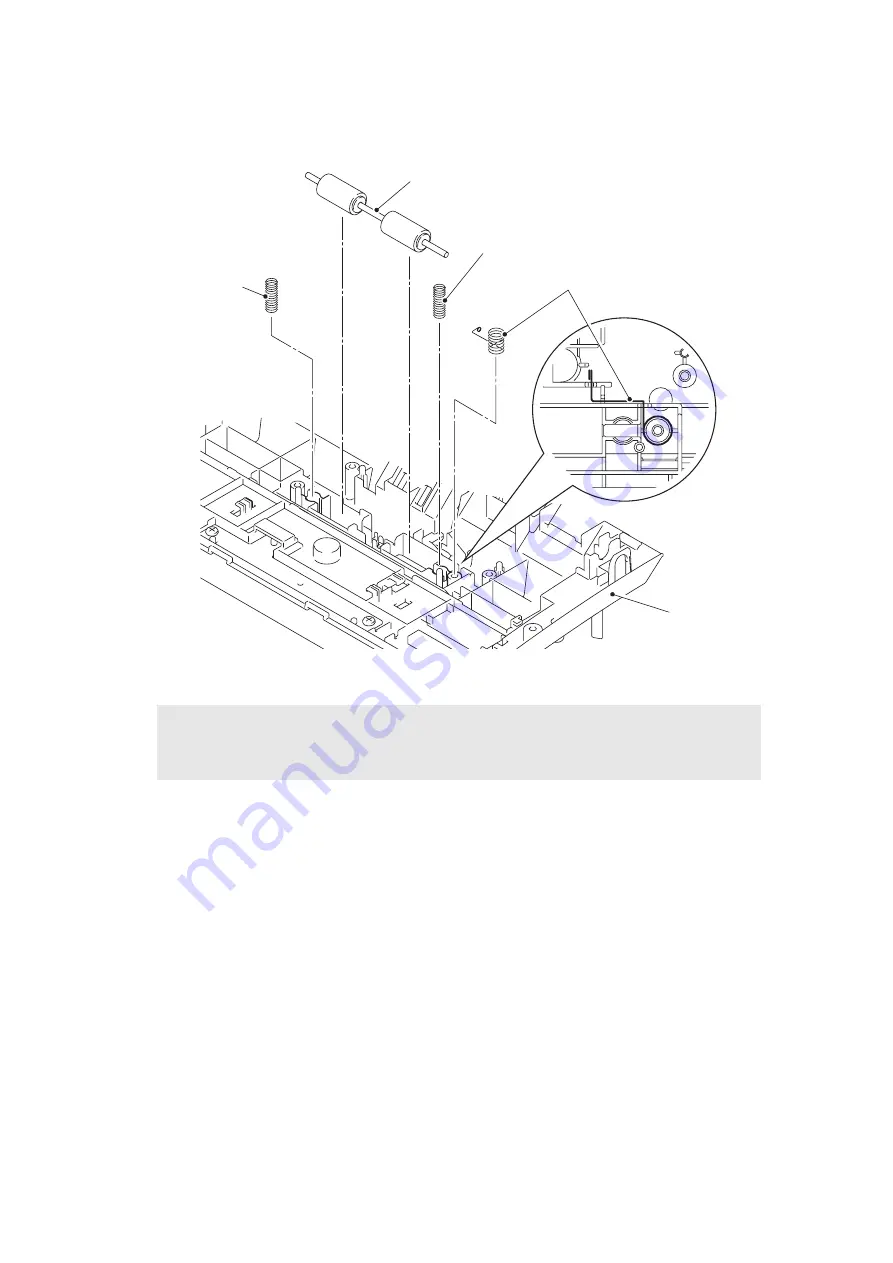
3-28
Confidential
(19) Remove the double feeding sensor earth spring from the upper chute.
(20) Remove the two pinch roller springs to remove the pinch roller shaft from the upper chute.
Fig. 3-26
Assembling Note:
• Attach the double feeding sensor earth spring on the position described in the
illustration above.
Pinch roller shaft
Pinch roller spring
Double feeding sensor earth spring
Pinch roller spring
Upper chute
Summary of Contents for ADS-2000e
Page 15: ...Confidential CHAPTER 1 SPECIFICATIONS ...
Page 22: ...Confidential CHAPTER 2 TROUBLESHOOTING ...
Page 28: ...2 4 Confidential 2 2 Paper Feeding Fig 2 2 Feed path ...
Page 50: ...Confidential CHAPTER 3 DISASSEMBLY REASSEMBLY ...
Page 54: ...3 2 Confidential 2 PACKING ...
Page 93: ...Confidential CHAPTER 4 ADJUSTING AND UPDATING SETTINGS AS REQUIRED AFTER PARTS REPLACEMENT ...
Page 107: ...Confidential CHAPTER 5 SERVICE FUNCTIONS ...
Page 113: ...Confidential CHAPTER 6 WIRING DIAGRAM ...
Page 116: ...Confidential CHAPTER 7 PERIODICAL MAINTENANCE ...
Page 117: ...Confidential CHAPTER 7 PERIODICAL MAINTENANCE CONTENTS 1 PERIODICAL MAINTENANCE PARTS 7 1 ...
Page 119: ...Confidential APPENDIX 1 SERIAL NUMBERING SYSTEM ...
Page 123: ...Confidential APPENDIX 3 INSTALLING MAINTENANCE DRIVER ...