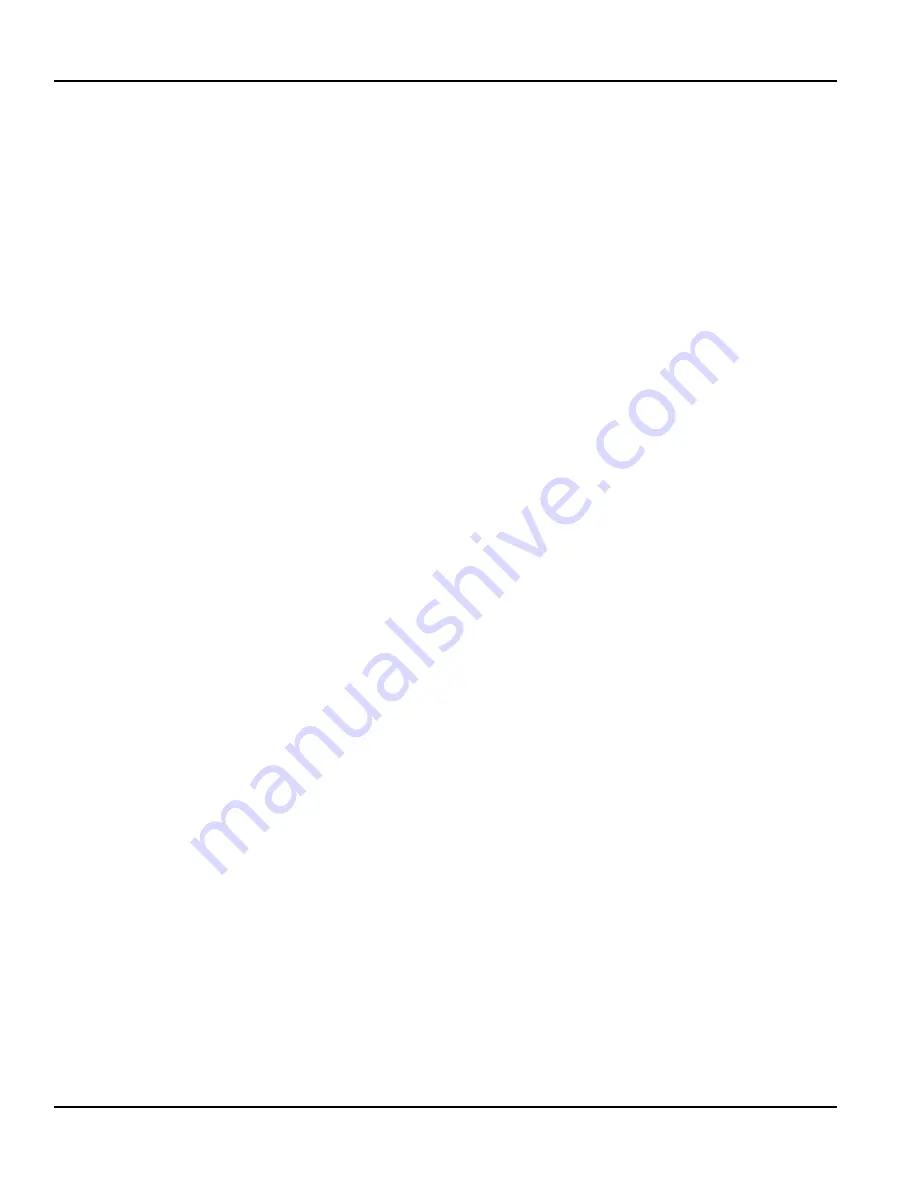
Classic Terrazzo
®
Corner Washfountain with Infrared Control
WF2613
Installation Instructions
Bradley Corporation • 215-1451 Rev. D; EN 06-915B
24
4/6/2007
Thermostatic Mixing Valve Maintenance and Troubleshooting
NOTE: Before attempting to troubleshoot the valve or disassemble the components, check for the
following conditions:
• If stop/check valves are used, make sure that they are fully open
• Make sure that the hot and cold inlet pipes are connected properly, and that there are no cross-
connections or leaking stop/check valves
• check the hot water heater output to make sure that it is at least 20° F above the set temperature.
Be sure to close the appropriate shut-off valves prior to disassembly of the valve and reopen the
valves after inspection and repair is complete.
Problem: Limited water flow
Cause: Dirt and debris have built up in the valve.
Solution: Check the valve's piston for free and smooth movement, follow the procedures outlined
below:
1. Remove the valve's cap and thermostat (see Figure 11 on Page 25).
2. Push down on the piston with your finger (the piston should move freely). If the movement is
not as it should be, the piston needs to be cleaned. Follow the method outlined below for cleaning
the piston and valve body:
• Remove the thermostat.
• Lift the piston out with a needle-nose pliers and remove the spring.
• Any cleaner suitable for brass and stainless steel may be used (if cleaning with suitable cleaner
is not sufficient to remove debris, a 400-grit sandpaper may be used to polish and hone the
piston and valve body).
• Snap spring into piston (will detent) and reassemble into the valve body.
• Retest the piston.
3. If, after a thorough cleaning, the piston does not move freely, the piston must be replaced.
Contact your Bradley representative and ask for Repair Kit (part number S65-259).
Problem: External leaks in the system
Cause: O-rings have been damaged.
Solution: Replace O-rings where necessary. For replacement of the O-rings, contact your
Bradley representative and ask for Repair Kit (part number S65-259).
Problem: Improper water temperature or temperature fluctuation
Cause: Thermostat is slowly failing or not working at all.
Solution: "Check the thermostat for proper operation".
1. At room temperature (80° F or less) remove cap and thermostat.
2. Place thermostat into container with 115° F water. The pushrod should pop out of the
thermostat approximately 1/10".
3. If thermostat pushrod does not pop out, the thermostat must be replaced. Contact your Bradley
representative and ask for Repair Kit (part number S65-259).
Cause: Valve temperature is not properly set.
Solution: "Adjust the temperature" per steps on Page 23.