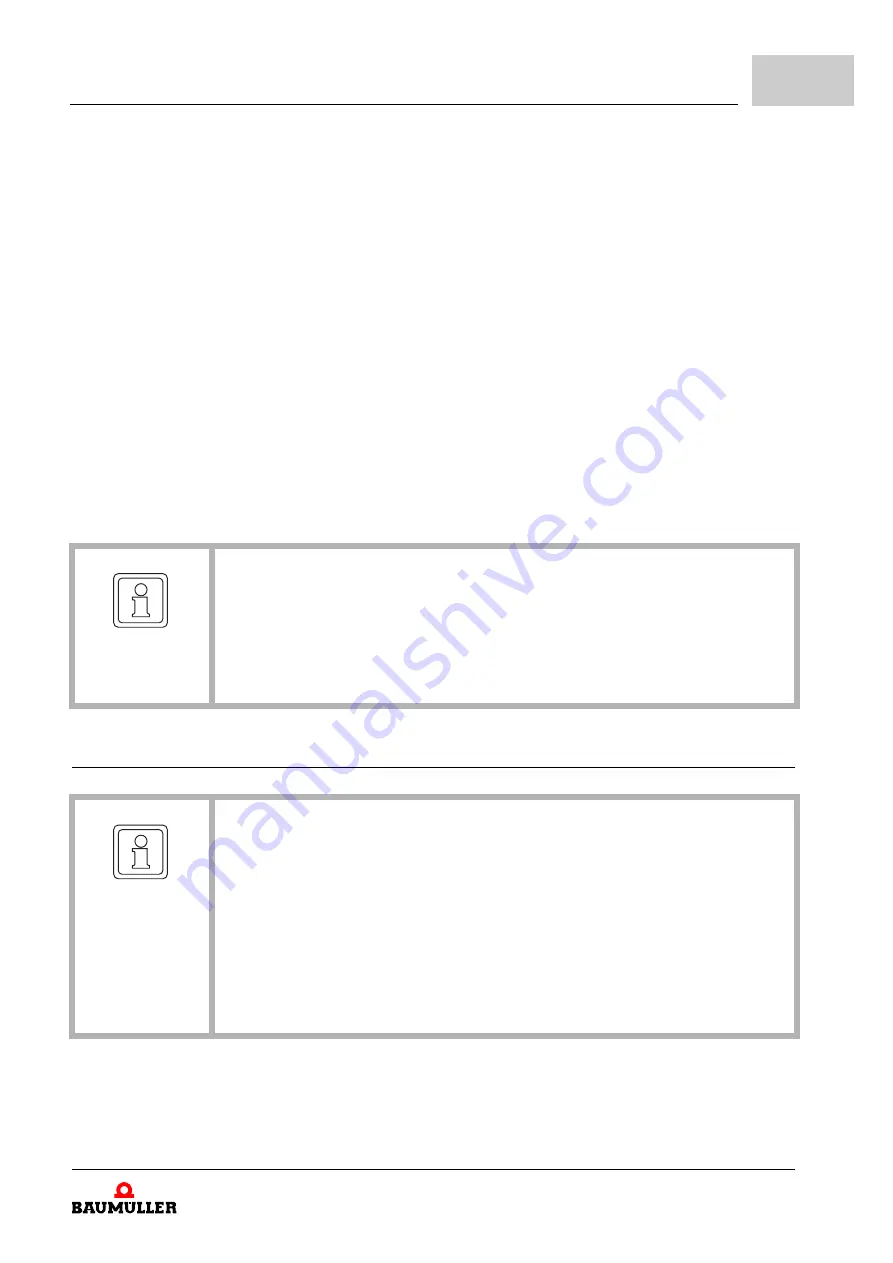
Commissioning
Operation Manual
b maXX safe PLC
BMC-M-SAF-02
Document no.: 5.07020.04
75
11
The entry process can be repeated once if an incorrect code has been entered. The re-
peat entry is activated by briefly pushing the S1 button on the CF module and the S1 but-
ton on channel 2 of the PLC simultaneously. If the second code entry is also incorrect, it
will not be possible to enter the code again. The code entry process can only be conduct-
ed again after turning the safely control off and then on again.
If the correct code has been entered, the project will be copied from the CF module to the
control. The yelllow LED H3 will light up in the process.
When the copying process has ended, the yellow LED H3 will go out and the control goes
into “STOP” status. The control can then be started manually (by turning on or off, reset-
ting or changing the RUN/STOP switch from RUN to STOP and back to RUN).
If an error occurs during the project, the red LED H4 on channel 2 of the PLC will go on.
If there is a new project on the CF module in which only the files for the standard PLC
have been changed, that is, the project check sum between the CF module and the safety
PLC correspond with one another, it will be possible to transfer the project from the CF
module to the control by force by doing the following. To do this, the safety PLC will have
to be in “STOP” status and the standard PLC will have to be in “STOP” or “ON” status.
The transfer is started by a short push and entering the release code (3 digit), as de-
scribed above.
11.9.4 Data transfer from the control to the card
Once the user has pushed the S1 button on the CF module and the S1 button on
channel 2 of the PLC simultaneously and held them down for a long time (> 3 s), LED H4
(green) on channel 2 of the PLC will blink and will wait for the copying code (2-digit) to be
entered.
NOTICE!
When the user starts the entry process of the release code by briefly pushing the S1
button on the CF module and the S1 button on channel 2 of the PLC, the safety PLC
will be in practically the same status as during the power-on procedure, that is, online
communication at the safety PLC will no longer be possible until one of the end sta-
tuses has been reached. Online communication at the PLC will be possible, although
the project-related commands (download, activated, reset, run, stop) will be blocked.
NOTICE!
Before using a compact flash card for the
first time
, the user must create on this
memory card the following directory structure (e.g. with a card reader connected to a
PC):
m
SYS00001\SAF02_00\V000\AppSt
m
SYS00001\SAF02_00\V000\Applic
All files both for the standard PLC and for the safety PLC part are copied at restoring
from the CF card and storing to the CF card respectively.
The files of the standard PLC part are in the subdirectory „AppSt“ and the files of the
safety PLC part are in the subdirectory „Applic“.
Summary of Contents for b maXX BMC-M-SAF-02
Page 119: ......