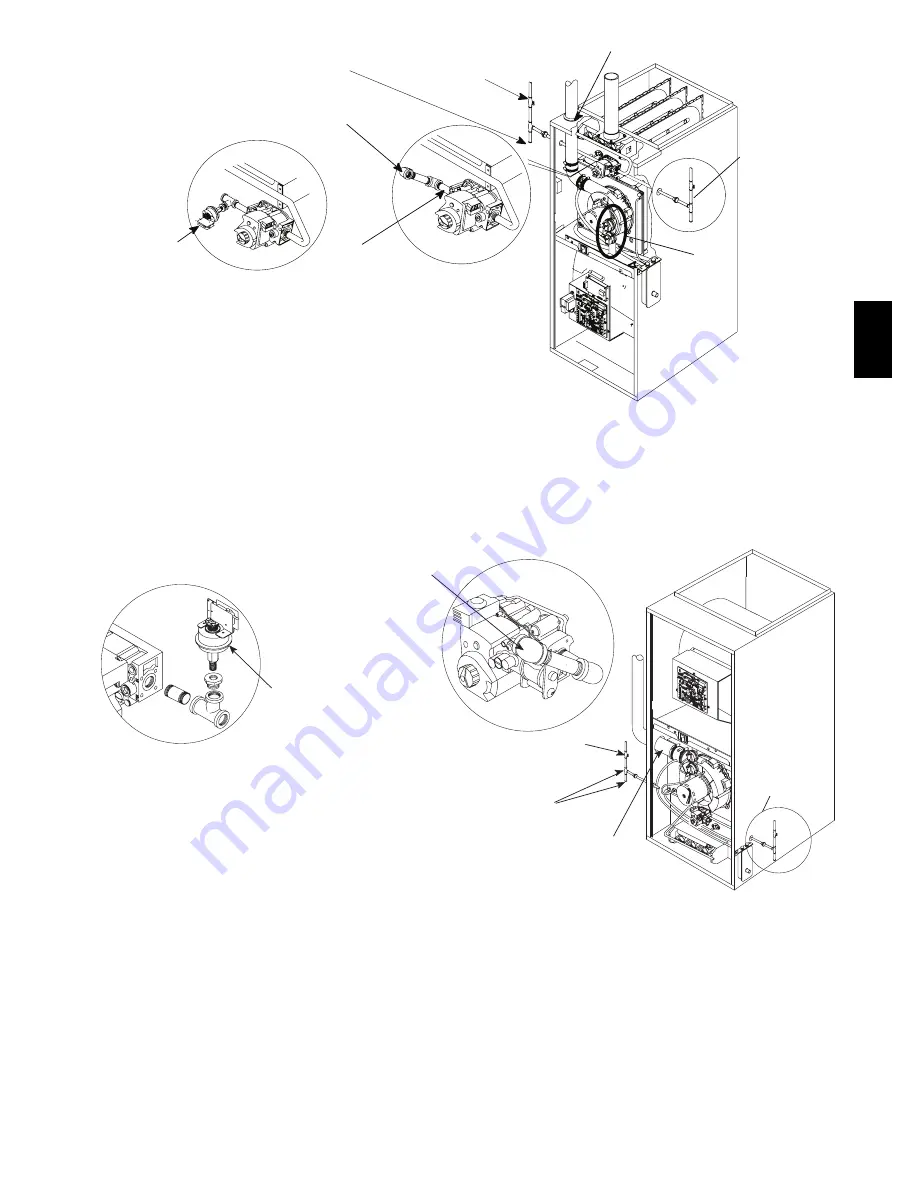
35
ON
OFF
ON
O
FF
O
N
O
F
F
Use elbows and 3
″
pipe nipple to connect valve to
piping when using right side gas pipe entry.
* Union may be installed inside the cabinet when necessary
because of clearances.
Drip Leg and Union, Union* should be outside the
cabinet. Manual shut- off valve MUST be upstream of
dripleg, union, and furnace.
Propane Low pres-
sure switch
REQUIRED.
Vent Pipe Grommet (Single Pipe)
3
″
pipe
nipple
Models may
have 1 or 2
pressure
switches
Manual shut- off
valve
Alternative
installation
Representative drawing only, some models may vary in appearance.
A07724
Fig. 36 -- Typical Gas Piping for Upflow
Use elbows and 3
″
(76 mm) pipe nipple to connect valve to
piping when using left side gas pipe entry.
*Union may be installed inside the cabinet when necessary
because of clearances.
Drip Leg and Union, Union* should be outside the cabinet.
Manual shut--off valve MUST be upstream of dripleg, union,
and furnace.
Propane low pressure
switch.
Gas Pipe Grommet
(Single Pipe)
Manual shut- off
valve
Alternative
installation
A09206
Fig. 37 -- Typical Gas Piping for Downflow
359AA
V