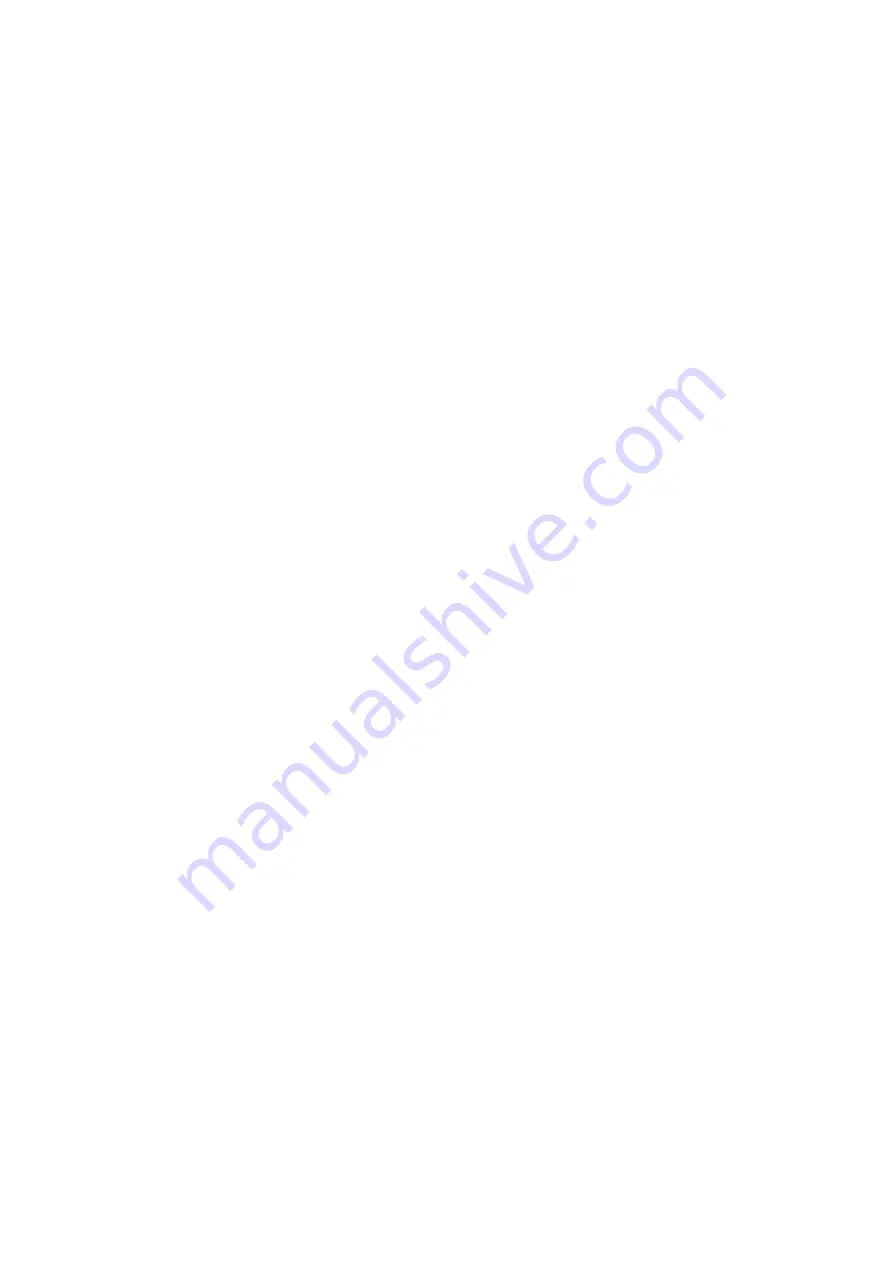
7. CONFIGURATION EXAMPLE
In this example a BA314NG Tachometer is connected
to a proximity detector producing 105 pulses per
revolution.
The BA314NG is required to display rotational speed
in RPM with a resolution of one RPM. The run-time
clock is to operate when the shaft speed exceeds
5 RPM. The display is to be updated twice per
second.
For this application the operator needs to reset the
run-time display to zero from the display mode, but
should not be able to reset the grand total run-time
from the display mode. To prevent tampering the
instrument configuration menu is to be protected by
security code of 1209.
7.1 Configuration procedure
The BA314NG Tachometer may be configured on-site
without disconnection from the power supply or from
the proximity detector.
Step 1
Enter the configuration menu
Enter the configuration menu by
simultaneously pressing
(
and
)
.
Assuming a security code has not already
been entered the instrument will respond
by displaying
inPut
which is the first
function in the configuration menu. See
Fig 10.
Step 2
Select the type of input & debounce
With
inPut
displayed press
(
which will
reveal the sub-menu. Using the
&
or
*
button select
inP
.
tYPE
and press
(
to
reveal the current input. The Tachometer
is required to work with a proximity
detector so again using the
&
or
*
button select
Pr.
dEt
followed by
)
to
return to the
inP
.
tYPE
prompt in the sub-
menu.
Using the
&
or
*
button select
dEbouncE
from the sub-menu and press
(
. Using the
&
or
*
button select
dEFAuLt
which will provide moderate pulse
edge noise protection. If the Tachometer
is subsequently found to miscount the
noise rejection can be increased. Enter
the selection and return to the
inPut
prompt in the configuration menu by
pressing the
)
button twice.
See 6.4, 6.5 and 6.6
Step 3
Select the interval between display
updates
Using the
&
or
*
button select
uPdAtE
in the configuration menu and press
(
to
reveal how frequently the Tachometer
display is updated.
Using the
&
or
*
push button select
0
.
5
(0.5 seconds i.e. 2 display updates
per second). Enter the selection and
return to the
uPdAtE
prompt in the
configuration menu by pressing the
)
button.
See 6.7
Step 4
Run-time display
Using the
&
or
*
button select
di5P-2
in the configuration menu and press
(
to select if the run-time display is
on
or
oFF
. The Tachometer is required to
display run-time therefore using the
&
or
*
button select
on
and press
)
to
enter the selection and return to the
di5P-2
prompt in the configuration menu.
See 6.8
Step 5
Position of decimal point in speed
display.
Select
dP
from the configuration menu
and press
(
. The speed display will be
activated and identified by the Rate
annunciator. Using the
&
or
*
push
button position the decimal point to the
right of the least significant digit to give a
total display resolution of 1.
Finally press the
)
button to enter the
selection and return to the
dP
prompt in
the configuration menu.
See 6.9
Step 6
Enter the speed scale factor
5CALE.5
is a dividing factor adjustable
between 0.0001 and 99999 that enables
the Tachometer to display speed in the
required engineering units. The speed
display timebase is determined by
t-bA5E
that is adjusted in Step 7.
In this example the Tachometer speed
display is required in revolutions per
minute. The proximity detector produces
105 pulses per revolution therefore
5CALE
.
5
should therefore be adjusted to
105.0.
Using the
&
or
*
push button select
5CALE.5
from the configuration menu
and press
(
to reveal the existing value
with one digit flashing. This should be
changed to 105.0 using the
&
or
*
push button to adjust the flashing digit
and the
(
button to transfer control to
the next digit and to position the decimal
point. Finally, enter the new value and
return to the
5CALE
.
5
prompt in the
configuration menu by pressing
)
.
See 6.10
25
Summary of Contents for BA314NG
Page 1: ...Issue 5 9th July 2019 BA314NG Ex nA and Ex tc Tachometer Issue 5...
Page 16: ...16...
Page 17: ...17...