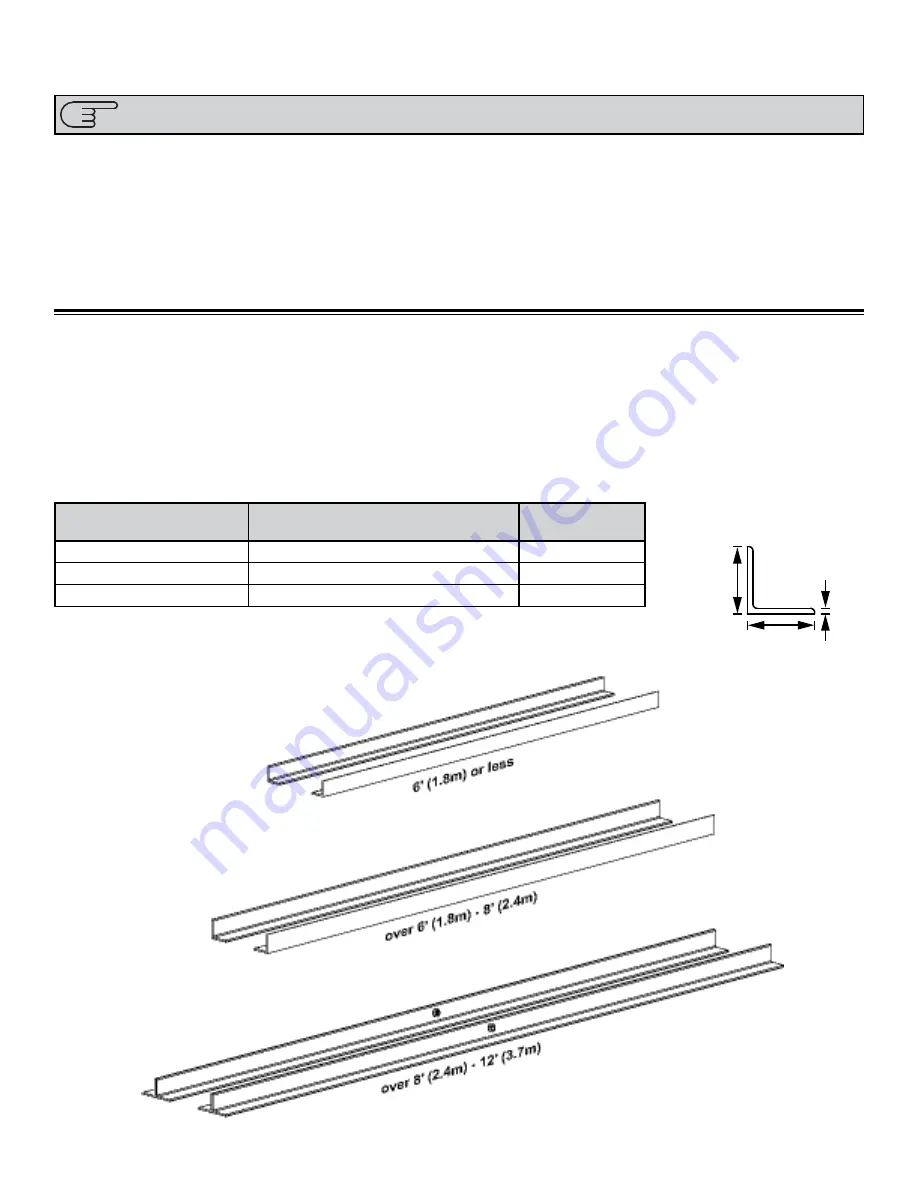
8’ - 24’ POWERFOILPLUS™, POWERFOIL™, & WICKERBILL FANS
WWW.BIGASSFANS.COM ©2010 DELTA T CORP. DBA BIG ASS FAN ALL RIGHTS RESERVED
12
WWW.BIGASSFANS.COM ©2010 DELTA T CORP. DBA BIG ASS FAN ALL RIGHTS RESERVED
8’ - 24’ POWERFOILPLUS™, POWERFOIL™, & WICKERBILL FANS
1. Select Proper Angle Irons
NOTE: Angle irons and angle iron hardware are not included with the fan.
CAUTION: Do not install the fan from a single purlin, truss, or bar joist.
CAUTION: Unsupported angle iron spans should not exceed 12 ft (3.7 m).
Follow the table below when selecting angle irons for fan installation.
Height
Width
Ø 9/16”
(1.4 cm)
Thickness:
1/4” (6 mm)
Angle Iron Side View
(see table for dimensions)
Thickness
Angle Iron Span
(between mounting points)
Minimum Angle Iron Dimensions
(W x H x T)
Number of Angle
Irons Needed
6 ft (1.8 m) or less
2.5” (6.4 cm) x 2.5” (6.4 cm) x .25” (0.6 cm)
2
over 6 ft (1.8 m)-8 ft (2.4 m)
3” (7.6 cm) x 3” (7.6 cm) x .25” (0.6 cm)
2
over 8 ft (2.4 m)-12 ft (3.7 m)
3” (7.6 cm) x 3” (7.6 cm) x .25” (0.6 cm)
4*
*2 pairs of angle irons. Pairs should be placed back to back and fastened in center (see step 2).
Mounting Method 2: Angle Irons
If you are installing the fan to an I-beam and have attached the upper yoke (p. 11), proceed to “Hanging the Fan”
(p. 18).
WARNING: The fan should not be installed unless the structure on which the fan is to be mounted is of sound construction,
undamaged, and capable of supporting the loads of the fan and the method of attachment to the structure. A structural
engineer should verify that the structure is adequate prior to fan installation. Verifying the stability of the mounting structure
is the sole responsibility of the customer and/or end user, and Big Ass Fans hereby expressly disclaims any liability arising
therefrom, or arising from the use of any materials or hardware other than those supplied by Big Ass Fans or otherwise
specified in these installation instructions.
WARNING: Never use beam clamps when mounting the fan to angle irons! Beam clamps are only intended for I-beam
installations.