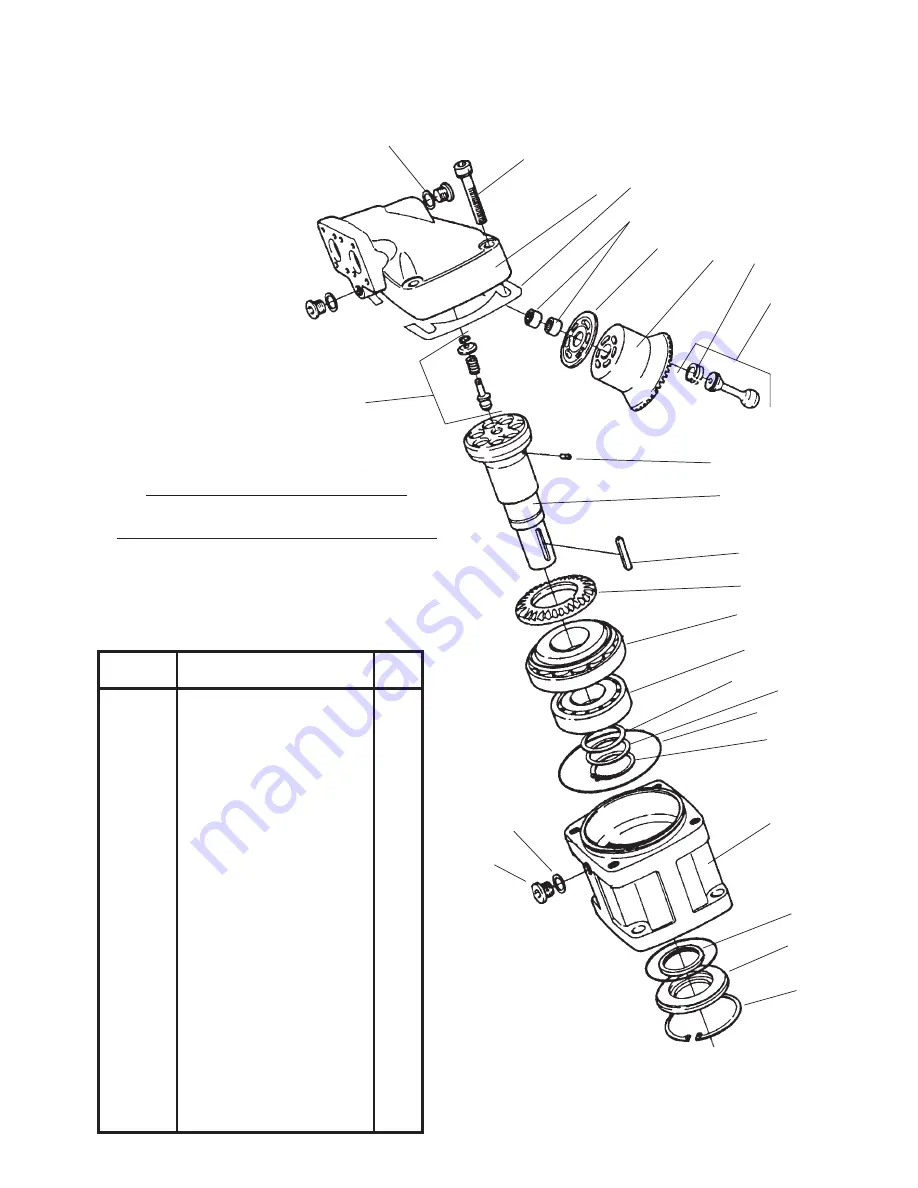
page 92
page 92
page 92
page 92
page 92
375 SE
800-00162
MOTOR MAINTENANCE (F12 SWING)
MOTOR MAINTENANCE (F12 SWING)
MOTOR MAINTENANCE (F12 SWING)
MOTOR MAINTENANCE (F12 SWING)
MOTOR MAINTENANCE (F12 SWING)
ITEM NO. DESCRIPTION QTY.
ITEM NO. DESCRIPTION QTY.
ITEM NO. DESCRIPTION QTY.
ITEM NO. DESCRIPTION QTY.
ITEM NO. DESCRIPTION QTY.
1
ASSEMBLY, barrel housing
1
2
SCREW, set
1
3
VALVE PLATE
1
4
WASHER, seal
1
5
BEARING HOUSING
1
6
O-RING
1
7
O-RING
1
8
O-RING
1
9
SEAL CARRIER
1
10
SHAFT SEAL
1
11
RETAINING RING
1
12
BLEEDER PLUG
1
13
WASHER, seal
1
14
SHAFT
1
15
FLAT KEY
1
16
CYLINDER BARREL
1
17
NEEDLE BEARING
2
18
BARREL SUPPORT
1
19
ASSEMBLY, piston
7
20
PISTON RING
21
21
GUIDE PIN
1
22
RING GEAR
1
23
TAPERED ROLLER BEARING
1
24
CYLINDER BEARING
1
25
WASHER, spacer
1
26
WASHER, spacer
1
27
RETAINING RING
1
28
SHIM
2
29
SCREW, hex socket
4
1
11
11
3
33
33
14
14
14
14
14
15
15
15
15
15
16
16
16
16
16
17
17
17
17
17
18
18
18
18
18
19
19
19
19
19
20
20
20
20
20
21
21
21
21
21
22
22
22
22
22
23
23
23
23
23
24
24
24
24
24
6
66
66
25
25
25
25
25
26
26
26
26
26
27
27
27
27
27
28
28
28
28
28
12
12
12
12
12
13
13
13
13
13
29
29
29
29
29
4
44
44
11
11
11
11
11
9
99
99
10
10
10
10
10
5
55
55
MOTOR ASSEMBLY DRAWING
MOTOR ASSEMBLY DRAWING
MOTOR ASSEMBLY DRAWING
MOTOR ASSEMBLY DRAWING
MOTOR ASSEMBLY DRAWING
FOR REFERENCE WHEN SERVICING
FOR REFERENCE WHEN SERVICING
FOR REFERENCE WHEN SERVICING
FOR REFERENCE WHEN SERVICING
FOR REFERENCE WHEN SERVICING