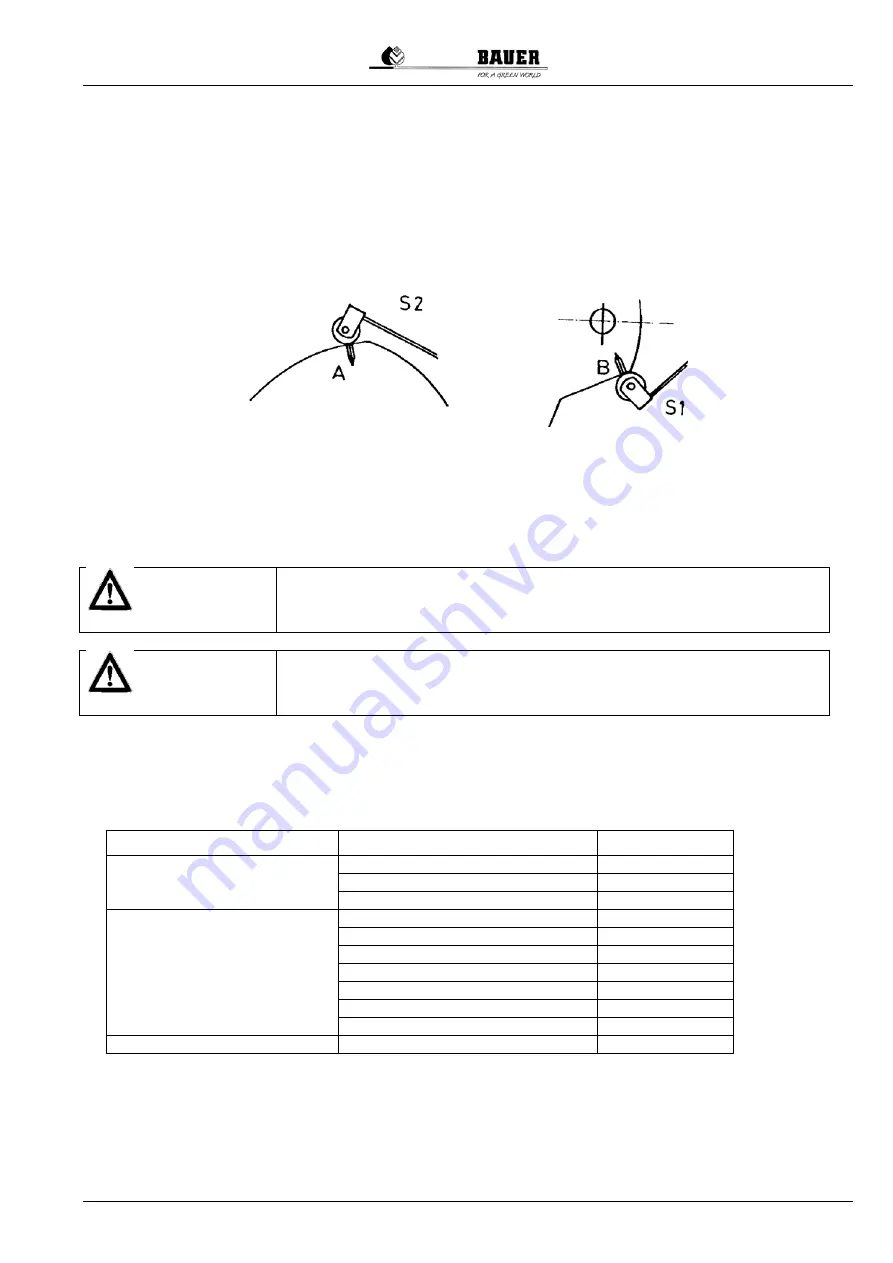
Operating Manual for
BAUER LINESTAR 9000 with hose feed
35
2. Control switch: twist the switch cam until the switch roller touches notch „A“. Move the switch in the bolt
holes towards the switch cam until the control switch (
microswitch
) responds (
clicks
), the bracket of the
switch lying next to the switch housing. Fix the switch with the screws in this position.
3. Safety switch: twist the control cam until the switch roller touches notch „B“. Move the switch toward the
cam until it responds (
clicks
), the bracket of the switch lying next to the switch housing. Fix the switch with
the screws in this position.
4. Check the switching points, repeat adjustment if necessary.
A periodical check and re-adjustment (
if necessary
) of the exact switching points of the micro-switches is obligatory
to guarantee a trouble-free operation of the machine.
14 ELECTRICAL SYSTEM
WARNING !
System is powered by 230 Volts and 400 Volts (460 Volts) !
All installation and service work must be performed with extreme care by
an expert person - in strict compliance with the relevant safety codes !
WARNING !
All electrical installation to be carried out ONLY after powering off the
complete system!
14.1
CABLES AND MARKINGS
1. The pivot cable consists of 11 phases which are marked by colours.
Phase colour
Phase number
Power circuit
Black
1
Blue 2
Brown 3
Control circuit
Pink
4
Grey 5
Red 6
White 7
Violet 8
Green 9
Orange 10
Grounding conductor
yellow/green
2. Cable
lengths
The cables are already cut to length and stripped at their ends at the manufacturer’s. Cables are long enough
to enter the alignment controls in a slight loop.
3. Mounting the cables
On the tower side of the span, where the alignment control has been mounted on the end pipe, the cable end is
Summary of Contents for LINESTAR 9000
Page 1: ...OPERATING MANUAL for BAUER LINESTAR 9000 with hose feed Version XII 2013 850 9898 ...
Page 82: ...74 Operating Manual for BAUER LINESTAR 9000 with hose feed ...
Page 94: ...86 Operating Manual for BAUER LINESTAR 9000 with hose feed 23 4 LINESTAR LINEAR CONTROL ...
Page 101: ...Operating Manual for BAUER LINESTAR 9000 with hose feed 93 ...
Page 104: ...96 Operating Manual for BAUER LINESTAR 9000 with hose feed 23 5 5 END TOWER BOX STANDARD ...
Page 106: ...98 Operating Manual for BAUER LINESTAR 9000 with hose feed 23 5 7 END TOWER BOX WITH END STOP ...
Page 110: ...102 Operating Manual for BAUER LINESTAR 9000 with hose feed 23 6 BOOSTER PUMP FOR END GUN ...