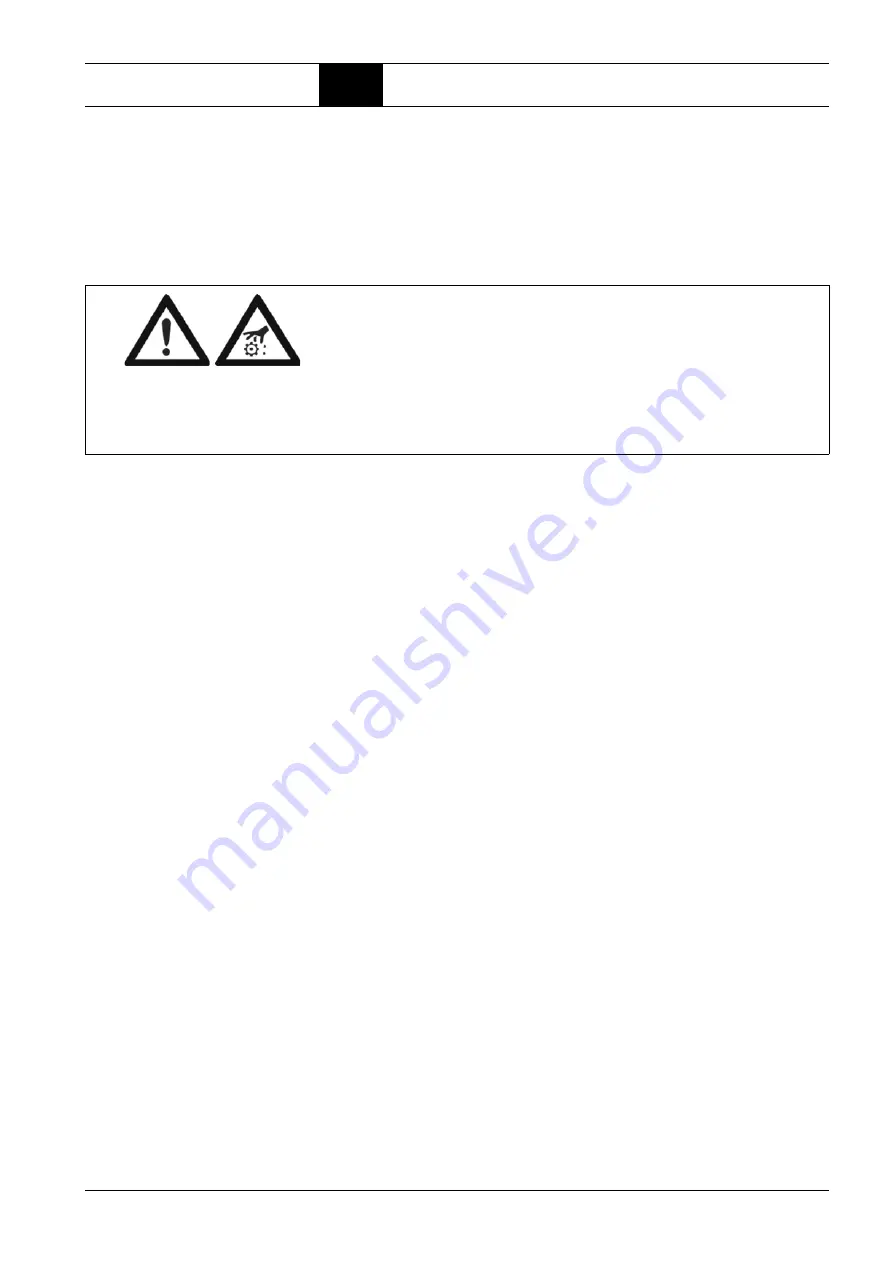
BOGE Operating instructions for C 16 N...C 30 N, C 16 F N...C 30 F N series screw compressors
Page 29
Installation
3.3
Installation
3.3 Installation
General
BOGE compressor units are supplied ready for connection. Only the work
described in the following paragraphs needs to be carried out during the instal-
lation.
–
Please inspect the compressor immediately after delivery and direct dam-
age claims to the last haulier – even when the packing is not damaged!
To safeguard claims against the haulier we recommend leaving the ma-
chine, devices and packing material in the same condition as they were in
when the damage was detected.
–
Prior to commissioning, check the compressor for external damage.
–
Observe the compressor very closely during commissioning and the fol-
lowing trial run.
–
If malfunctions occur, switch off the compressor immediately and inform
the BOGE-Service.
Checking the delivery
scope
The delivery scope depends on your order.
Prior to commissioning, please check whether all required parts have been
provided. Please check the order confirmation for any possible accessory
equipment.
The delivery scope includes the following component parts:
–
Operating instructions
–
Electric circuit diagram (in the compartment of the switch cabinet)
–
List of electrical equipment (in the compartment of the switch cabinet)
–
Oil drainage hose
–
Head nut (in the compartment of the switch cabinet)
–
Spare parts list
Installing the
compressor
–
Remove the packing material on and in the compressor.
–
Install compressor and align horizontally. The compressor must stand
firmly on the ground on all feet.
WARNING!
Only have the installation work carried out by appropriately trained persons
or specialists.
Lay out all energy supply lines in a trip-proof and barrier-free manner so that
potential accidents can be avoided!
Prior to delivery, each compressor is subjected to a trail run at the factory.
It is carefully tested and set. However, possible transport damage cannot
be excluded.