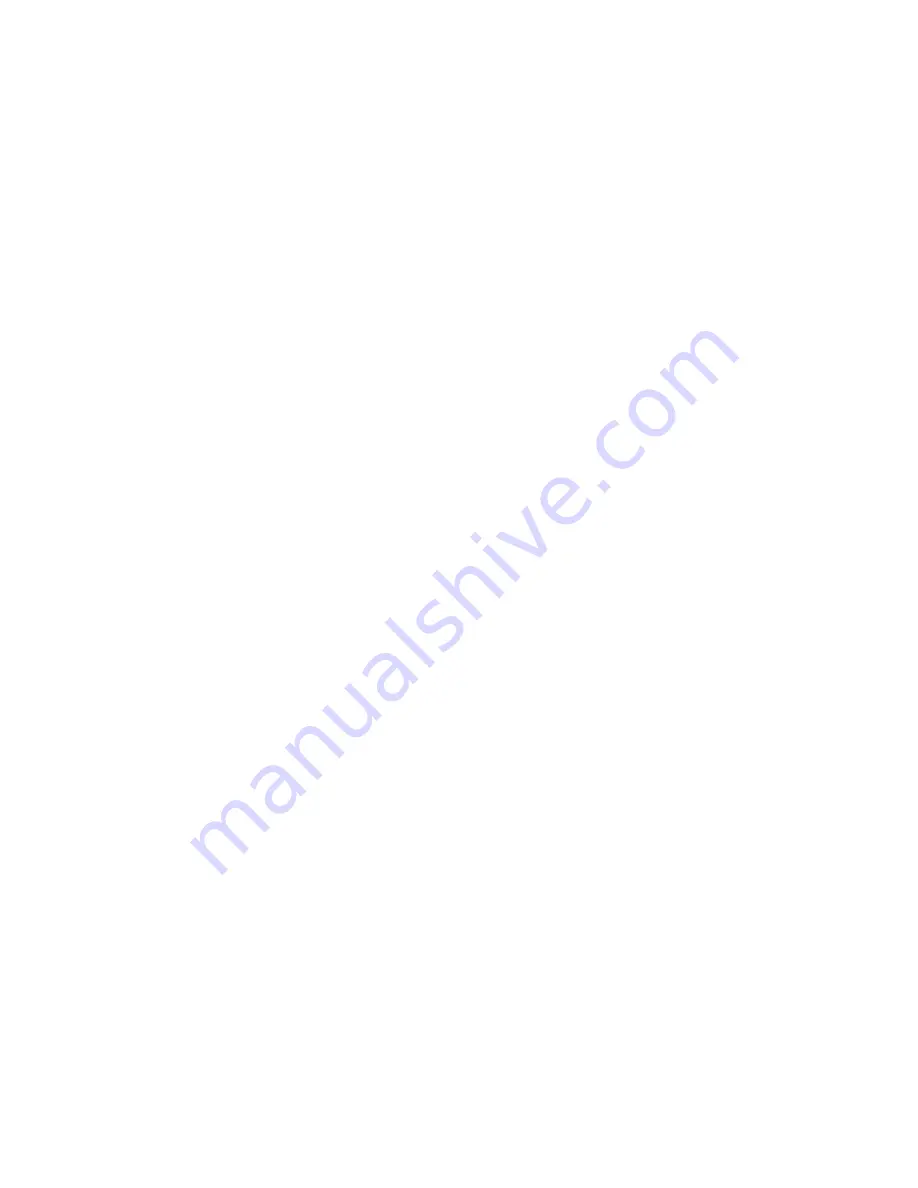
BH8-Series – User’s Manual
www.barrett.com
© 2007 Barrett Technology®, Inc.
Document: D3000, Version: AF.00
Page 71 of 82
Θ
Θ
Θ
Θ
−
=
Θ
Θ
Θ
Θ
Θ
Θ
Θ
Θ
Θ
4
3
2
1
31
21
11
33
32
23
22
12
12
0
35
/
2
0
0
0
0
0
0
35
/
2
0
0
0
0
375
/
4
0
0
0
0
0
0
0
0
375
/
4
0
0
0
0
0
0
0
0
375
/
4
0
0
0
0
M
M
M
M
Equation 5 - Motor to Joint Angle Transform after TorqueSwitch™
Activation
Equation 5 is only valid after Breakaway. Once the finger stops, the end tip position cannot be
accurately determined until the TorqueSwitch™ mechanism is reset. Reset the TorqueSwitch™
by opening the finger.
Note: The feedback device for each of the motors uses a 90 line, or 360 count, encoder. Thus, the
motor angle is the encoder position.
9.6 Joint Motion Limits
The maximum joint motion limits for the BarrettHand™ are calculated based on the zero position
seen in Figure 29. Depending on the position of the spread joint,
Θ
11
, and the objects in the grasp,
the maximum joint motion limits for the finger links may vary.
The inner link,
Θ
12
,
Θ
22
,
Θ
32
, has a maximum joint motion limit of 140
°
with no object blocking
movement and
Θ
11
in the full close or open position. The outer link,
Θ
13
,
Θ
23
,
Θ
33
, has a
maximum joint motion limit of 48
°
when
Θ
11
is fully open or closed and there is no object in the
grasp, as shown in Figure 31. When the spread is in any position other than full open or close, the
fingers may not have the full range of motion due to interference with other fingers.