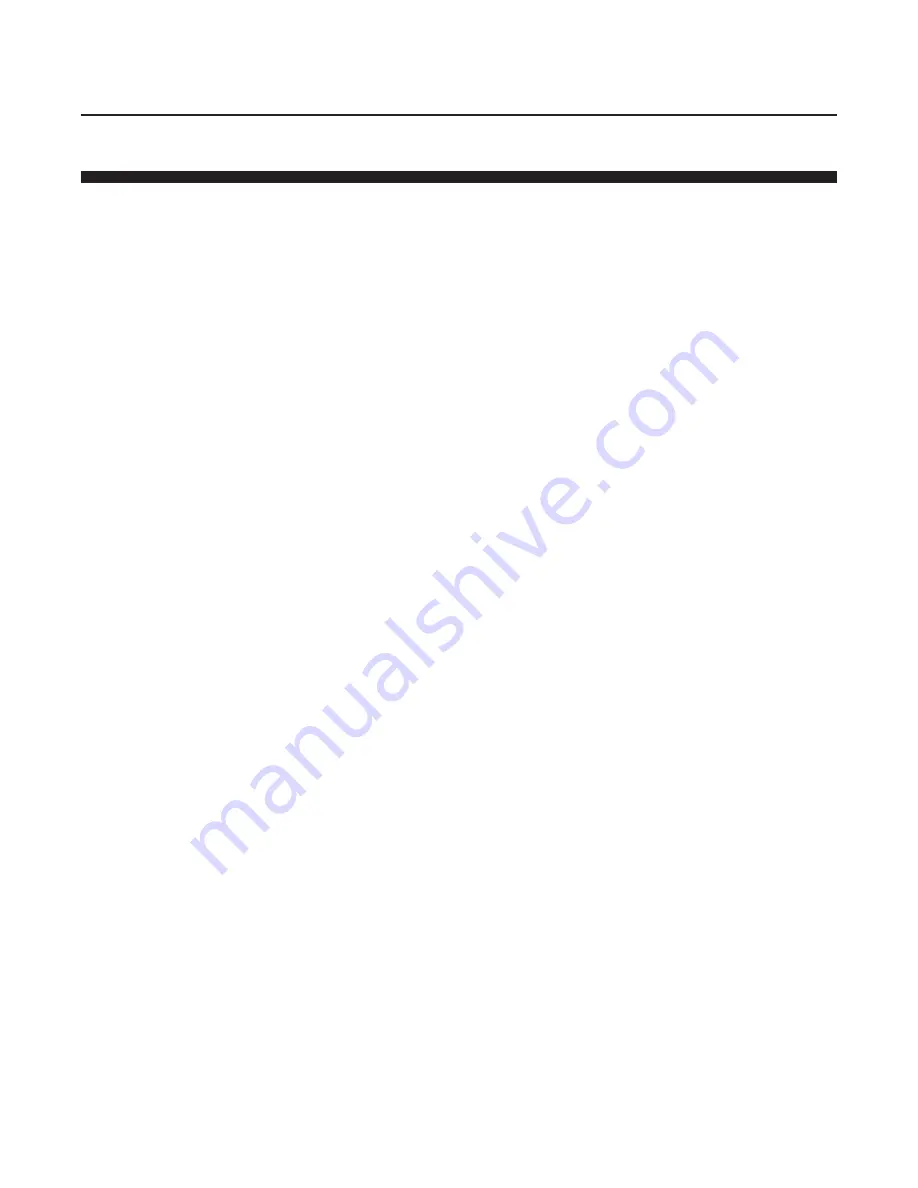
3-4
Brooks
®
Model SLA5840
Section 3 Operation
Installation and Operation Manual
X-PR-SLA5840-Series-RevB-RT-eng
Part Number: 541B201AAG
October, 2017
3-4 Analog I/O Mode of Operation
The following paragraphs describe the basic operation of the Brooks Digital
Series RT's. The DeviceNet, Profibus and RS485 Instruction Manuals
describe further details on specific communication features.
A. Functional Description
When configured in Pressure Control mode, the SLA5840 will utilize the
remote transducer signal in it’s internal PID control. When configured in
Mass Flow Control mode, the device utilizes the internal thermal sensor for
mass flow control. Installation is always in a forward flow direction (through
the sensor, then through the valve).
A typical transducer signal is 0-10 Vdc. The I/O signals can be selected
using the “BEST” software tool (available for free download on the Brooks
Instrument website - specific cable is required) (See Figure 2-1 for
connections)
For best accuracy and performance, apply power and warm-up the
instrument for approximately 45 minutes.
The analog interface may include any of the following I/O options as
specified by the user:
0 - 5 Vdc setpoint, 0 - 5 Vdc flow output
1 - 5 Vdc setpoint, 1 - 5 Vdc flow Output
0 - 20 mA setpoint, 0 - 20 mA flow output
4 - 20 mA setpoint, 4 - 20 mA flow output
0 - 10 Vdc setpoint, 0 - 10 Vdc flow output
Also included is a Valve Override input signal.
All analog signals are available on the 15 pin D-Connector. (See Figure 2-1)
B. Analog I/O Setpoint
The analog interface is consistent with other Brooks devices. The options
for analog input signals are as shown above.
If utilizing the “BEST” software to reconfigure the I/O selection, no A-D/D-A
calibration is required as all I/O options are factory calibrated.
The command input allows the user to establish the RT setpoint.
The full range of the setpoint represents 0-100% of the Flow or Pressure
as specified on the order or label. Setpoints below 0.5% will be treated as
a zero setpoint.
Setpoints above 110% will result in a maximum setpoint of 110% FS.
See Table 1-3 for electrical specifications.
C. Analog I/O Flow Signal
The analog interface is consistent with other Brooks devices.
The options for analog output signals are as shown above.
If utilizing the “BEST” software to reconfigure the I/O selection, no A-D/D-A
calibration is required as all I/O options are factory calibrated.
This output is used to indicate the mass flow rate.
A negative flow signal indicates reverse flow through the device, (Note the
device is NOT calibrated for accuracy in a reverse flow direction).
See Table 1-3 for electrical specifications.