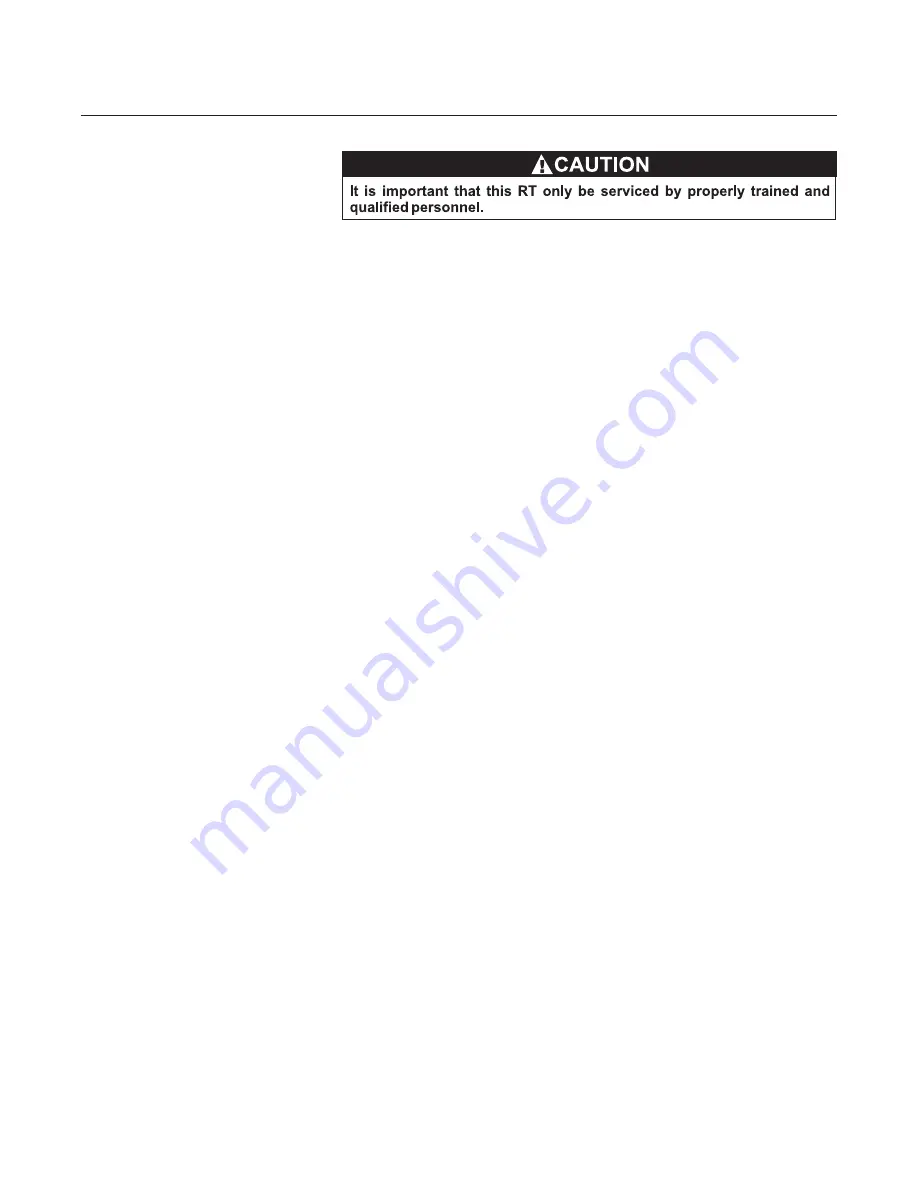
4-2
Brooks
®
Model SLA5840
Section 4 Maintenance
& Troubleshooting
Installation and Operation Manual
X-PR-SLA5840-Series-RevB-RT-eng
Part Number: 541B201AAG
October, 2017
This section contains suggestions to help diagnose simple RT related
problems in the gas distribution system and answers commonly asked
questions.
The Brooks SLA5840 (RT) can operate in mass flow mode as a mass flow
controller utilizing the on board thermal flow sensor, or it can operate in
pressure control mode utilizing the user supplied external pressure
transducer. In most cases, the device would be used as a remote
transducer pressure controller.
The SLA5840 is a Mass Flow Controller designed to utilize a remote
pressure transducer input in its PID control loop. This device will act as a
pressure controller while simultaneously providing a flow signal output.
Each RT is built to order which means it was custom built to operate at
certain specifications as was determined at the time the order was placed.
The Controller can be configured to operate with 0-10 Vdc or 0-5 Vdc as
the Aux/RT input. The command setpoint can also be configured for more
than one type of signal. Please assure your device is being used in the
same way as it is configured.
As a first step to troubleshooting, always be sure the device is installed and
operated according to the order specifications.
When troubleshooting, it is important to understand that the response time
required to increase or decrease pressure is directly related to the flow rate
of the device and the size of the vessel or lines being pressurized.
Performance is also related to any other devices flowing gas into the
pressure vessel and these other devices capabilities.
In troubleshooting, it is very helpful to utilize the BEST software tool
(available on the Brooks Instrument website). With this tool, you can
control the device via your PC and isolate, test, verify and configure I/O.
This tool will allow you to prove device functionality independent of process
control.
Also, this software will allow for switching the device between Flow Control
mode and Pressure Control mode.
In Flow Control mode, the device should simply control flow to a setpoint
command. If this function works in a basic configuration, then the device
functionality can be assumed to function properly.
After proving the device functionality in Flow Control mode, set it to
Pressure Control mode and test in this configuration. The software tool will
allow you to diagnose the input signal to prove it is operating properly.
Keep in mind that the response in Pressure Control mode will be
dependent on the process configuration and available pressures and
flows.
The Controller can be configured to operate with 0-10 Vdc or 0-5 Vdc as
the Aux/RT input. The command setpoint can also be configured for more
than one type of signal. Please assure the device is being used in the
same way as it is configured.