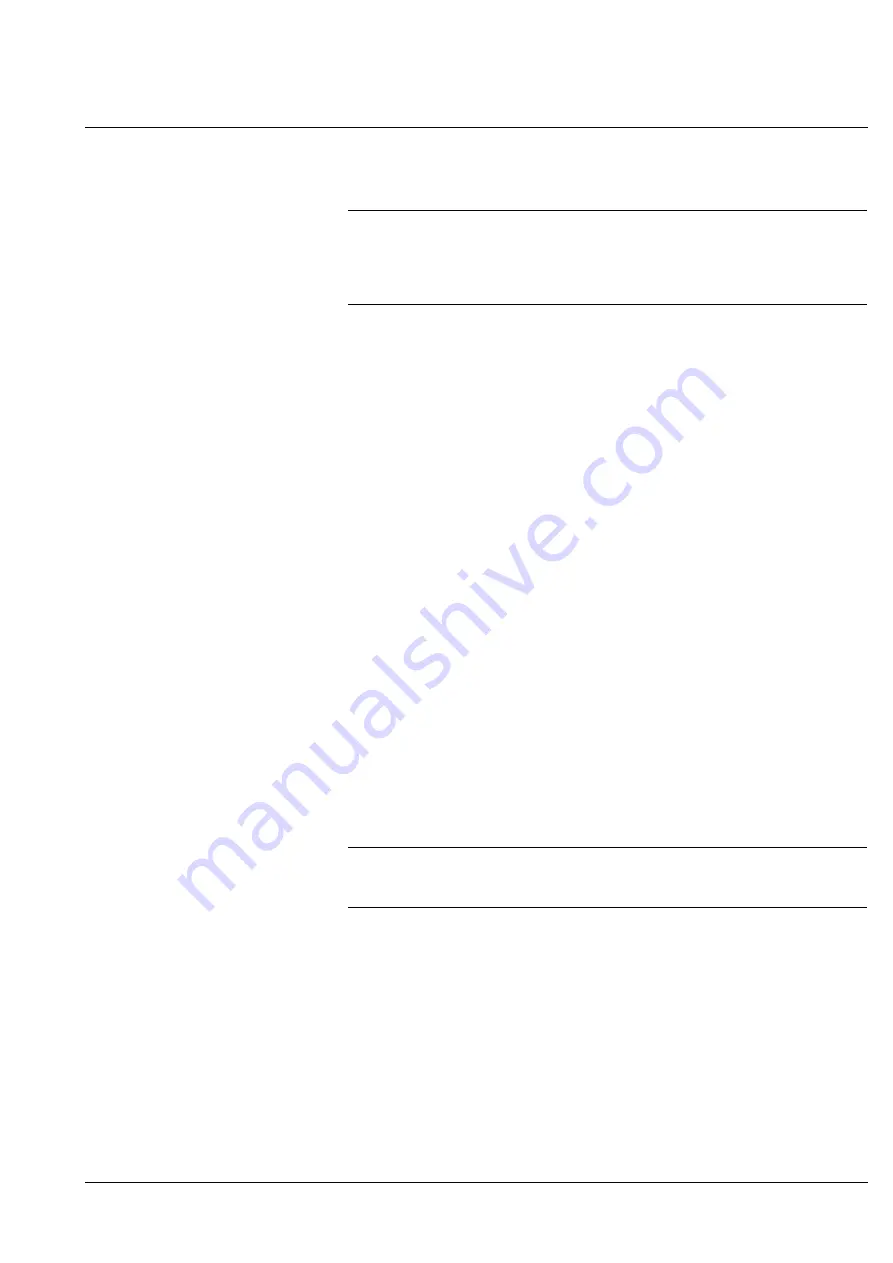
7.3 - Dilution
M2041/5en
SBT-2400 Appendix
63
©BTG 2006
7.3 Dilution
NOTE!
Calculate the dilution water control valve correctly and use a high quality precision
actuator. Make sure that the dilution water pressure is stable and that the water
is injected at high velocity into the pump suction.
Correct dilution is essential to ensure reliable transmitter operation!
Dilution water should be pressure-controlled or otherwise protected from major
pressure variations.
To ensure good control, dilute no more than 20% in each dilution stage,
though a higher percentage may be acceptable early in the process.
If considerable dilution is required it should be carried out in two stages, 70%
to 80% of the water being added in the bottom part of the pulp chest and the
remainder in the form of a fine dilution upstream of the pump.
To avoid consistency variations, thoroughly mix the bottom of the pulp chest
upstream of the transmitter.
The dilution water pipe should be inserted in such a way that it extends 15–50
mm (0.6–2 in), depending upon pipe size, into the main pipe on the suction
side of the pump, see Fig 10. The pipe must be inserted perpendicular to the
suction stud. The pipe should be located at 1/3 of the distance between the
pump and the chest, measured from the pump, to avoid back flow into the
chest.
At the point of injection, the dilution water pipe should be dimensioned to pro-
duce a rate of flow 3–4 times faster than the flow in the main pipe. Typically this
means a dilution water flow
3–5 m/s (10–16.5 fps) at max flow in the suction
pipe. The dilution water pipe should have the same or larger dimension as the
valve bore to prevent the valve being plugged by pulp at water pressure loss.
Choose a dilution water valve with linear characteristics. The pressure drop
over the valve should be at least 0.5 bar (7 psi) and should exceed 25% of the
total pressure drop in the dilution water line. The valve and its actuator must
operate with the least possible backlash and smallest possible dead zone. The
valve must be tight when in its closed position, see Fig 10.
NOTE!
Additional information in
“Accurate Consistency — a hand-book in consistency
measurement in pulp and paper processing”
— available from BTG.