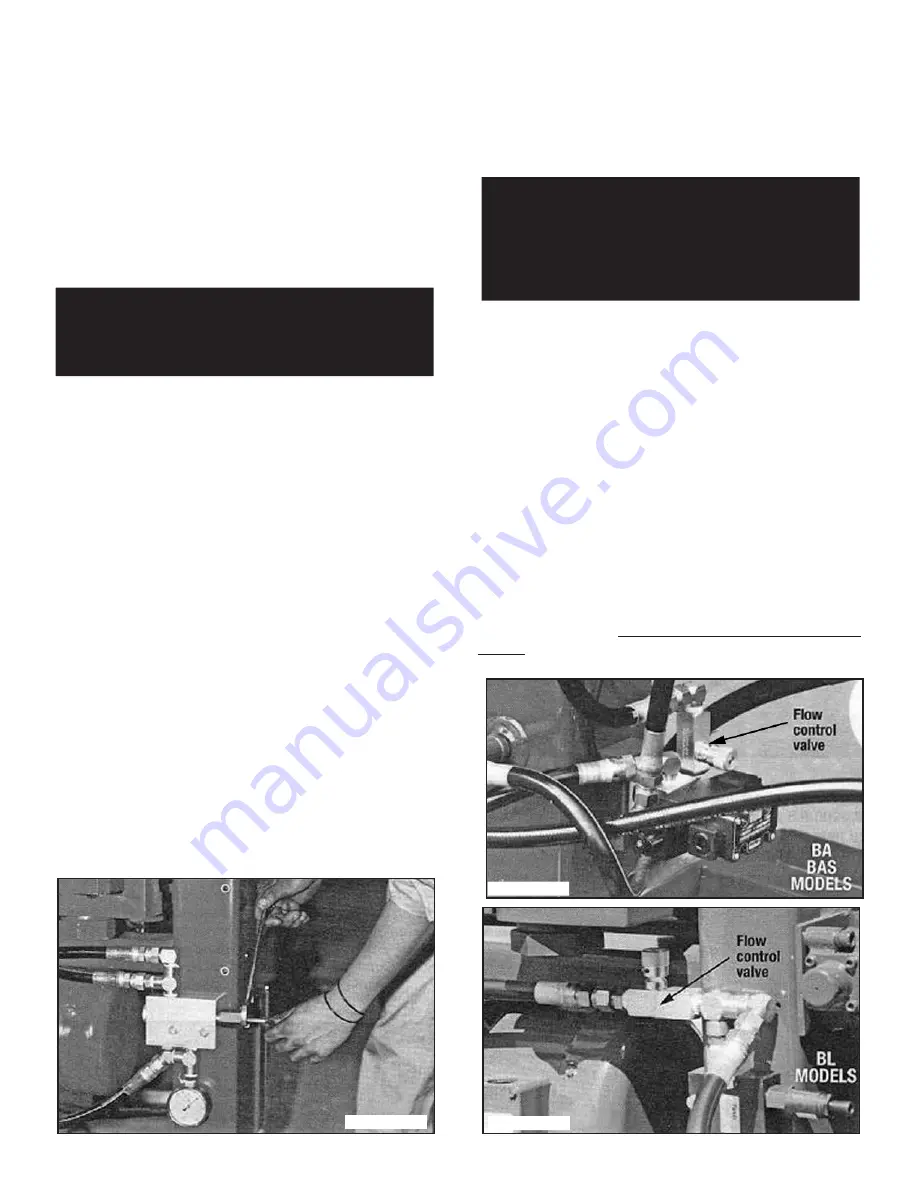
NOTE:
Loose hoses and Hydraulic Components will not always
show a visual sign of leakage, however even small leaks
can allow air into the system. It is very important to
tighten all hoses and mounting bolts on Hydraulic
Components monthly.
PRESSURE SETTINGS
There are three critical pressure settings on your Bender
that affect its performance These pressures should be
checked weekly. The following is a brief description of
the pressures and the roles they play.
BACK PRESSURE
Back pressure is actually resistance pressure applied to
the Back Gates during the bending process. The
pressure is transferred to the Back Gates via the Bottom
Cylinder and Chain Assembly. The setting itself is
controlled by the Sequence Valve. This “resistance”
pressure is required in order to form the shape of the
Tubing as the Radius Die advances. This pressure is
read on the Gauge attached to the Sequence Valve
located near the front left side of the machine. The
pressure reading is taken as the Dies advance through
the Gates during a bend.
The normal operating back
pressure should be set at 1600 P.S.l.
In some cases it
may be necessary to adjust this
pressure. (See Three Inch and Stainless Bending
Procedures found on pages 21 & 22.)
If the back pressure needs adjusting, proceed as follows:
1. Turn the machine on.
2. Place a Radius Die and set of Back Shoes in position.
Tubing will not be required for this operation.
3. Advance the Radius Die until it begins to pass through
the Gates.
4. At this time read the pressure shown on the Gauge
attached to the Sequence Valve. (See figure 3-B)
5. If an adjustment is required, loosen the locking nut
that secures the adjusting screw.
6. To increase the pressure, turn the adjusting screw
clockwise; to decrease, counterclockwise. Never
exceed 2000 P.S.I.
RETURN PRESSURE
This pressure reading is also taken on the gauge located
near the front left side of the machine. The purpose of this
pressure is to maintain adequate tension on the chain
assemblies during the retract sequence. This is important
so that the Gates close in unison with the Radius Die.
Upon initiating the return sequence, Hydraulic Oil is “split”
and redirected, so that an equal portion is transferred to
the Top Cylinder and Bottom Cylinder simultaneously. If
the pressure is set too high, the machine will groan and
strain when reversing as the Top Cylinder tries to overcome
the Bottom Cylinder. If the pressure is too low, the Gates
may hesitate or remain open when the Radius Die retracts
as the Top Cylinder receives more Oil than the Bottom
Cylinder. It is seldom necessary to readjust this pressure
setting.
The normal operating return pressure should
be set at 350 P.S.l.
This pressure reading is taken as the
Radius Die retracts
just after it releases from the Back
Shoes.
This pressure setting is controlled by the flow
Control Valve. (See figure 1-A and 2-A)
CAUTION!
Never exceed 2000 P.S.I. for the back pressure
unless specifically instructed to do so by the
factory for special circumstances. If it is necessary
to increase the back pressure, always remember to
return the pressure back to 1600 P.S.I. before
proceeding with the next bend.
CAUTION!
Improper back pressure settings will cause Tubing
to wrinkle and/or collapse and may also damage
machine and/or Dies.
Figure 1-A
Figure 2-A
Figure 3-B
34 Bender Operation Manual
Summary of Contents for BB 1302-BA
Page 50: ...50 Bender Operation Manual...
Page 51: ...Bender Operation Manual 51...
Page 56: ...56 Bender Operation Manual...
Page 57: ...Bender Operation Manual 57...
Page 58: ...58 Bender Operation Manual...
Page 59: ...Bender Operation Manual 59...
Page 60: ...60 Bender Operation Manual...
Page 61: ...Bender Operation Manual 61...
Page 62: ...62 Bender Operation Manual...
Page 63: ...Bender Operation Manual 63...
Page 64: ...64 Bender Operation Manual...
Page 65: ...Bender Operation Manual 65...