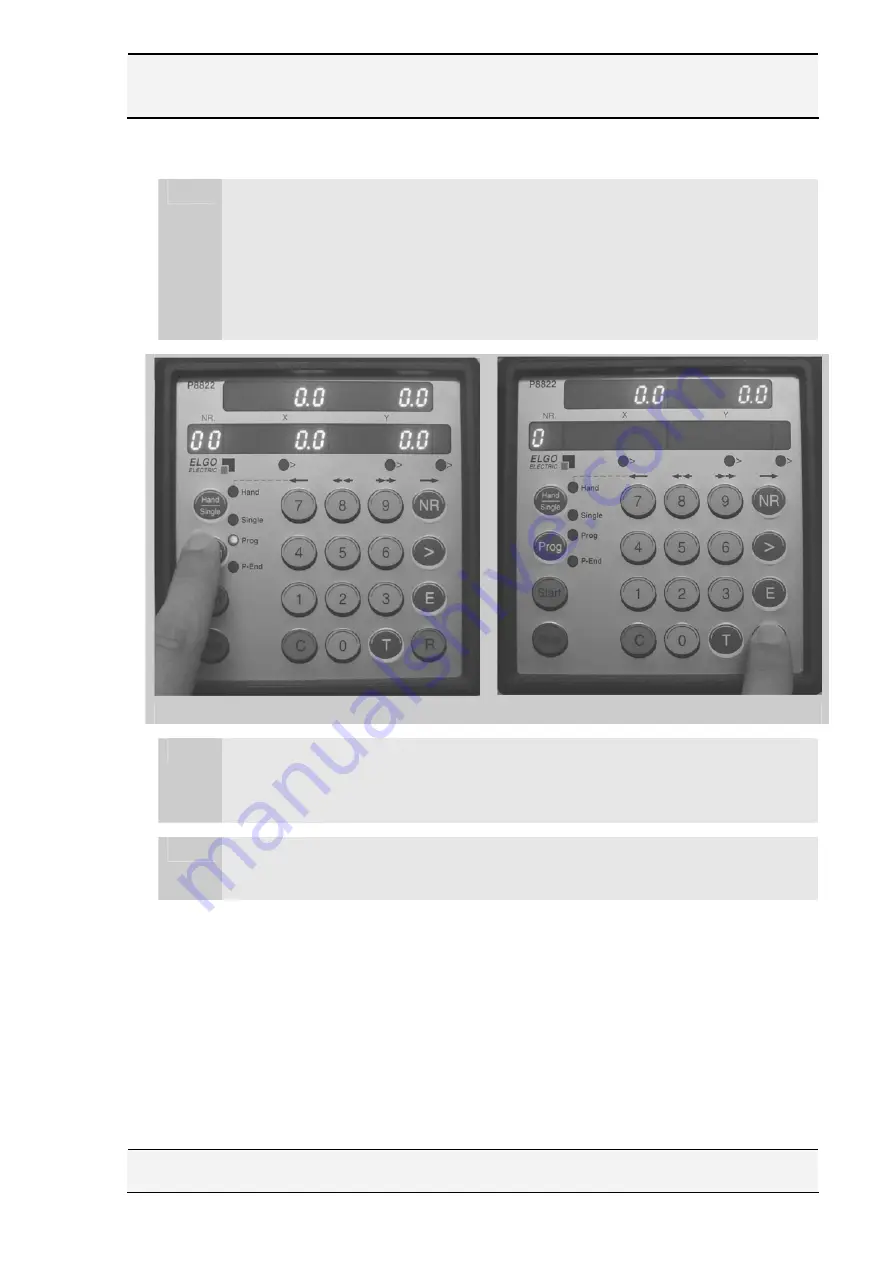
BAYKAL
EDITION NO :
APH
SECTION :
DATE OF ISSUE :
July-2005
PAGE :
43
3.
Program mode
When you select the program mode in the controller, you can bend sheet metals
according to the program you write before. To work with program, first you
should select program mode;
1.
Press Prog key on the controller
(See Figure 6.5.3.16)
. The small led
(Prog. Led) will light up. A new program can be selected by means of
Register R40. The values of digits in register R40 are 0 to 99 i.e. value
"0" is the number 1 program.
Figure 6.5.3.16
Figure 6.5.3.17
2.
In this step, you should select program number. To select program
number, press R key
(See Figure 6.5.3.17)
on the controller. (If you are
editing a program, press T key to resets windows to zero.) NR window
begins flashing.
3.
Enter 40
(See Figure 6.5.3.18)
using numerical keys and press Cursor
key
(See Figure 6.5.3.19)
.
You will see existing program number in X widow.
Summary of Contents for APH Series
Page 17: ...BAYKAL EDITION NO APH SECTION DATE OF ISSUE July 2005 PAGE 17 Figure 5 1...
Page 90: ...BAYKAL EDITION NO APH SECTION DATE OF ISSUE July 2005 PAGE 90 APPENDIX A SPARE PART LIST...
Page 91: ...BAYKAL EDITION NO APH SECTION DATE OF ISSUE July 2005 PAGE 91 B HYDRAULIC CIRCUIT DIAGRAM...
Page 92: ...BAYKAL EDITION NO APH SECTION DATE OF ISSUE July 2005 PAGE 92 C ELECTRIC CIRCUIT DIAGRAM...
Page 93: ...BAYKAL EDITION NO APH SECTION DATE OF ISSUE July 2005 PAGE 93 ADDITIONAL MANUALS...