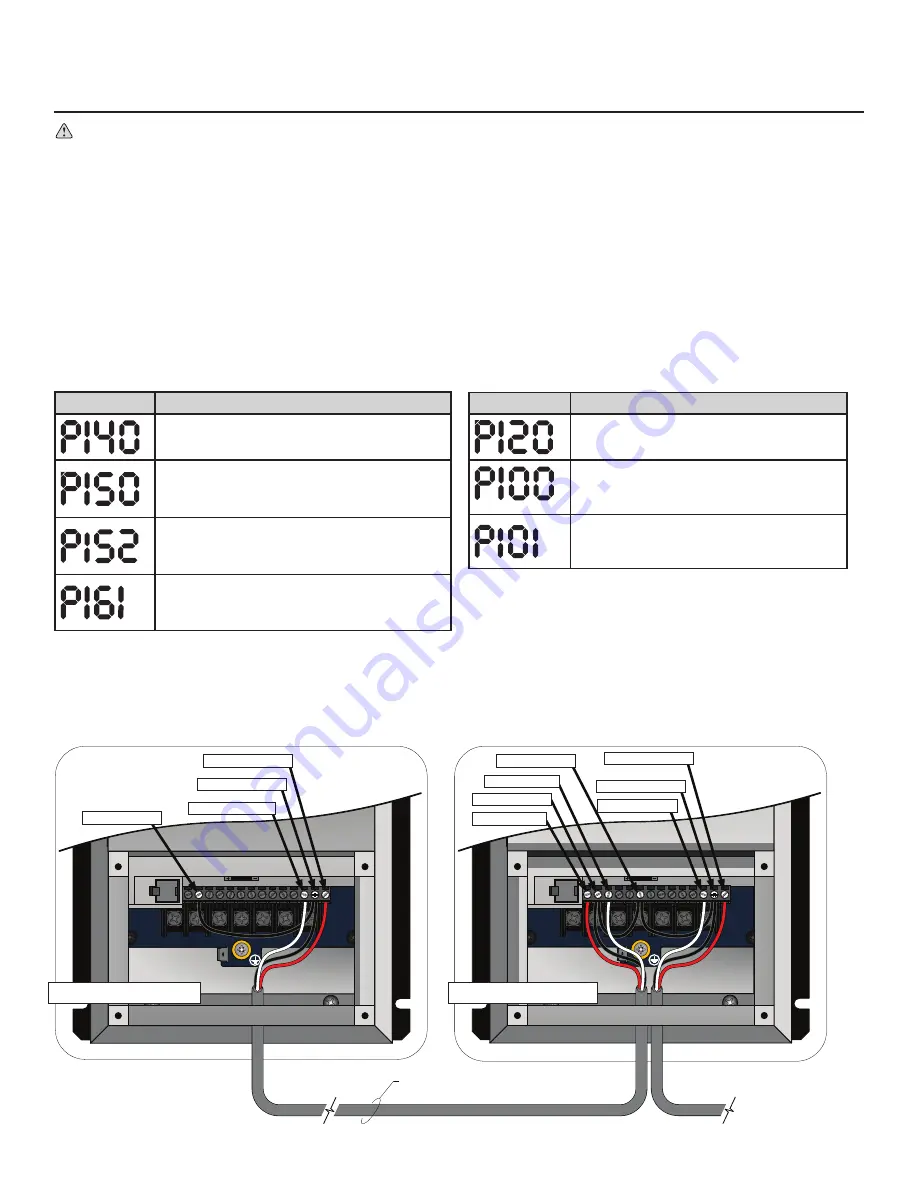
PIVOT™ 180
33
WWW.BIGASSFANS.COM ©2011 DELTA T CORP. ALL RIGHTS RESERVED
PIVOT™ 180
Daisy chaining
WARNING: Wait three minutes after disconnecting before servicing!
The following illustrations and parameter changes enable daisy chaining of the Pivot
™
180 fan speed controller. The first fan provides
a start/stop contact and 0–10VDC analog speed reference for the downstream fan controller. The downstream fan controller provides
a new start/stop contact and 0–10VDC analog speed reference for the following downstream fan controller. This preferred method of
linking the fan controllers together ensures minimal signal loss of command signals in larger multi-fan systems.
Assertion Level Switch (ALSW)
The fan controller ships with the onboard digital I/O configured for Sourcing (PNP) operation. Terminal 4 pr15VDC to be
used as a supply voltage for user-supplied switches and accessories. For this 3-wire daisy chaining application, the downstream fan
controllers must be switched to Sinking (NPN) operation. Terminal 4 will then provide a DC common connection and allow the analog
signal and start stop signal to share that common.
The Assertion Level Switch above terminal 4 must be switched from (+) to ( - )
on all downstream fan controllers for proper daisy chaining operation prior to powerup, parameter changes and operation.
Parameter changes (for first controller)
Parameter
Description
Relay Output Function
Change from “0” for None to “1” for Run.
TB-30 Output
Change from “0” for None to “1” for 0–10VDC
output (scaled to drive output frequency).
TB-30 Scaling Frequency
Change to equal the frequency setting of P103
Maximum Frequency.
Speed at Max Signal
Change to equal the frequency setting of P103
Maximum Frequency.
Note: Depending on the AWG and distance of the low voltage wiring, the downstream fans may run slightly slower than the leading fan.
If this occurs, P161 Speed at Max Signal can be used to introduce a minor command reference overshoot to compensate for the analog
voltage drop. At each downstream fan (beginning with the first downstream fan), adjust the value of P161 up 0.1 to 0.2Hz increments
until the fan’s output frequency matches that of the lead fan.
Electrical Installation (cont.)
Parameter changes (for downstream controllers)
Parameter
Description
Assertion Level
Change from “2” for High to “1” for Low.
Start Control Source
Change from “0” for keypad operation to “1”
for Terminal Strip.
Standard Reference Source
Change from “0” for keypad operation to “1”
for 0–10VDC analog input operation.
U/T1
V/T2
W/T3
PE
L1
L2
L3
1 2 5 6
13A 13B 13C 14
30
16 17
25 4 11
1
2
5 6
13A 13B 13C 14
30 16 17
25 4 11
U/T1
V/T2
W/T3
PE
L1
L2
L3
1 2 5 6
13A 13B 13C 14
30
16 17
25 4 11
1 2 5
6
13A 13B 13C 14
30 16 17
25
4
11
WHITE
BLACK
RED
WHITE
BLACK
RED
WHITE
BLACK
RED
#17 = N.O. Relay Output
#17 = N.O. Relay Output
#16 = N.O. Relay Output
#16 = N.O. Relay Output
#2 = Analog Common
3 conductor shielded cable minimum 20 AWG Stranded
(provided by installer) Recommended Maximum distance = 200 ft
#30 = 0–10 VDC Output
#30 = 0–10 VDC Output
#4 = Digital Common*
0–10 VDC and Start/Stop out
to next downstream controller
#2 = Analog Common
Terminals 2 and 16 shall all be tied together
on the first fan controller.
#1 = Run/Stop Input
#5 = 0–10VDC Input
Terminals 2, 4 and 16 shall all be tied
together on all downstream fan controllers.
Summary of Contents for Pivot 180
Page 1: ...INSTALLATION GUIDE For help call 1 877 BIG FANS or visit www bigassfans com Pivot 180...
Page 46: ......
Page 48: ......
Page 50: ......
Page 59: ......