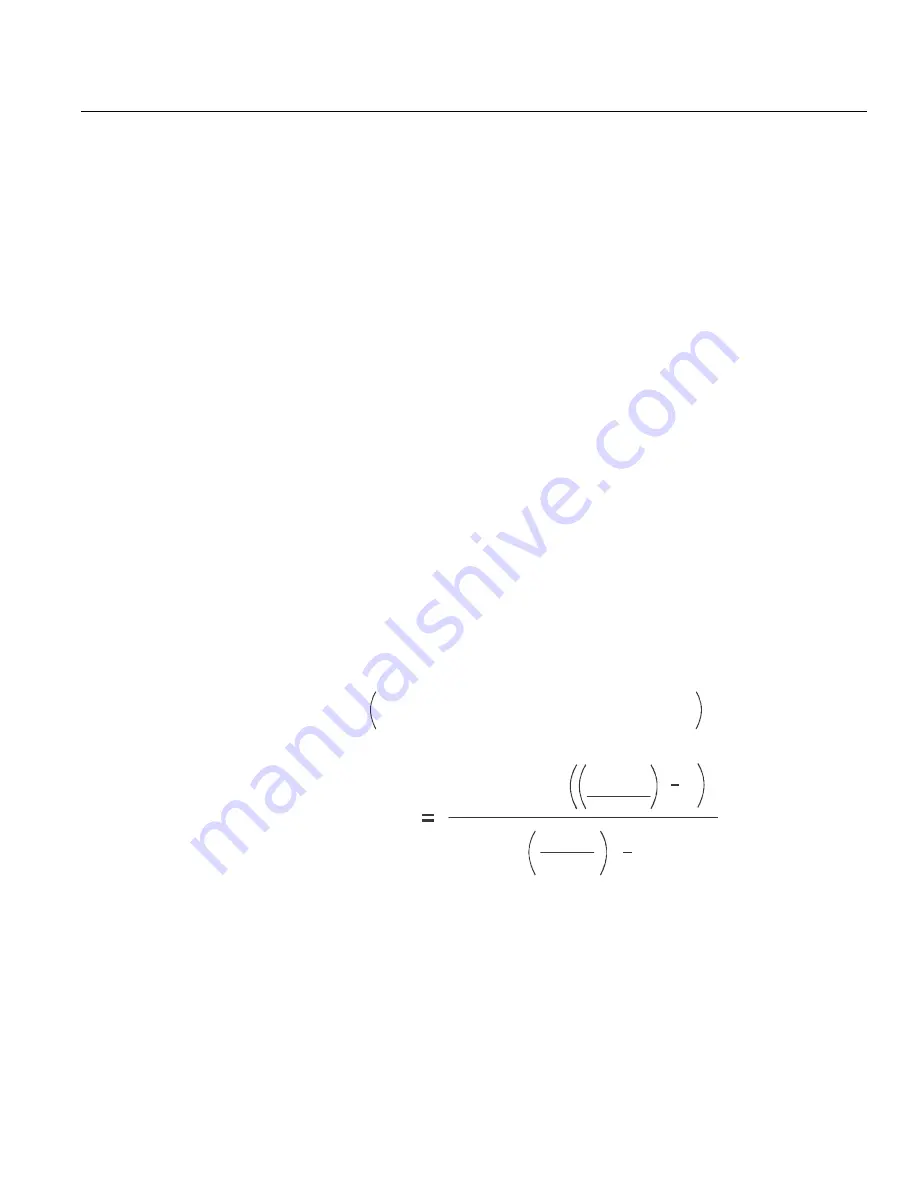
M2L 3000 Series VFD
78
FUNCTION-06 (40156)
Coast to Brake Time
Value: 0.1 – 10.0 Seconds Default: 0.1
When
the Stop Mode
(FUNCTION-01) is set to “Coast then DC Brake”,
Coast to Brake
Time
allows for a programmed delay, in which the motor coasts, between pressing
“STOP” and the DC Brake being applied. This allows the magnetic field in the motor to
decay before applying the brake.
FUNCTION-07 (40157)
Stopping Brake Time
Value: 0.1 – 300.0 Seonds Default: 0.1
When the
Stop Mode
(FUNCTION-01) is set to “Coast then DC Brake” or “Decel then
DC Brake”, the Stopping Brake Time determines how long the system will apply the DC
Brake. The amount of braking is determined by the
Stopping Brake Level
(FUNCTION-
08).
FUNCTION-08 (40158)
Stopping Brake Level
Value: 1 – 100%
Default: 1
When
Stop Mode
(FUNCTION-01) is set to “Coast then DC Brake” or “Decel then DC
Brake”, the Stopping Brake Level determines how much current the DC Brake will ap-
ply. This value represents a percentage of the
Motor Rated Current
(DRIVE-01), the
duration of which is determined by the
Stopping Brake Time
(FUNCTION-07).
FUNCTION-09 (40159)
Decel to Brake Frequency
Value: 0.10 – 300.00 Hertz Default: 20.0
When the
Stop Mode
(FUNCTION-01) is set to “Decel then DC Brake”, the Decel to
Brake Frequency determines the frequency at which, after following the
Deceleration
Profile
(DRIVE-15), DC current is applied to brake the motor.
FUNCTION-10 (40071)
Motor Thermal Overload
Enable
Value: 0 Disabled
1: Enabled
Default: Enabled
The motor overload function enables protection of the motor from thermal breakdown of
the insulation and windings. When enabled, the drive will trip when the output current
persists over the value programmed in
Motor OL Level
(FUNCTION-11), for a duration
longer than that programmed in
Motor OL Time
(FUNCTION-12).
if
Actual
Motor Current
Service Factor
[FUNCTION-14]
X
Rated Current
[DRIVE-01]
then
Overload
Trip Time
at Given
Current
(in sec.)
Motor Thermal
Overload Time
[FUNCTION-12]
Motor Thermal
Overload Level
[FUNCTION-11]
2
100%
X
1
Actual
Motor Current
2
1
Rated Current
[DRIVE-01]
NOTE
: Do not rely on the drive for motor overload protection when the drive is
used in a synchronous transfer application. The drive cannot monitor motor current
when the motor is transferred across the line.
Summary of Contents for M2L 3000
Page 2: ...M2L 3000 Series VFD 2...
Page 6: ...M2L 3000 Series VFD 6...
Page 10: ...M2L 3000 Series VFD 10...
Page 14: ...M2L 3000 Series VFD 14 Part Number Definitions UL Applicable Base Part Numbers...
Page 16: ...M2L 3000 Series VFD 16...
Page 27: ...3 Installation 27 Wiring Schematics Figure 1 MV Drive System Layout...
Page 28: ...M2L 3000 Series VFD 28 Figure 2 Converter Power and Control Circuit Portions...
Page 29: ...3 Installation 29 Figure 3 Inverter Power and Control Circuit Portions...
Page 40: ...M2L 3000 Series VFD 40...
Page 72: ...M2L 3000 Series VFD 72...
Page 124: ...M2L 3000 Series VFD 124...
Page 126: ...M2L 3000 Series VFD 126...
Page 127: ...References 127 References Placeholder for text with left side label...
Page 128: ...M2L 3000 Series VFD 128...
Page 132: ...M2L 3000 Series VFD 132...