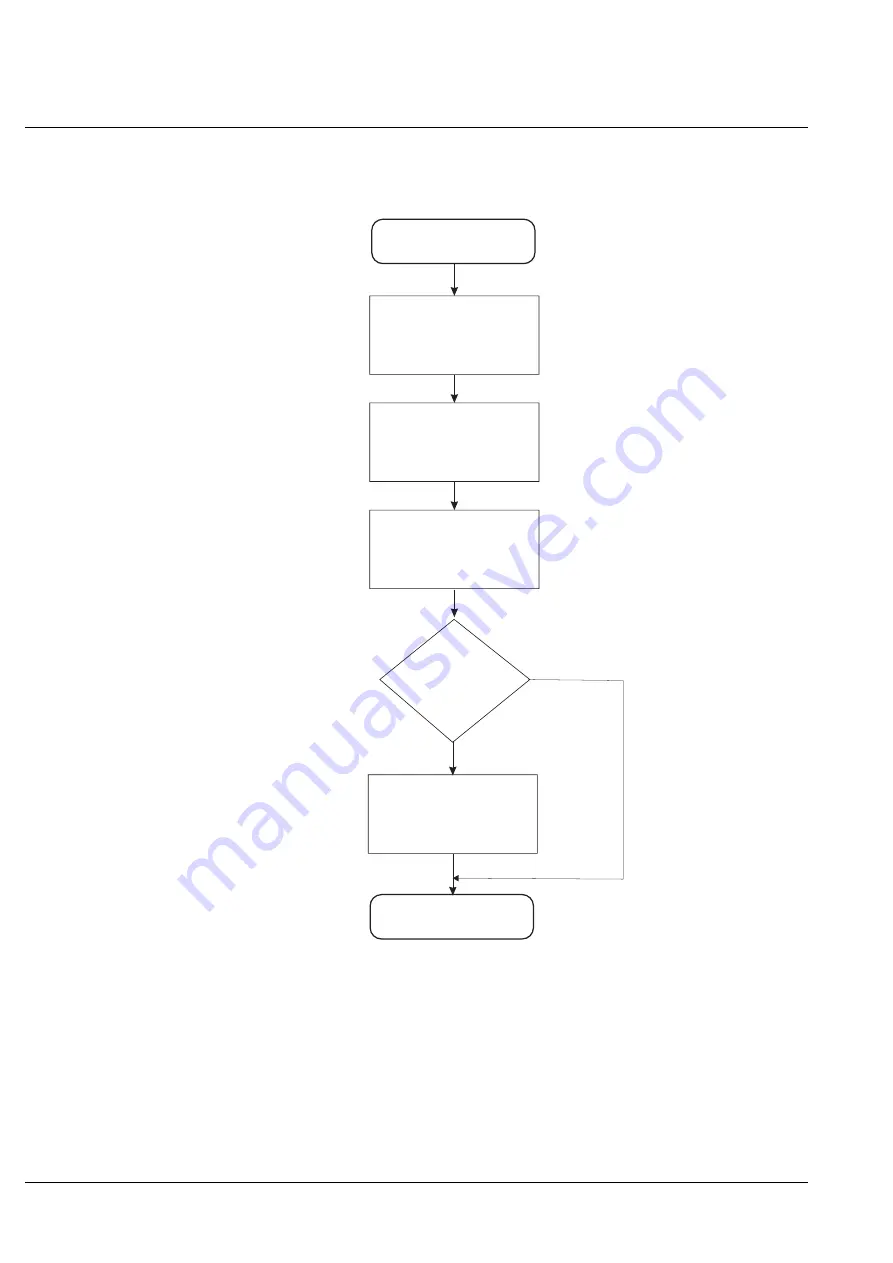
4.2 - Operations with JCT-1200
24
SBT-2400 Operating Instructions
M2041/5en
©BTG 2006
4.2.3.1
Single-point Calibration
Start
Take a lab sample. See
chapter “Take New
Sample Values”.
Calculate the
deviation between
sample and laboratory
measurement.
Is
Multi-point
calibration to
be done
later?
Enter lab-value. See
chapter “Enter Lab
Sample Values”.
Yes
No
Done
Enter new offset
value. See chapter
"Change Offset"