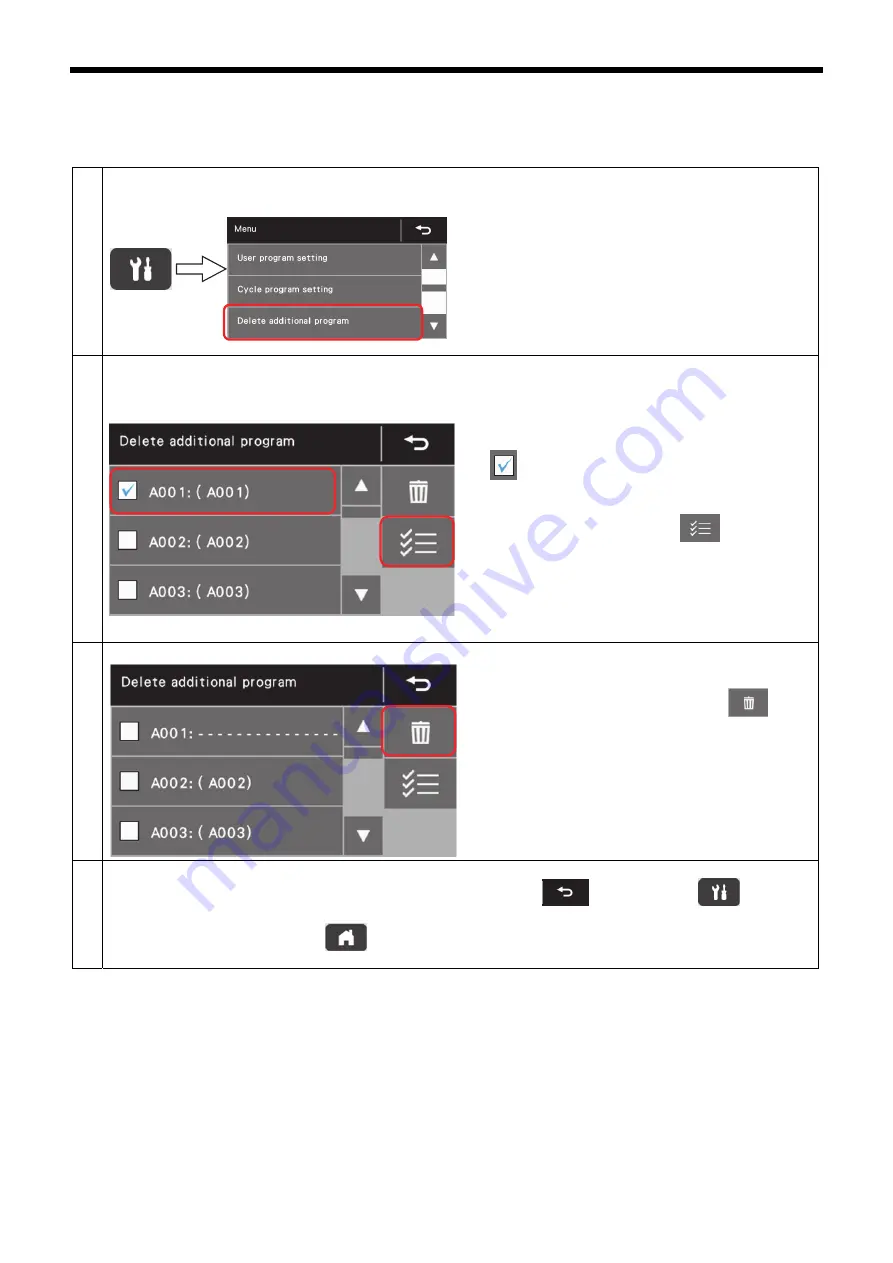
5. SETTING FUNCTION
KE-430HX/KE-430HS, BE-438HX/BE-438HS
54
5-7. Deleting additional programs
Additional programs which are not needed can be deleted.
1
Switch to the delete additional program setting
screen.
Press the menu key to switch to the setting menu screen.
Touch "Delete additional program" in the setting menu
screen to switch to the select delete additional program
screen.
2
Select the program number for the program that you
would like to delete.
Set the program number (1) for the cycle program which
you would like to delete from the list on the screen.
・
Select the number by which the program has been
registered.
・
When you touch a program number, a check mark
will appear against the program number in the
list. (Multiple program numbers can be selected.)
・
You can select all cycle programs in the list (A001 to
A500) by pressing the ALL key
(2).
3
Delete the additional programs.
Once all the additional programs to be deleted have been
selected, you can press the delete key
(3) to
delete the registered sewing patterns which have been
assigned to the additional program numbers which are
currently selected.
・
"---" will be displayed after the program numbers of
the additional programs which have been deleted.
4
<To exit from the additional program deleting screen>
・
At the delete additional program screen, you can press the back key
or the menu key
to return to
the setting menu.
・
In addition, when the home key
is pressed, the display switches to the home screen.
Example: program number A001
(3)
(2)
(1)
Summary of Contents for BE-438HS
Page 203: ...14 ELECTRIC MECHANISM 192 KE 430HX KE 430HS BE 438HX BE 438HS 4313B ...
Page 204: ...14 ELECTRIC MECHANISM 193 KE 430HX KE 430HS BE 438HX BE 438HS 4314B ...
Page 205: ...14 ELECTRIC MECHANISM 194 KE 430HX KE 430HS BE 438HX BE 438HS 4315B ...
Page 206: ...14 ELECTRIC MECHANISM 195 KE 430HX KE 430HS BE 438HX BE 438HS 4316B ...