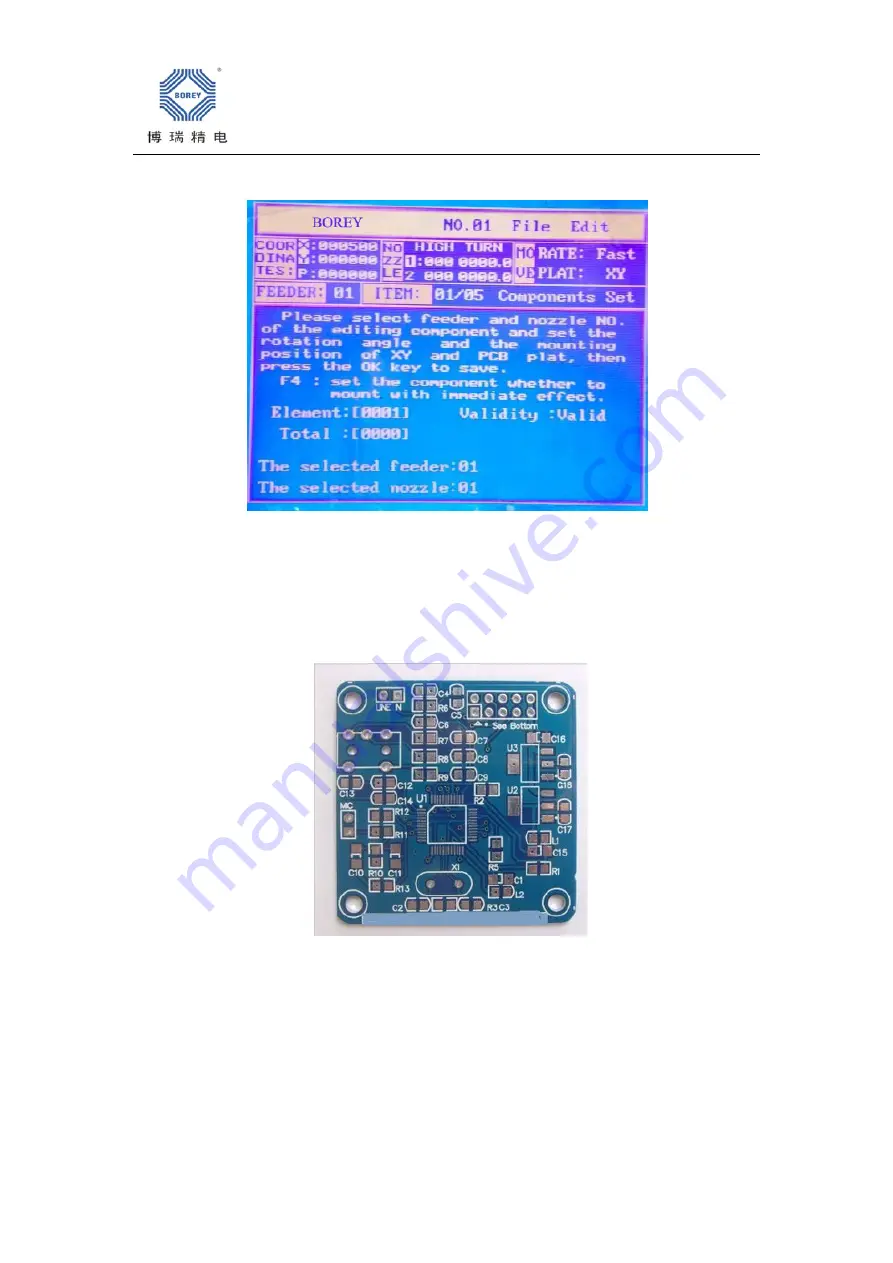
BEI JING BOREY TECH CO., LTD Website:www.en.boreytech.com
As the picture
:
Two different kinds of boards will be set.
1.irregular single board
As the picture:
For this kind of board ,please use camera’s cross and align every soldering pad on
PCB,then set feeder stack,nozzle number and rotating angle,then press Ok to sace.
2.Jointed board,such as LED light board
(
Figure 1
)
The first level array will be used for this kind of board;TH second level array will be
better for longer board.(out of XY axis moving range)