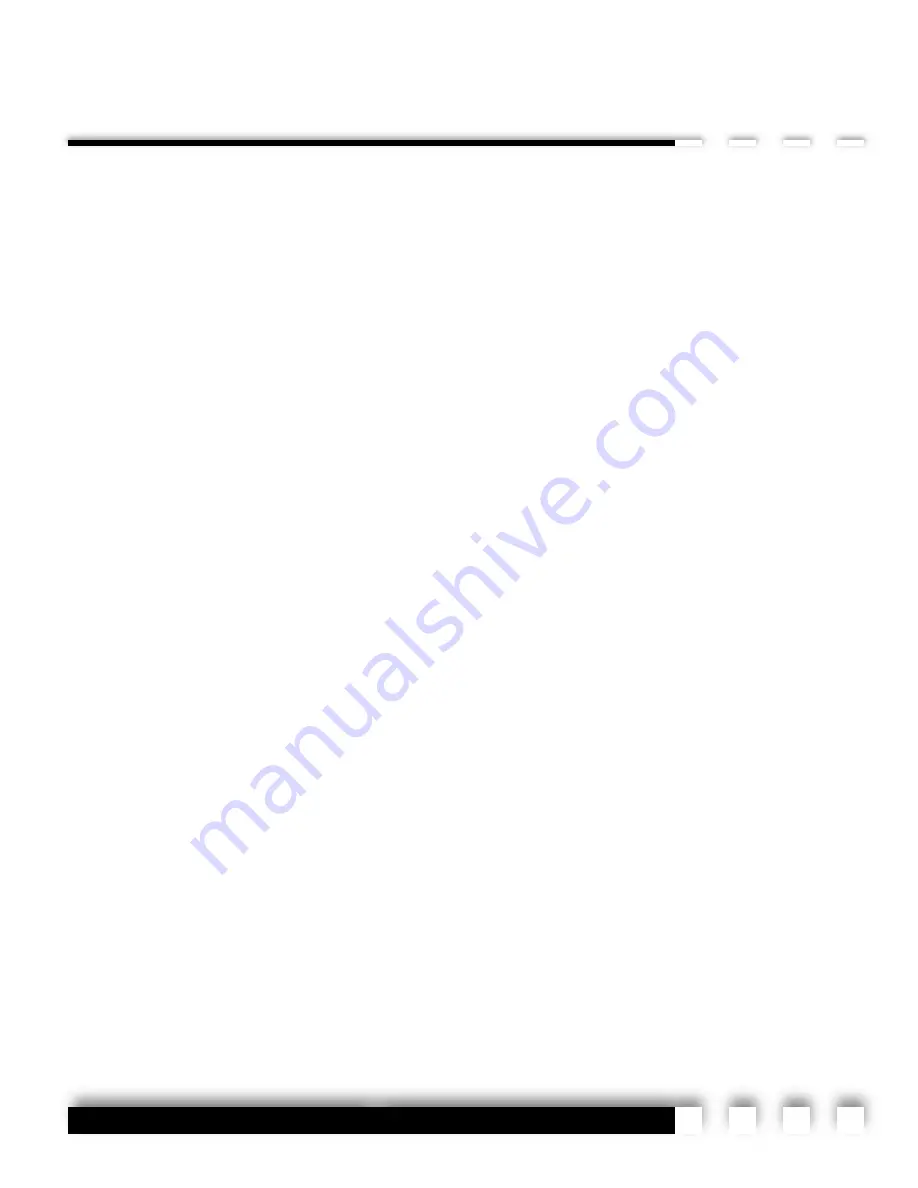
Except as set forth above,
Bestway shall have no obligation or liability of any kind on
account of its equipment and shall not be liable for special or consequential damages.
Bestway makes no other warranty, expressed or implied, and, specifically, Bestway disclaims
any implied warranty or merchantability or fitness for a particular purpose. Some states or
provinces do not permit limitations or exclusions of implied warranties or incidental or conse-
quential damages, so the limitations or exclusion in this warranty may not apply.
This warranty is subject to any existing conditions of supply, which may directly affect our
ability to obtain materials or manufacture replacement parts.
Bestway reserves the right to make improvements in design or changes in specifications at any
time, without incurring any obligation to owners of units previously sold.
No one is authorized to alter, modify or enlarge this warranty nor the exclusions, limitations
and reservations.
A7
Summary of Contents for Field-Pro IV 1200
Page 9: ...A8 SPECIFICATIONS ...
Page 11: ...A10 A C D E G P N 67657 A P N DEC HAZ01 A Safety Sign Locations B C F P N DEC HAZ08 A ...
Page 19: ...B6 ...
Page 29: ...C10 Raven 450 Spray Wiring Diagram ...
Page 32: ...C13 Raven 440 Spray Wiring Diagram ...
Page 50: ...E3 50 Hours 12 Hours 2 places 12 Hours 2 places 12 Hours Grease Zerk Locations ...
Page 64: ...G1 PARTS LISTING ...
Page 69: ...G6 ...
Page 70: ...G7 BASE PLUMBING ...
Page 72: ...G9 Pro 60 Boom ...
Page 73: ...G10 ...
Page 78: ...G15 Pro 80 Boom ...
Page 79: ...G16 ...
Page 84: ...G21 Pro 60 Boom Hydraulic Schematic ...
Page 86: ...G23 Pro 80 Boom Hydraulic Schematic ...
Page 88: ...G25 Pro 60 plumbing ...
Page 90: ...G27 Pro80 Boom Plumbing ...
Page 94: ...G31 ...
Page 96: ...G33 Foam Guidance system Model 6 or 10 ...
Page 100: ...G37 Rinse Assembly ...
Page 102: ...G39 Deluxe Plumbing with 4 Valve Stack Assembly ...
Page 104: ...G41 Deluxe Plumbing with 3 Valve Stack Assembly ...
Page 106: ...H1 Field Pro IV 1200 Base Wiring Details ...
Page 108: ...H3 ...