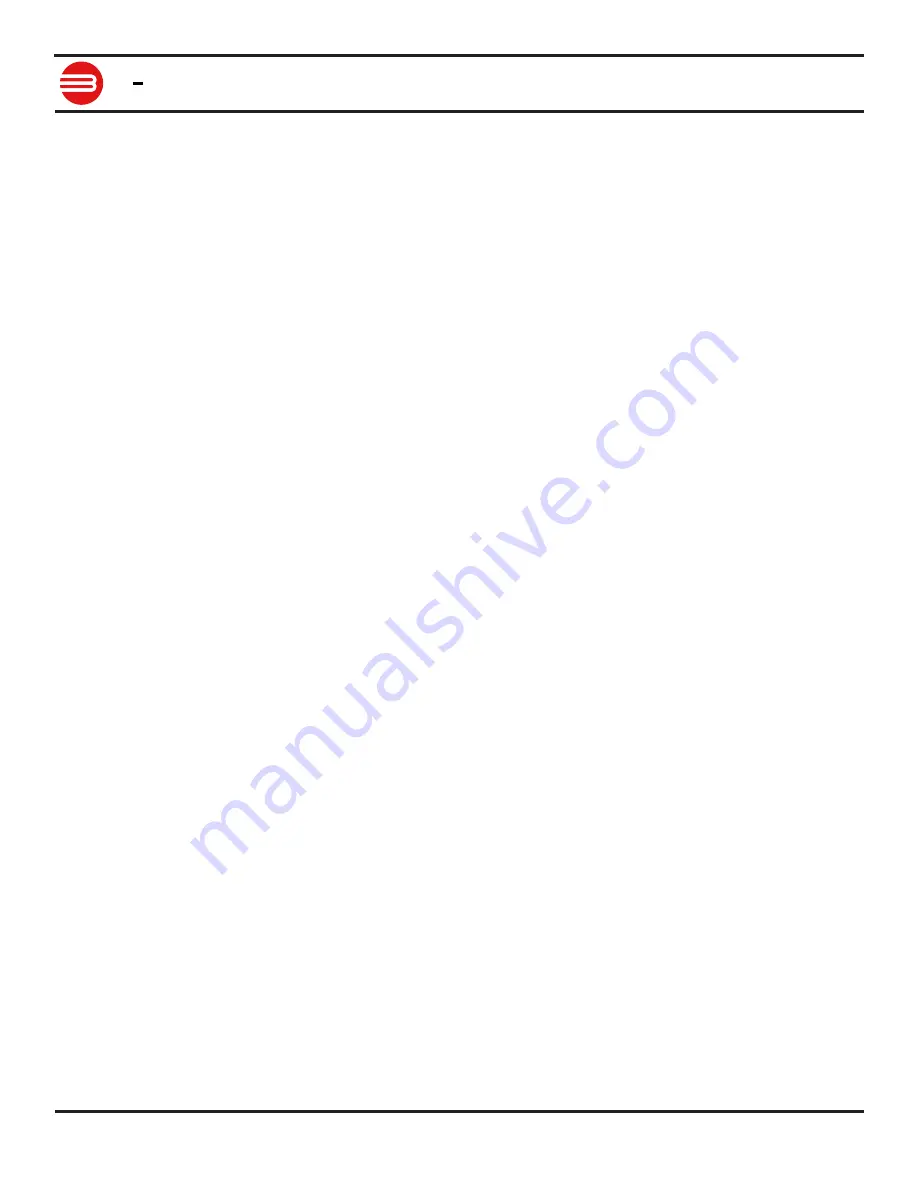
RoboClaw Series
Brushed DC Motor Controllers
RoboClaw Series User Manual
13
BASICMICRO
Hardware Overview
I/O
RoboClaw's I/O is setup to interface to both 5V and 3.3V logic. This is accomplished by internally
current limiting and clipping any voltages over 3.3V. RoboClaw outputs 3.3V which will work with
any 5V or 3.3V logic. This is also done to protect the I/O from damage.
Headers
RoboClaws share the same header and screw terminal pinouts across models in this user
manual. The main control I/O are arranged for easy connectivity to control devices such as
R/C controllers. The headers are also arranged to provide easy access to ground and power for
supplying power to external controllers. See the specific model of RoboClaw's data sheet for
pinout details.
Control Inputs
S1, S2, S3, S4 and S5 are setup for standard servo style headers I/O(except on ST models),
+5V and GND. S1 and S2 are the control inputs for serial, analog and RC modes. S3 can be used
as a flip switch input when in RC or Analog modes. Additionally, in all modes, S3, S4 and S5
can be used as emergency stop inputs or as voltage clamp control outputs. When set as E-Stop
inputs they are active when pulled low and have internal pullups so they will not accidentally trip
when left floating. S4 and S5 can also optionally be used as home signal inputs. The pins closest
to the board edge are the I/0s, center pin is the +5V and the inside pins are ground. Some RC
receivers have their own supply and will conflict with the RoboClaw’s 5v logic supply. It may be
necessary to remove the +5V pin from the RC receivers cable in those cases.
Encoder Inputs
EN1 and EN2 are the inputs from the encoders on pin header versions of RoboClaw. 1B, 1A, 2B
and 2A are the encoders inputs on screw terminal versions of RoboClaw. Channel A of both EN1
and EN2 are located at the board edge on the pin header. Channel B pins are located near the
heatsink on the pin header. The A and B channels are labeled appropriately on screw terminal
versions.
When connecting the encoder make sure the leading channel for the direction of rotation is
connected to A. If one encoder is backwards to the other you will have one internal counter
counting up and the other counting down. Refer to the data sheet of the encoder you are using
for channel direction. Which encoder is used on which motor can be swapped via a software
setting.
Logic Battery (LB IN)
The logic side of RoboClaw can, optionally, be powered from a secondary battery wired to LB IN.
The positive (
+
) terminal is located at the board edge and ground (
-
) is the inside pin closest to
the heatsink. On older RoboClaws that have it, remove the LB-MB jumper if a secondary battery
for logic will be used.
BEC Source (LB-MB)
RoboClaw logic requires 5VDC which is provided from the on board BEC circuit. On older
model RoboClaws the BEC source input is set with the LB-MB jumper. Install a jumper on the
2 pins labeled LB-MB to use the main battery as the BEC power source. Remove this jumper
if using a separate logic battery. On models without this jumper the power source is selected
automatically.