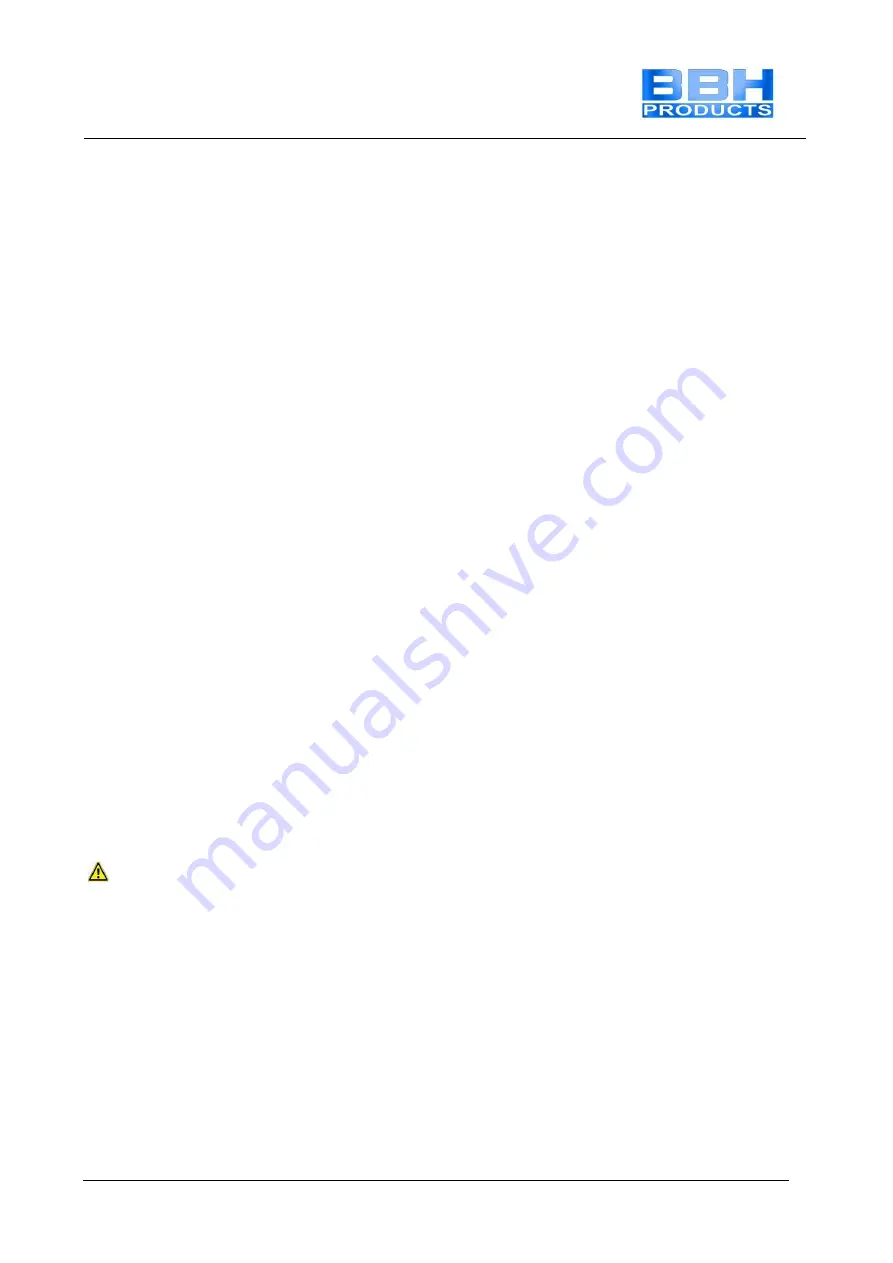
Installation manual
HB-37420-810-01-25F-EN SMX100 Installation manual.docx
Page 191 of 260
Version: 25F
5.11 Connection of position and speed sensors
5.11.1 General notes
Depending on the module type, SMX100 axis expansion module (SMX1xx(/2) has external
encoder interface to connection conventional incremental and absolute encoders. The encoder
interfaces can be configured as incremental, SIN/COS, absolute SSI encoder or as Proxy.
It is also possible to connect 2 incremental signal generating sensors (e.g. proximity switches)
to the counting inputs of the SMX100 module. The signals must each be read in with normal
and complementary track.
IMPORTANT
The voltage supply of the encoder system uses the dedicated terminals on the SMX100
module. This voltage is applied to the encoder plug and monitored by an internal diagnostic
process.
When the sensor is supplied with an external voltage, this voltage must be supplied through the
encoder plug. The corresponding terminal (encoder supply voltage) on the SMX100 module
remains unoccupied.
If an external sensor voltage supply is not recirculated through the encoder plug, any failure of
this supply must be included in the fault examination of the overall system. This, in particular,
requires evidence that this fault is detected or can be excluded when the specified operating
voltage of the overall system is fallen short of / exceeded.
EMC - measures such as shielding etc. must be observed.
The two encoders must be non-interacting to each other. This applies for both the electrical as
well as the mechanical part.
If both encoders are coupled to the facility to be monitored via common mechanical parts, the
connection must be positively designed and should not have any parts that are susceptible to
wear (chains, toothed belts, etc.). Should this be the case, additional monitoring features for the
mechanical connection of the sensors (e.g. monitoring of a toothed belt) are required).
In case of an active position processing at least one absolute value encoder must be used.
When using two equivalent sensors one must make sure that the sensor with the higher
resolution is configured as sensor 1 (process sensor) and the sensor with the lower resolution
as sensor 2 (reference sensor).
Safety note:
•
The GND connections of the encoders must be connected to the GND of the SMX.
This applies in the same way also to resolvers.
Attention:
The sensor connections must neither be plugged on nor pulled off during operation. This could
cause damage to electrical components of the encoder. Always de-energize connected
encoders and the SMX100 module
before
plugging on or pulling off encoder connections.
For the data and Clock signals, track A and track B or Sin/Cos, lines twisted in pairs are to be
used for the signal transmission acc. to RS485 standard. The wire cross-section must in each
individual case be chosen in compliance with the current consumption of the encoder and the
cable length required for the installation.