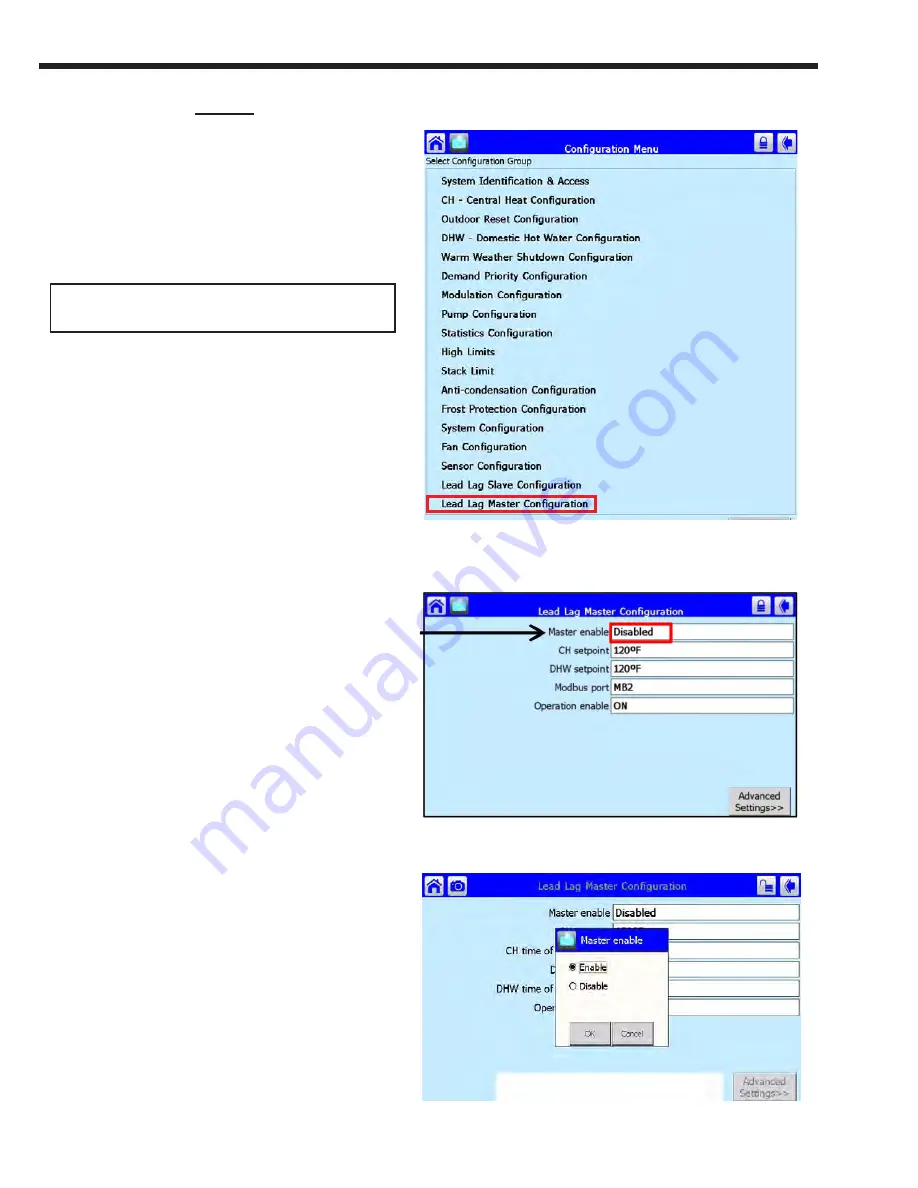
Page 60
B
RADFORD
W
HITE
8.7.18 Lead Lag Leader Configuration
Confirm the Master control is ‘Enabled’.
If not enabled, press to select.
Select Master Control ‘Enable’
and Press OK
Note: The system sensor and outdoor sensor will
need to be wired to the Master boiler only.
The input from these sensors is used by the Master
control to control the modulation rate of all
of the operating boilers it is connected to. See the
manual for sensor and cascade wiring.
When a boiler is operating as part of a Lead Lag
system, it does not use the normal “CH set point” –
it uses the “Lead Lag CH set point” on the Master
control.
It is STRONGLY recommended to start each boiler
to complete combustion set up (See page 64 ) and
perform all safety checks before setting up Lead
Lag cascade.
Wiring Connections for Lead Lag -
The controller in each boiler includes two
wiring terminals for the Modbus system, labeled
“MB1” and “MB2.” MB1 has the wiring
connections to the User Interface display on each
unit, and MB2 is used to communicate with the
other boilers in the Lead Lag system.
For wiring connections to Lead Lag,
see Figure 36 on page 40
To reach the controller, open the cabinet of the
unit. The front panels on the indoor model pop off
when pulled forward. The outdoor model has two
latches that must be released on the sides before
pulling the panel forward and then up and off.
The wiring from the controller on the first
boiler runs to the controller on the next boiler.
Use 22 AWG or thicker shielded twisted-pair wire
with drain. Two twisted pairs or three conductors
are needed. Wire A on MB2 of Boiler 1 must be
connected to A on MB2 of Boiler 2, wire B on
Boiler 1 goes to B on Boiler 2, and wire C on Boiler
1 goes to C on Boiler 2. Repeat this wiring for any
other boilers in the system. Connect all of the drain
wires and ground the drain wire on one end of the
assembly only.
The Configuration Menu
Select ‘Lead Lag Master Configuration’
Summary of Contents for Copper Brute II BWCH 2000
Page 4: ...BRADFORD WHITE...
Page 26: ...Page 22 BRADFORD WHITE 150 285 Figure 23 Minimum Venting Distance...
Page 48: ...Page 44 BRADFORD WHITE Figure 38 Ladder Diagram 7 9 Ladder Diagram...
Page 96: ...Page 92 BRADFORD WHITE Parts Illustration 4 Internal Components Sizes 750 850...
Page 98: ...Page 94 BRADFORD WHITE Parts Illustration 6 Gas Train Components Sizes 600 850...
Page 102: ...Page 98 BRADFORD WHITE Notes...
Page 103: ...Page 99 Brute HIGH EFFICIENCY COMMERCIAL BOILERS AND VOLUME WATER HEATERS Notes...