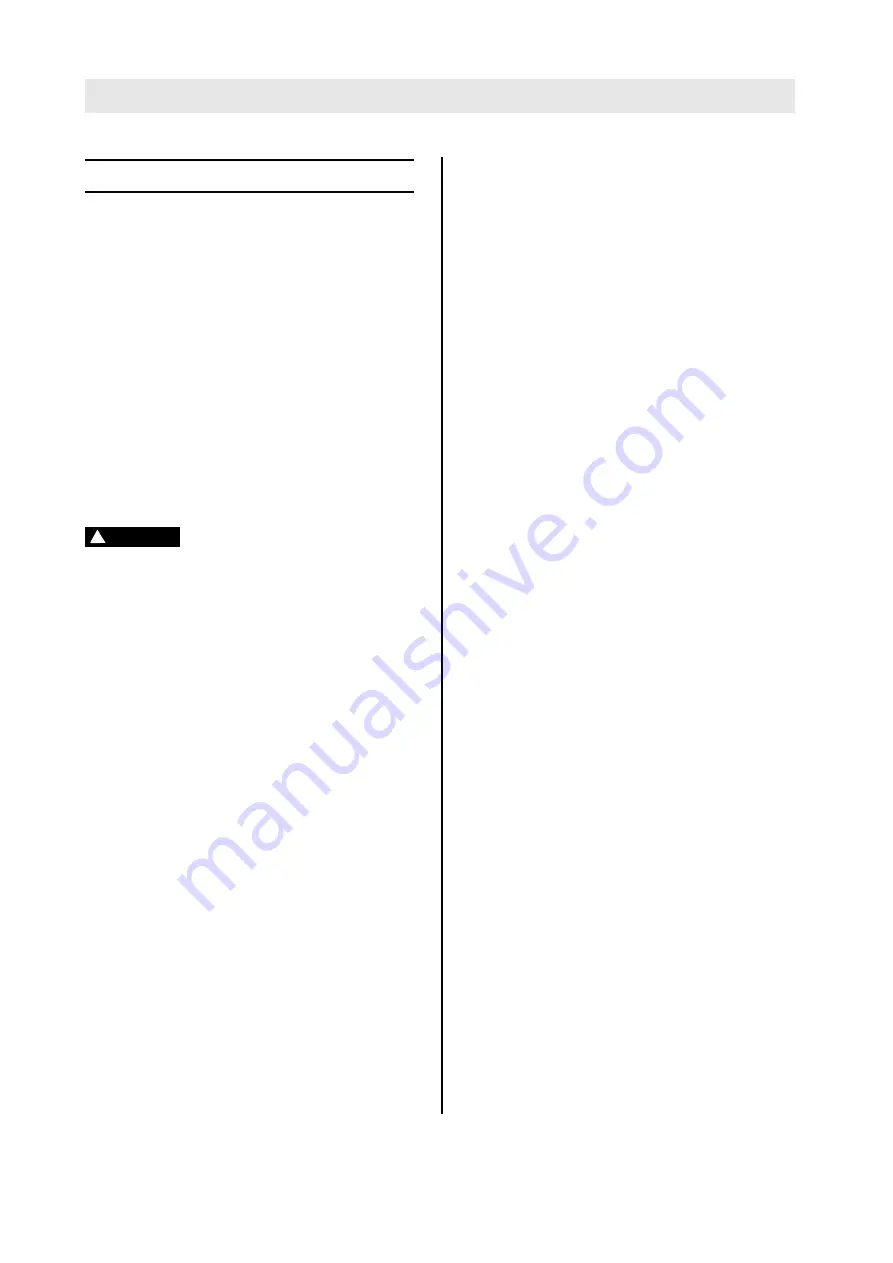
Trouble shooting
BOMAG
96
BW 213 D-4
6.1
General notes
The following work must only be carried out by
qualified and trained personnel or by the sales
service.
Please observe strictly the safety regulations
in chapter 2 of these operating and mainte-
nance instructions.
Faults occur frequently due to the fact, that the
machine has not been properly operated or serv-
iced. Therefore, whenever a fault occurs, read
through these instructions on correct operation
and maintenance. If you cannot locate the cause
of the fault or eliminate it yourself by following the
trouble shooting charts, you should contact our
customer service departments at our branch office
or dealers.
!
Danger
Danger of injury!
Keep away from rotating parts of the engine.
Summary of Contents for BW 213 D-4
Page 2: ......
Page 7: ...BOMAG 7 BW 213 D 4 1 Technical Data...
Page 11: ...BOMAG 11 BW 213 D 4 2 Safety regulations...
Page 18: ...Safety regulations BOMAG 18 BW 213 D 4...
Page 19: ...BOMAG 19 BW 213 D 4 3 Indicators and Controls...
Page 20: ...Indicators and Controls BOMAG 20 BW 213 D 4 Fig 5...
Page 30: ...Indicators and Controls BOMAG 30 BW 213 D 4 Constant end of compaction...
Page 31: ...BOMAG 31 BW 213 D 4 4 Operation...
Page 46: ...Operation BOMAG 46 BW 213 D 4...
Page 47: ...BOMAG 47 BW 213 D 4 5 Maintenance...
Page 95: ...BOMAG 95 BW 213 D 4 6 Trouble shooting...
Page 99: ...Trouble shooting BOMAG 99 BW 213 D 4...
Page 100: ...Trouble shooting BOMAG 100 BW 213 D 4...
Page 101: ......
Page 102: ......