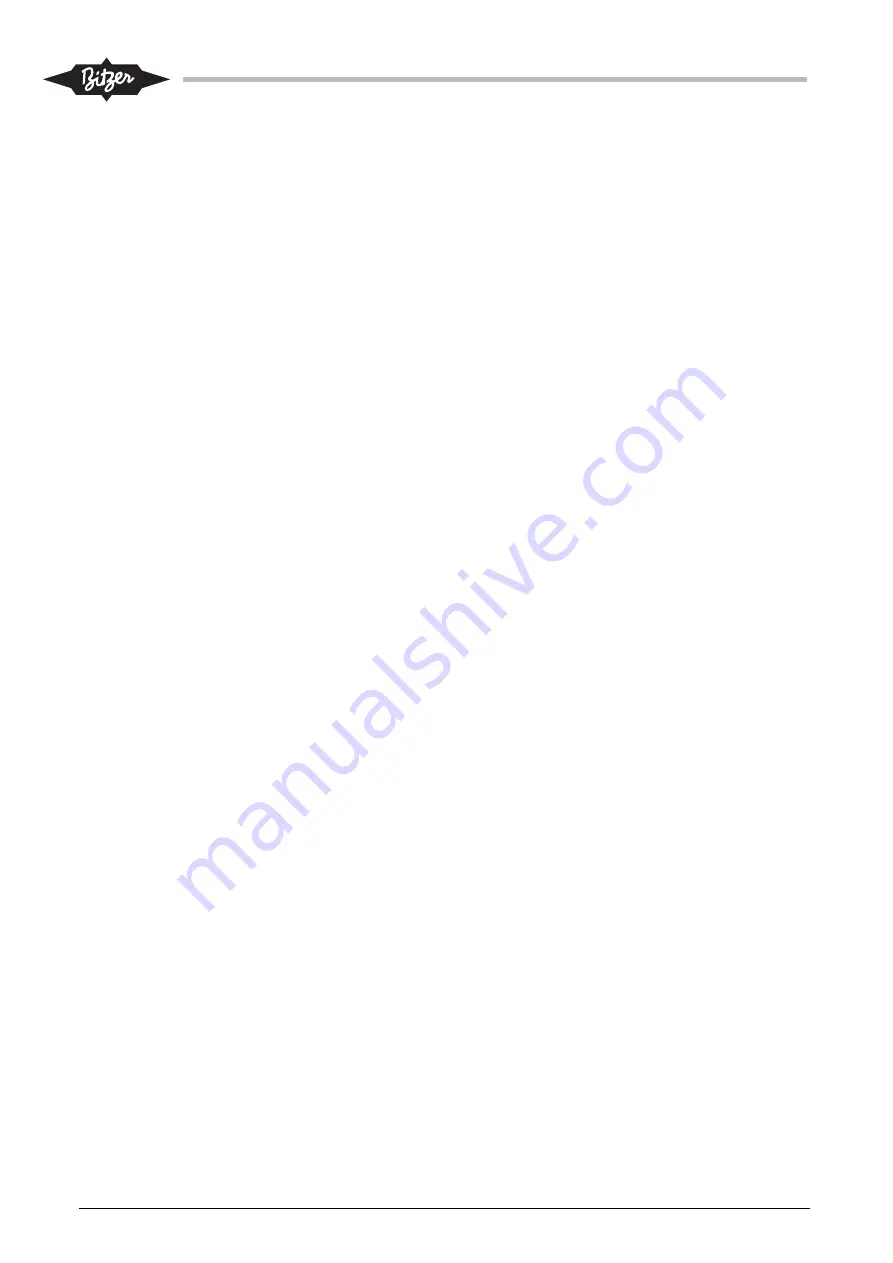
30
CT-600-2
9
Configuration and setup
The BITZER ACP LINK must be configured and setup after the first software installation. Typically this is
already done in the factory. It may also be necessary to configure and setup the parameters of the system,
after firmware or program update.
9.1
Configuration ACP LINK panel, IP addresses and PLC name
If not experienced in using the HMI panel, then first see section 10 on how to operate the ACP LINK panel
HMI.
For the correct communication between ACP LINK PLC and HMI, it is necessary to have a correct setup of
IP addresses and ACP LINK PLC node-name. First, both PLC and HMI must be set up with IP addresses in
the same range. Second, the ACP LINK PLC must have a unique node name (if more than one PLC on the
same network). Finally, the HMI must be setup to look for a PLC with the very node-name of the PLC it shall
communicate with. One can risk to have the HMI communicate with another PLC on the same network if this
is not setup correctly. See section 8.1.3, 8.1.4 and 8.2.3 on how to proceed.
9.2
Configuration ACP LINK, basic setup
The basic configuration, defined by the number and type of compressors, motor and drive types, the optional
equipment (economizer system), etc. must be setup first, to enable communication to the modules. See also
section 10.10 and 10.11 about configuration and parameter settings.
1.
Set the communication setup: Service \ Communication Setup.
Check that the number of available compressors equals the number of compressors on the ACP.
Correct using the +/- button for “Available compressors”.
Check that the electrical panel IO module is selected (IOSP).
Check that the oil system module (OAHC) is selected.
If a BITZER economizer system is connected, then check that the eco system module (ECOSYS) is
selected.
Correct with the corresponding buttons.
2.
Set system nominal frequency: Param. \ Plant page 1.
3.
Set system control voltage for CM: Param. \ Plant page 1.
4.
Set the maximum and minimum speed for VSD compressors: Param. \ Comp./Motor page 1.
Only necessary, if possible speed range is different from default (25 – 60Hz).
5.
Set CM-SW-01 and CM-IO firmware version: Param. \ Comp./Motor page 2.
Assure that the firmware used on all CM-SW-01 and CM-IO modules is as set here.
6.
Set compressor size and type: Param. \ Comp./Motor page 3.1..3
Must match configuration on corresponding compressor module.
7.
Set compressor regulation type: Param. \ Comp./Motor page 3.1..3
Set according to the used regulation type: CR for fixed speed operation and VSD for variable speed
drive.
8.
Set motor current high warning and high alarm: Param. \ Comp./Motor page 3.1..3
Set according to the motor name plate. High warning is set to the maximum motor current on the
motor name plate and high alarm is set 10% above.
Be aware to take into account possible lower limits from the drive or power supply side.