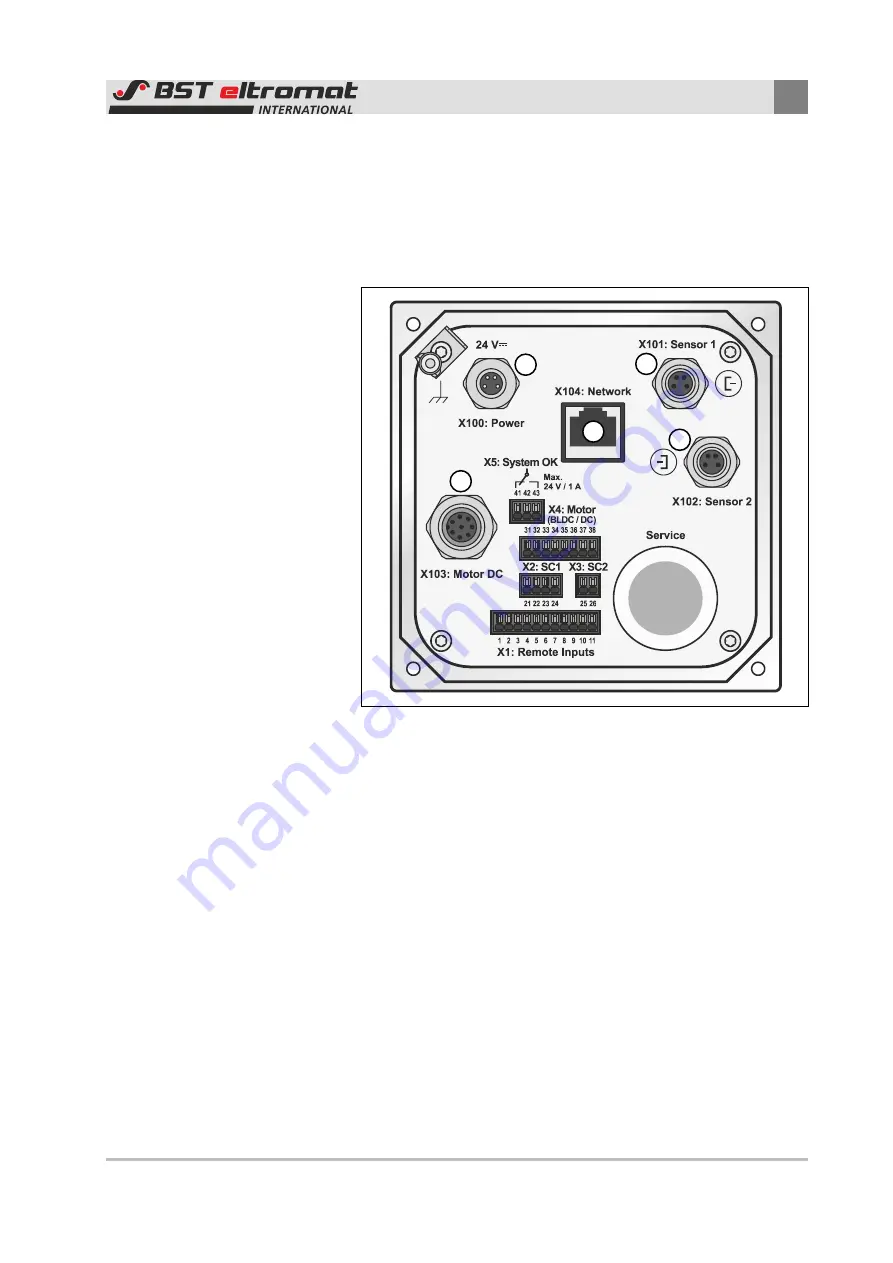
Electrical connection
7
EcoGuide compact web guide control
53/70
7.5 Cable connections
7.5.1 Cable connections for the EcoGuide size 1-3
On the back panel of the
ekr CON 100
controller integrated in the
EcoGuide
the following sockets can be accessed:
Fig. 29: Connections of the controller
①
Sensor 1 (edge sensor)
②
Sensor 2 (edge sensor)
③
Network (Ethernet)
④
Motor actuator
⑤
Power supply
1
4
5
2
3